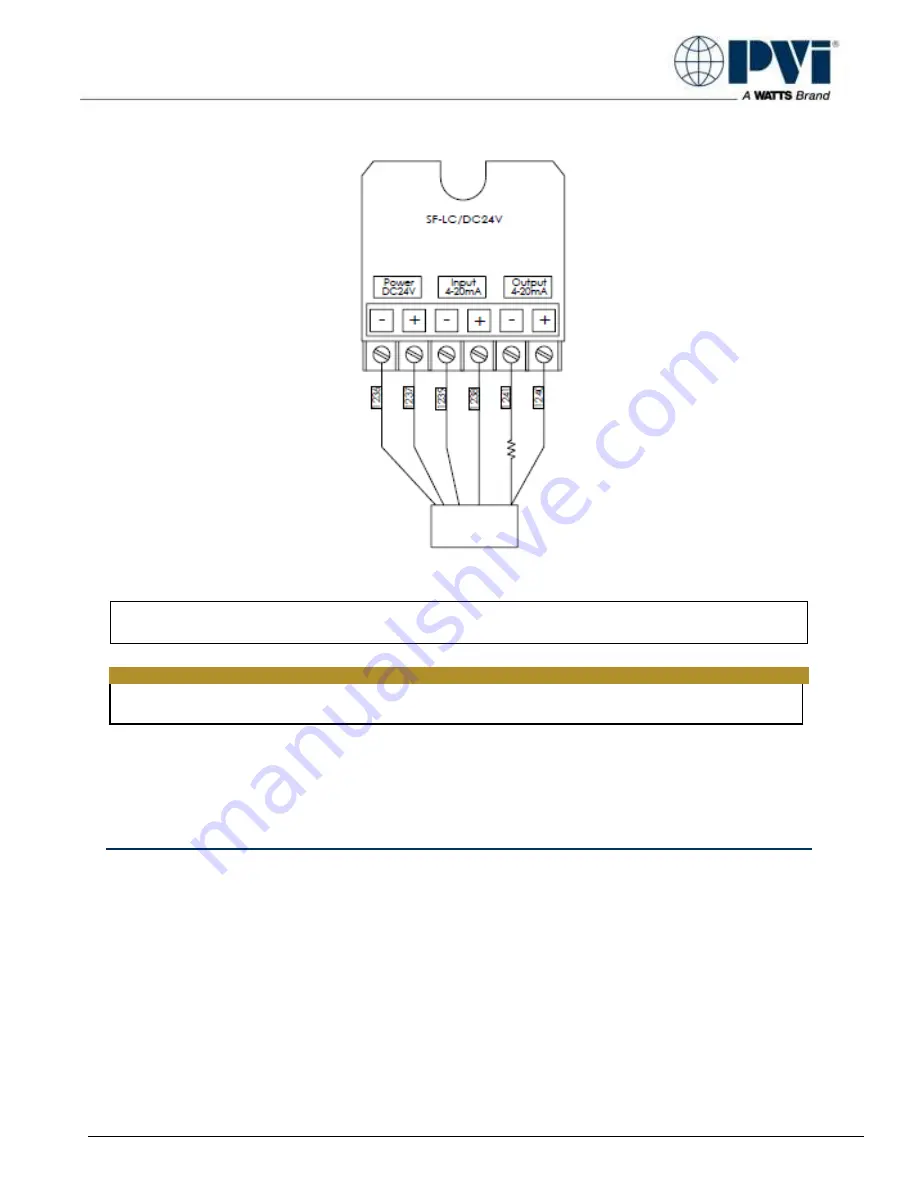
OMM-0153_E
• 5/11/2023 Technical Support • (800) 526-0288 • Mon-Fri, 8 am - 5 pm EST Page 87 of 124
CENTURION Installation, Operation & Maintenance Manual
SECTION 8: WATER HEATER MANAGEMENT
The components on the PC board include DIP switches which are preset at the factory and
should not be changed unless instructed to do so.
Figure 8-16: Actuator PC Board Components
NOTE: DO NOT press Auto-Stroke (Reset) button
. Doing so may alter actuator calibration.
Depress and hold brass clutch button to manually rotate valve.
C A U T I O N !
Power must be removed from the Actuator prior to attempting to manual override. Failure to
observe this precaution may damage the Actuator.
A manual override is provided for use in setup or power failure situations. The override is
operated with a standard hex wrench (included). To manually open or close the valve,
disconnect the 5-pin connector on the Actuator to ensure 24 VDC power is not supplied.
8.10.1 Sequencing Valve Operating Characteristics
The Sequencing Valve is powered by 24 VDC power supply. The unit has a 5-pin molex valve
harness and the valve has a mating 5-pin plug and play connector. The 5 pins are:
1. +24VDC
2. -24VDC
3. 4-20mA (Control Signal)
4. Common
5. 0-10V (Feedback)
During normal Water Heater Management (WHM), a control signal of less than (<)
– 4mA will
rotate the valve to the fully open (90°) position. Conversely, a control signal of 20 mA will rotate
the valve to the fully closed (0°) position. The Sequencing Valve will send a status of the Valve
(open/close) as a feedback signal (0
–10 VDC) to the Edge Controller.