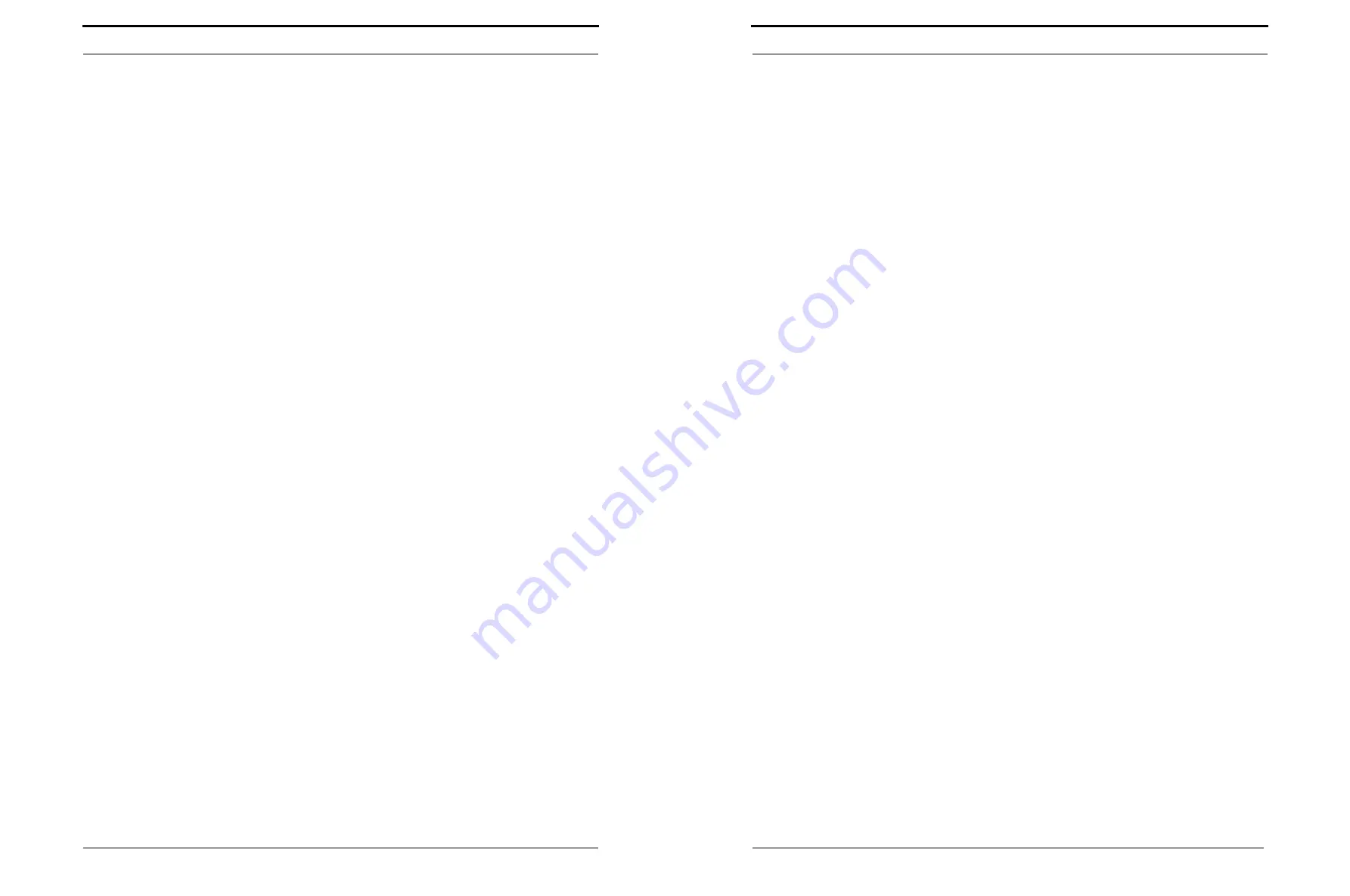
Machine Areas
20
Plockmatic PowerSquare™ 224 - Service Training Workbook
8.3
Gathering Area Module
The gathering area module accepts the paper from the connecting bridge.
When the correct number of sheets has arrived, tampers knock down the paper
between the sidelays and the endlays,
(see Section 8.4)
Locate the following in the Gathering Area (Top)
Bridge Interface PCB (900-278)
Tamper Stepper Motor PCB (900-277)
Main Drive Stepper Motor PCB (900-279)
Bridge Axis Motor Control PCB (900-212)
Gathering Area Loaded Optical Sensor
Gathering Area Flow Optical Sensor
Bridge axis home switch
Main drive proximity sensor
Locate the following in the Gathering Area (Bottom)
Gathering Area cover switch
Bridge axis motor
Main drive stepper motor
Tamper stepper motor
Tamper proximity sensor
Perform the following tasks:
ADJ 4.4.3 (Calibrate the Bridge Axis)
Machine Areas
Plockmatic PowerSquare™ 224 - Service Training Workbook
29
8.10
Machine Cycle Control
At this stage of the training, you understand how the machine works and how it
is controlled.
To see the full machine cycle, make a test book using the
TEST
screen.
Before you begin:
• Use the GUI to adjust the PSQ for the correct paper size, book thickness,
etc.
• Select 2 stitches.
• Place the paper in the gathering area.
Use the
TEST
screen to make a book:
• Motor Slow
• Pick-up - Shuttle x2
• Activate Rear Tamper x2
• 1st Stitch - Shuttle
• Stitch Wire On x2
• Incr Move - Shuttle
• Stitch Wire Off
• Park - Shuttle
• Fold x3
• Clamp
• Form (number of times depends on thickness of book)
• Clamp
• Eject x2
• Outfeed x2 (to drive the book onto the trim stop)
• Blade x3
• Trim Stop
• Outfeed
• Trim Stop
• Outfeed
• Stack Feed x2
• Motor Slow (to turn off the Motor Slow function)