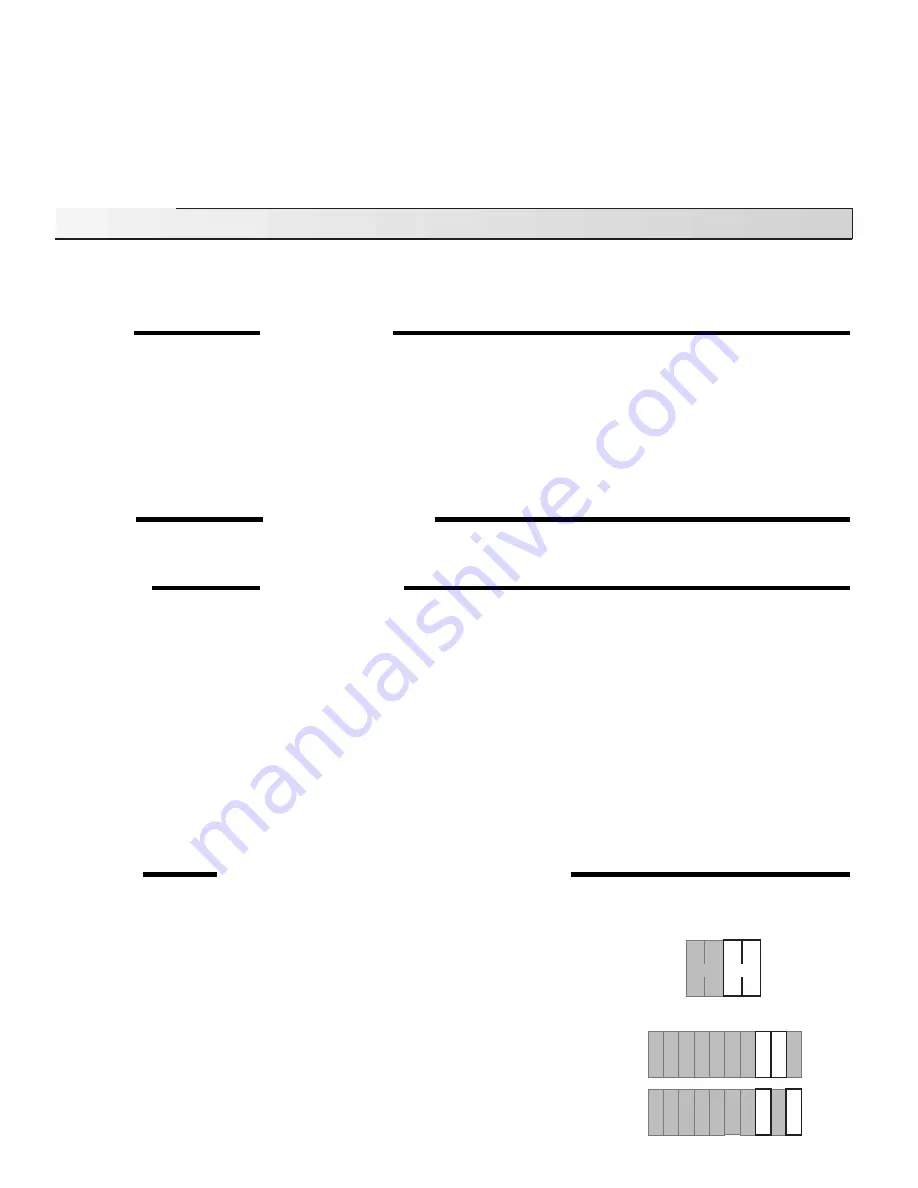
6
Exercising Procedure
The 368 first exercises the zone valves or pumps. If a zone valve or zone pump has not been operated in the past 3 days, the 368
turns on the zone relay for 10 seconds.
Note The zone relay exercising time is increased to 3 minutes if the DIP switch is set to
Thermal Motor.
After the zone valves or pumps have been exercised, the 368 exercises the system pump. If the system pump has not operated
in the past 3 days, the 368 turns on the
System Pmp relay for 10 seconds.
Once the exercising procedure is complete, the 368 returns to its normal operating sequence.
Installation
Caution
Improper installation and operation of this control could result in damage to the equipment and possibly even
personal injury. It is your responsibility to ensure that this control is safely installed according to all applicable codes
and standards. This electronic control is not intended for use as a primary limit control. Other controls that are
intended and certified as safety limits must be placed into the control circuit.
STEP ONE
GETTING READY
Check the contents of this package. If any of the contents listed are missing or damaged, please contact your wholesaler or tekmar sales
representative for assistance.
Type 368 includes:
• One Zone Control 368
• Data Brochures D 368, D 001
• Application Brochures A 368
Other information available:
• Essays
Note Carefully read the details of the Sequence of Operation sections in all applicable brochures to ensure that you have chosen the
proper control for your application.
STEP TWO
MOUNTING THE BASE
Remove the control from its base by pressing down on the release clip in the wiring chamber and sliding the control upwards. The base
is then mounted in accordance with the instructions in the Data Brochure D 001.
STEP THREE
ROUGH-IN WIRING
All electrical wiring terminates in the control base wiring chamber. The base has standard 7/8" (22 mm) knockouts which accept common
wiring hardware and conduit fittings. Before removing the knockouts, check the wiring diagram and select those sections of the chamber
with common voltages. Do not allow the wiring to cross between sections as the wires will interfere with safety dividers which should
be installed at a later time.
Power must not be applied to any of the wires during the rough-in wiring stage.
• If a 10K Indoor Sensor is used for any zone, install the Indoor Sensor(s) according to the instructions in the Data Brochure 074 and
run the wiring back to the control.
• If a 10K RTU is used, install the RTU(s) according to the installation instructions provided in the Data Brochure D 054 and run the
wiring back to the control.
• If multiple Zone Controls are used, run two wires from one Zone Control to the next to create a chain.
• Run wires from the 120 V (ac) power to the control.
Use a clean power source to ensure proper operation. Multi-strand 16 AWG
wire is recommended for all 120 V (ac) wiring due to its superior flexibility and ease of installation into the terminals.
• Run wires from the system pump and from each zone valve / pump to the control.
STEP FOUR
ELECTRICAL CONNECTIONS TO THE CONTROL
The installer should test to confirm that no voltage is present at any of the wires. Push the control into the base and slide it down until
it snaps in firmly.
Powered Input Connections
120 V (ac) Power
Connect the 120 V (ac) power supply to terminals
Power N — L (3 and 4).
Sensor and Unpowered Input Connections
Do not apply power to these terminals as this will damage the control.
Zone Control Input and Output
Connect a wire between the
Com Sen (13) terminals on each 368. Connect the Zo Out
(12) terminal on the first 368 to the
Zo In (14) terminal on the second 368. With several
Zone Controls, connect the
Zo Out (12) terminal on the second 368 to the Zo In (14)
terminal on the third 368 and continue this process for each additional 368. The
Zo Out
Com
Sen
UnO
Sw
5 6
RTU
1
12
11
13
Com
Sen
14
Zo
In
Zo
Out
RTU
2
7
RTU
3
9
RTU
4
10
8
Com
Sen
Com
Sen
UnO
Sw
5 6
RTU
1
12
11
13
Com
Sen
14
Zo
In
Zo
Out
RTU
2
7
RTU
3
9
RTU
4
10
8
Com
Sen
3
1 2
N
L
Pmp
4
Power
Pmp
System