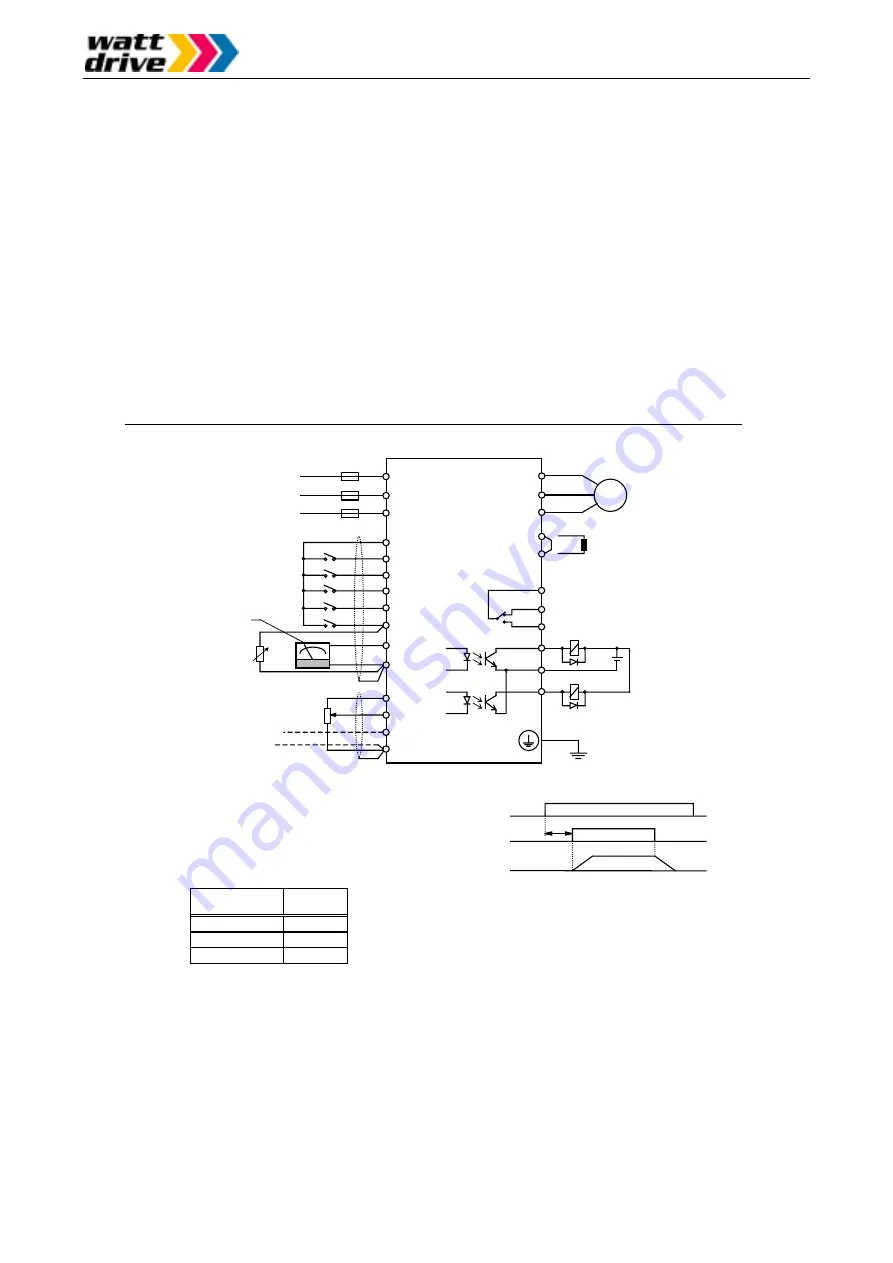
Appearance and names of parts
Page 17 / 52
Notes on technical specifications:
Note 1
: Protective structure is based upon EN60529
Note 2
: The applicable motor is a WATT DRIVE standard four-pole motor. When using
another motor, make sure that the rated motor current does not exceed the rated inverter
current.
Note 3
: The output voltage will decrease if input voltage decreases.
Note 4a
: The initial data setting values of 005N/011N are same as 007N/015N. So be sure
to set the correct values under
b 12
and
b 22
of 005N/007N for each motor first.
Note 4b
: The initial data setting value of 030H is same as 040H. So be sure to set the
values under
b 12
and
b 22
of 030H for the motor first.
Note 5
: Confirm with the motor manufacturer the motors maximum rpm when using a motor
running at frequencies higher than 50/60Hz
Note 6
: Torque will be reduced when the base frequency exceeds 50Hz.
Note 7
: In the range of 40 to 50°C reduce the carrier frequency to 2kHz and derate the
output current to 80% of the rated current, and remove the top cover.
Power supply
(three phase)
50/60 Hz
Fuses
L2000 series
inverter
L1 (L1)
L2
L3 (N)
T1 (U)
T2 (V)
T3 (W)
1
2
3
4
5
L
P24
H
O
OI
L
FM
AL0
AL1
AL2
11
CM2
12
Motor
+1
+
Ground
Alarm signal
(relay output)
°
C
Thermistor
Frequency
monitor
Set value input
4 – 20 mA
Analog set value 0 – 10V
(Pot 1k – 2k Ohm)
Power supply
Running command
Output frequency
> 2 s
The common potential depends
on the terminals used:
Terminals
Common
potential
1, 2, 3, 4, 5
P24
FM, H, O, OI
L
11, 12
CM2
Notes:
24VDC
Short bar must be removed
if the inductor is connected
A trip will occur when a running command is active at the time the
power supply is switched on. The power supply should not be
switched on simultaneously with the running command; instead
there should be a time delay of about 2 seconds from the time the
power supply is switched on until the running command is activated
(refer to time diagram). Also the power supply must not be switched
off while the running command is being active (motor is running).