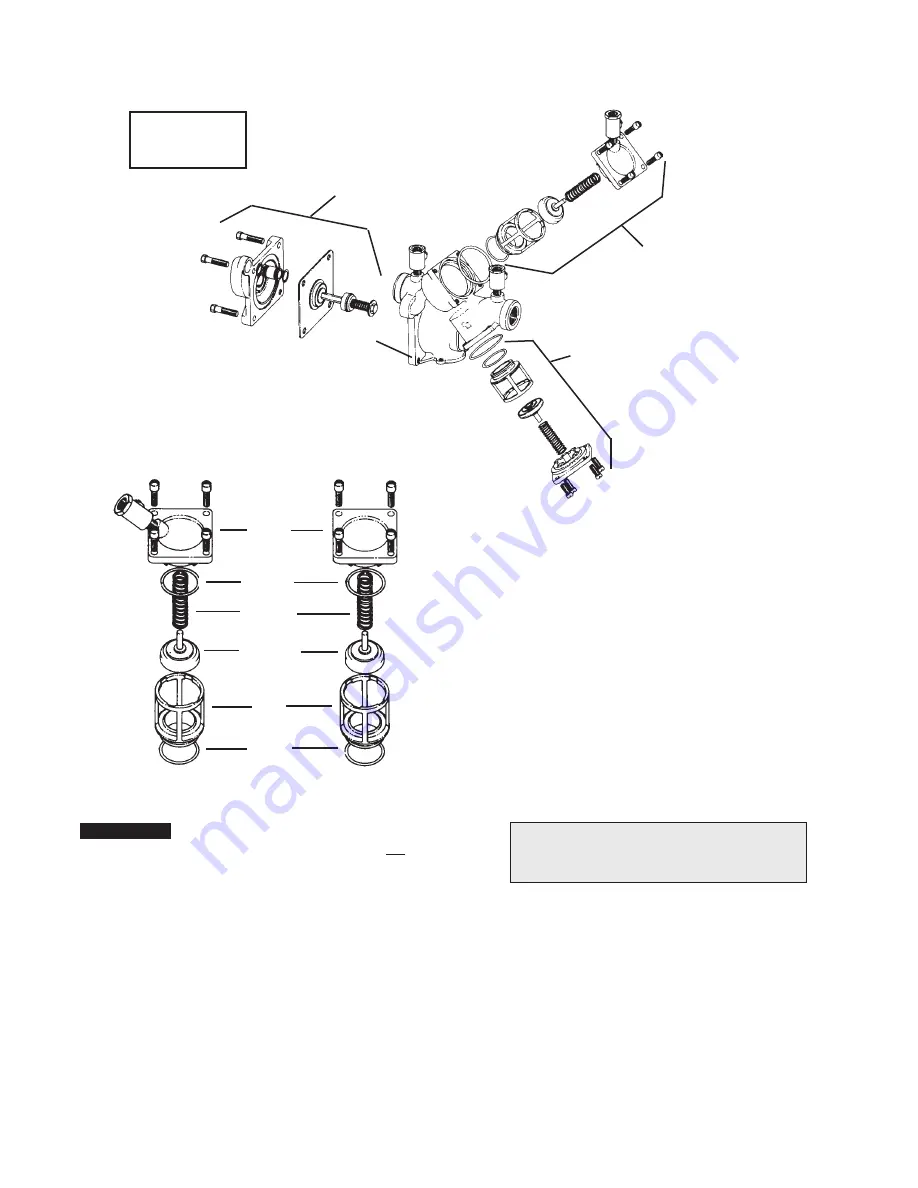
5
NOTICE
The springs and covers of the first and second check valves are
not
interchangeable. The heavier spring loaded module should be in the first
check and the lighter in the second check module.
Cover
Cover
O-ring
Spring
Disc
Assembly
Seat
Seat
O-ring
First Check
Second Check
Servicing First and Second Check Valves
3
/
4
" to 2"
No special tools
required to service
Series 909/LF909
First Check
Service Parts Kit
Second Check
Service Parts Kit
Body
Relief Valve
Service Parts Kit
For repair kits and parts, refer to our Backflow
Prevention Products Repair Kits & Service Parts
price list PL-RP-BPD found on
www.watts.com.
1. Remove the four screws holding the first check valve cover.
2. Lift off the first check valve cover. The check valve inside will
come out with the cover and is attached with a bayonet type
locking arrangement.
3. Holding the check valve module in both hands, rotate the
assembly quarter turn. This will disengage the disc assembly,
spring and seat cover into individual components.
4. The disc assembly may be cleaned and reassembled, or
depending upon its condition, it may be discarded and replaced
with a new assembly from theservice kit. O-rings should be
cleaned or replaced as necessary and lightly greased with the
FDA approved silicon grease which is also furnished with the
service kit.
5. Reassemble the check valve module in the reverse order.
Service is identical for both the first and second check valves.
For further details contact your local technical sales rep-
resentative.