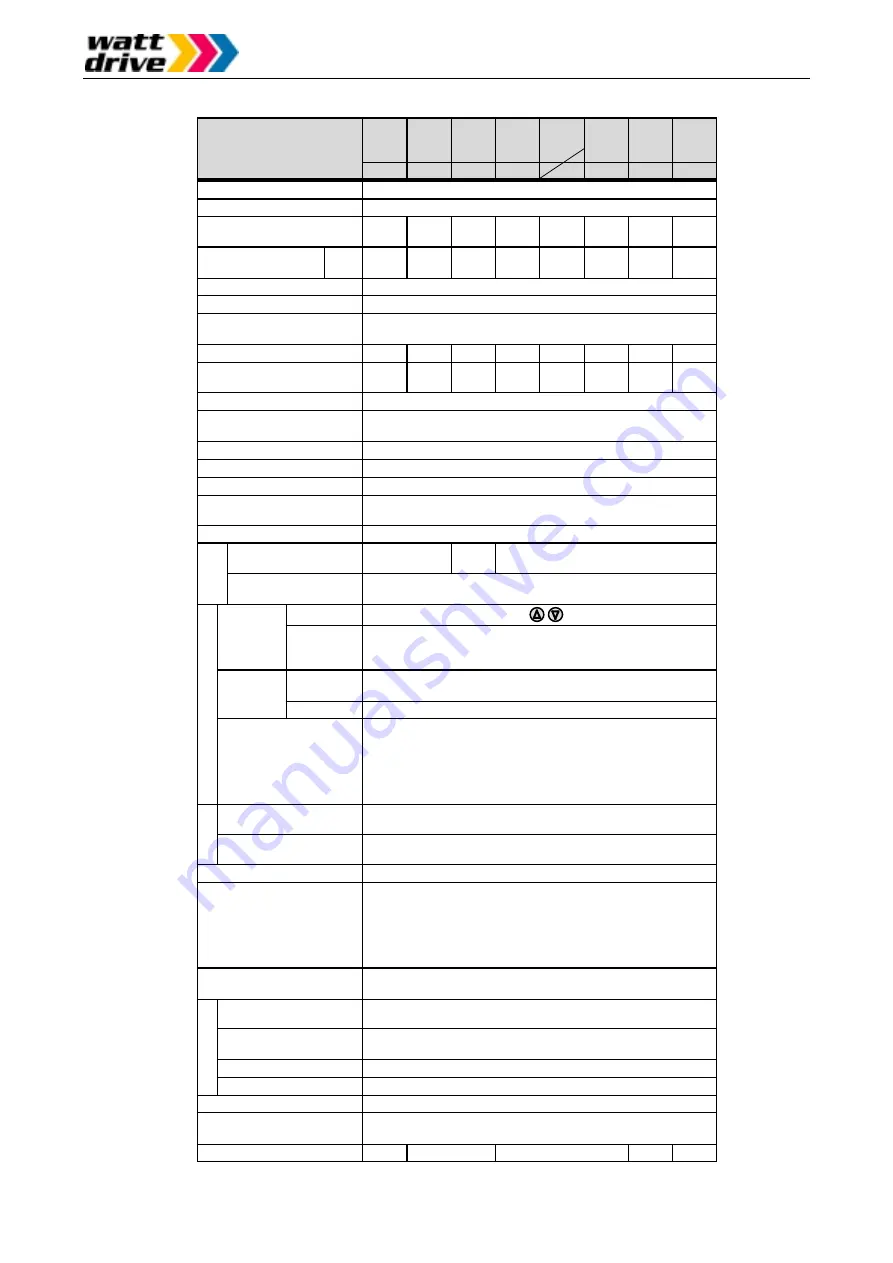
Appearance and names of parts
Page 16 / 52
004
HFE
007
HFE
015
HFE
022
HFE
030
HFE
040
HFE
055
HFE
075
HFE
Inverter L 2 0 0 0
-
(400V series)
Protective structure (
Note 1
)
IP20
Overvoltage category
III
Maximum motor size (4P)
in kW (
Note 2
)
0.4
0.75
1.5
2.2
3.0
4.0
5.5
7.5
Maximum capacity
in kVA
460V
1.1
1.9
3.0
4.3
6.2
6.8
10.3
12.7
Input supply phase
004 ~ 075HF: 3 phase
Rated input voltage
380VAC –10% ~ 10% 50/60Hz +/-5%
Rated output voltage
(
Note 3
)
Three phase 380 ~ 460VAC
(Corresponds to input voltage)
Rated input current in A
2.0
3.3
5.0
7.0
10.0
11.0
16.5
20.0
Rated output current in A
(
Note 4b
)
1.5
2.5
3.8
5.5
7.8
8.6
13.0
16.0
Output frequency range
0.5 ~ 360 Hz (
Note 5
)
Frequency accuracy
(at 25°C +/-10°C)
Digital command: +/-0.01% of maximum frequency
Analog command: +/-0.2% of maximum frequency
Frequency setting resolution
Digital setting: 0.1
Hz Analog setting: maximum frequency /1000
Voltage/frequency characterist.
Constant or reduced torque with any variable voltage/frequency
Overload current capacity
150% during 60 seconds (once per 10 minutes)
Acceleration/deceleration time
0.1 ~ 3000 s in selectable linear and non-linear mode
(second acceleration/deceleration usable)
Starting torque
100% ore more (when torque boost has been set)
Dynam. braking, feedback
to capacitor (
Note 6
)
ca. 100%
ca.
70%
ca. 20%
DC injection braking
Braking is on at the minimum frequency or less (minimum
frequency, braking time and braking force can be set)
Dig. operator
Settings using keys or potentiometer
Frequency
setting
External
signals
0-10VDC (input impedance 10k Ohm)
4-20mA (input impedance 250 Ohm)
Potentiometer 1k-2k Ohm, 1W
Dig. operator
Via keys RUN (for start) and STOP/RESET (for stop)
(Default setting: forward run)
Forward /
Reverse run
(Start/Stop) Ext. signals
Intelligent input terminals configurable as FW and RV
Intelligent input terminals
programmable as
FW: Forward run start/stop
RV: Reverse run start/stop
CF1–CF4: Multistage speed
JG: Jogging command
AT: Analog current input selection
2CH: 2.Accel./decel. time
FRS: Free run stop
EXT: External trip
USP: USP function
RS: Reset
SFT: Software lock
PTC: Thermal protection
Intelligent output terminals
programmable as
FA1/FA2: Frequ. arrival signal RUN: Motor running signal
OL: Overload signal OD: PID deviation signal AL: Alarm signal
Frequency and current
monitoring
Connection of external analog meter (0-10VDC, max. 1mA) for
frequency or current; connection of external digital frequency meter
Fault alarm contact
On when the inverter trips (1c contact)
Other functions
Automatic voltage regulation,
retry;
analog gain/vias adjustment,
frequency jump,
upper/lower limiter,
output frequency display,
trip history monitoring,
carrier frequency setting,
PID control,
automatic torque boost,
and many more
Protection functions
Overcurrent, overvoltage, undervoltage, electronic thermal,
temperature abnormality, ground fault upon starting, overload limit
Ambient temperature
(
Note 7
)
-10 ~ 50°C
Storage temperature and
humidity
-25 ~ 70°C (during short term transportation period only)
20 ~ 90% RH (no dew condensation)
Vibration
Max. 5.9m/s
2
(=0.6g) at 10-55Hz
Installation location
1000m or less altitude indoors (IP54 or equivalent)
External color
Blue
Options
Remote operator, copy unit, cable for digital operator,
reactor for improving power factor, noise filter
Overall weight (approx.)
1.3
1.7
2.8
5.5
5.7
Br
aki
ng
to
rque
In
pu
ts
Ou
tp
ut
s
En
vi
ro
nm
en
ta
l.