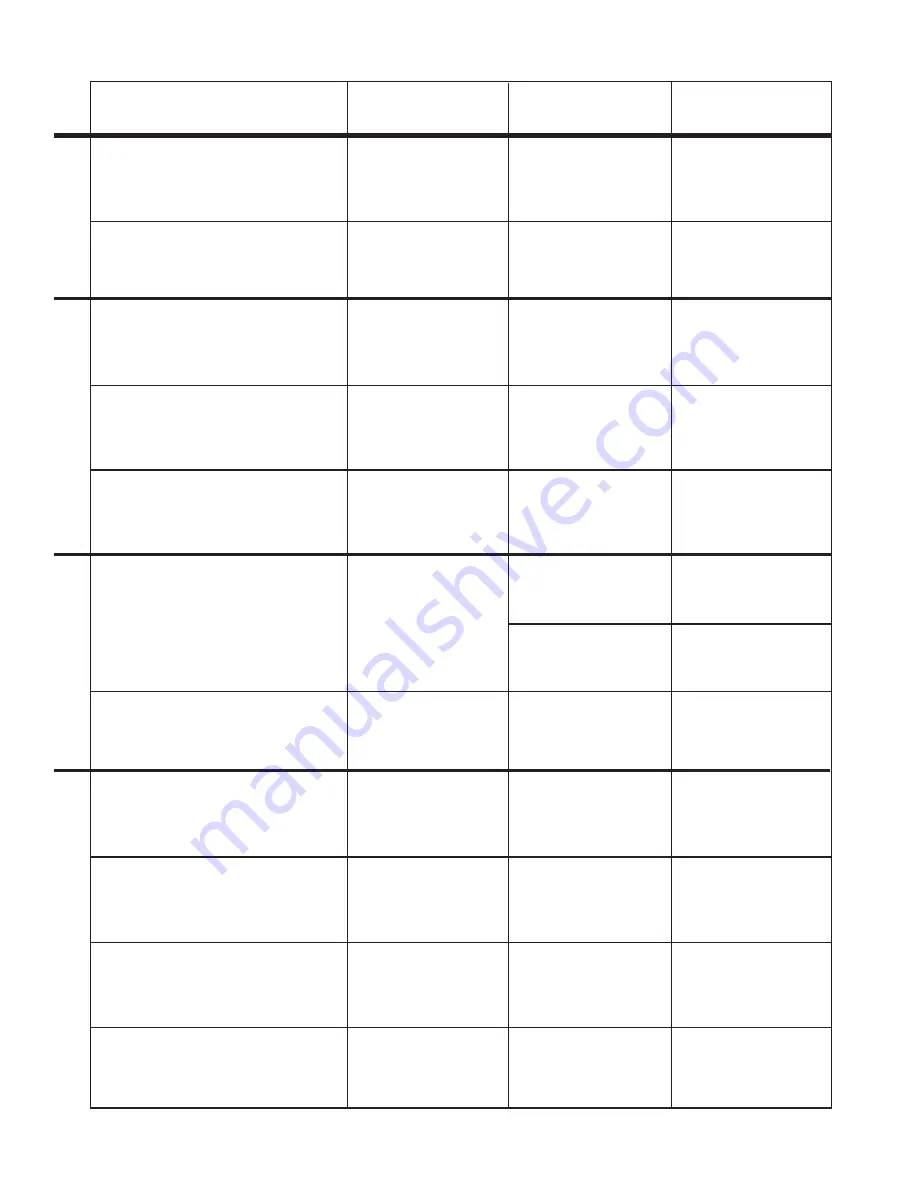
6
Type & Purpose
REDUCED PRESSURE ZONE
BACKFLOW PREVENTER
For High Hazard Cross-connections and
continuous pressure application.
REDUCED PRESSURE DETECTOR ASSEMBLY
High Hazard
DOUBLE CHECK VALVE ASSEMBLY
For Low Hazard Cross-connections and
continuous pressure applications.
DOUBLE CHECK DETECTOR ASSEMBLY
Low Hazard
DUAL CHECK VALVE
BACKFLOW PREVENTER
For low hazard cross-connections.
Continuous pressure applications.
SPECIALTY BACKFLOW PREVENTERS with
INTERMEDIATE ATMOSPHERIC VENT
For low hazard cross-connections in small
pipe sizes. Continuous pressure applications
LABORATORY FAUCET DUAL CHECK VALVE
with INTERMEDIATE VACUUM BREAKER
In small pipe sizes for low hazard
ATMOSPHERIC VACUUM BREAKERS
For high hazard cross-connections not
subject to continuous pressure
- 6" above fl ood rim.
PRESSURE VACUUM BREAKERS
For high hazard cross-connections.
Continuous pressure applications -12" above
fl ood rim.
ANTI-SIPHON, ANTI-SPILL
VACUUM BREAKER
1" above fl ood rim Factory installed
6" above fl ood rim Field installed
HOSE CONNECTION VACUUM BREAKERS
For residential and industrial hose supply outlets
not subject to continuous pressure
Description
Two independent check
valves with intermediate
relief valve. Supplied
with shutoff valves and
ball type test cocks
RPZ valve backfl ow
preventers with a
water meter and RPZ in
bypass line.
Two independent check
valves. Checks are
replaceable for
repair & testing.
Double check valve
backfl ow preventers with a
water meter and double
check in by pass line.
Two independent check
valves. Checks are
replaceable for
repair & testing.
Two independent check
valves with intermediate
vacuum breaker and
relief vent.
Two independent check
valves with intermediate
vacuum breaker and
relief vent.
Single fl oat and disc
with large atmospheric port
Spring loaded single fl oat
and disc with independent
1st check. Supplied with shutoff
valves and ball type
test cocks.
Anti-spill vacuum breaker with
modular check & fl oat assembly
of thermo plastic Housing
bronze body
Single check with
atmospheric vacuum
breakers vent.
Installed At
All cross-connections subject to
backpressure or back siphonage
where there is a high potential
health contamination.
Continuous pressure.
Fire protection system supply
main. Detects leaks and
unauthorized use of water.
All cross-connections subject to
backpressure or back siphonage
where there is a low potential
health contamination.
Continuous pressure.
Fire protection system supply main.
Detects leaks an unauthorized use
of water.
Cross-connections where there
is a low potential health hazard
and moderate
fl ow requirements
Cross-connections subject to
backpressure or backsiphonage
where there is low health hazard.
Continuous pressure.
Pressure outlet to prevent
backfl ow of carbon dioxide gas
and carbonated water into the
water supply system to
beverage machines
Cross-connections subject to
backpressure or backsiphonage
where there is low health hazard.
Cross-connection not subject to
backpressure or continuous
pressure. Install at least 6" above
fi xture rim. Protection against
backsiphonage only.
Valve is designed for installation
in a continuous pressure potable
water supply system 12" above
the overfl ow level of the system
being supplied. Protection
against backsiphonage only.
Indoor point of use
Install directly on hose bibbs,
service sinks and wall hydrants.
Not for continuous pressure.
Examples of
Installations
Main supply lines
Commercial boilers
Hospital equipment
Laboratory equipment
Waste digesters
Car washes
Fire Sprinkler Lines
Main supply lines
Food cookers
Tanks & Vats
Lawn Sprinklers
Fire Sprinkler Lines
Commercial Pools
Fire Sprinkler Lines
Residential Supply Lines
(at the meter)
Residential fi re sprinkler systems
Boilers (small)
Cooling towers (small)
Dairy equipment
Post-Mix Carbonated
Beverage Machine
Laboratory Faucets and
Pipe Lines
Barber shop and
Beauty Parlor sinks
Process Tanks
Dishwashers
Soap Dispensers
Washing Machines
Lawn Sprinklers
Laboratory equipment
Cooling towers
Commercial Laundry Machines
Swimming Pools
Chemical Planting tanks
Lawn Sprinklers
Chemical Dispenser
Commercial Dishwasher
Sterilizers
Hose bibbs
Service sinks
Hydrants
1
2
3
4
For additional cross-connection control information, send for F-50 brochure.
For Basic Types of Backflow Preventers
RP-IS-709_709DCDA.indd 6
9/26/08 2:28:15 PM