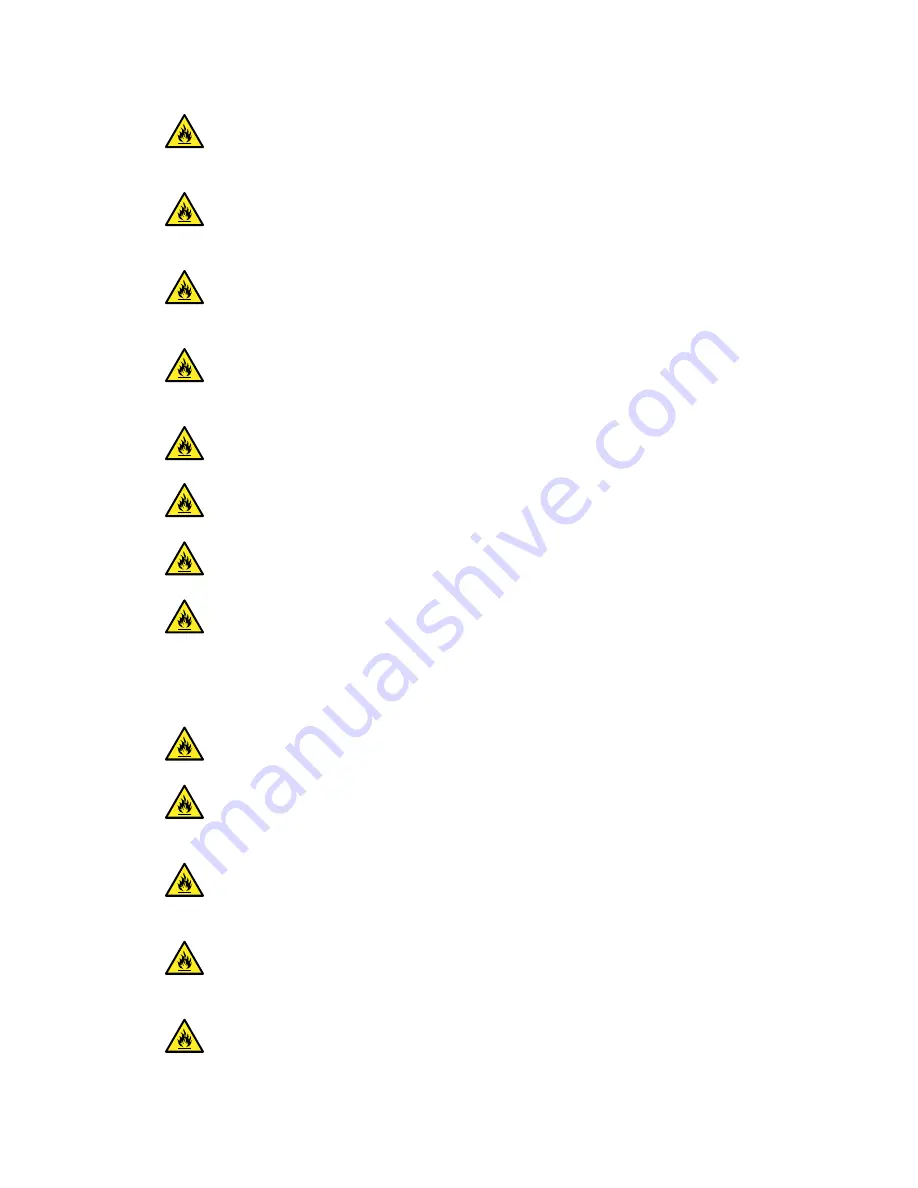
Avertissement :
pour éviter tout risque d'incendie, remplacez toujours les fusibles
par d'autres du type et de la puissance indiqués sur le panneau à proximité du
couvercle de la boite à fusible de l'instrument.
Warnung:
Zum Schutz gegen Feuer die Sicherungen nur mit Sicherungen ersetzen,
deren Typ und Nennwert auf den Tafeln neben den Sicherungsabdeckungen des
Geräts gedruckt sind.
Avvertenza:
per garantire protezione contro gli incendi, sostituire i fusibili con altri
dello stesso tipo aventi le caratteristiche indicate sui pannelli adiacenti alla copertura
fusibili dello strumento.
Advertencia:
Para evitar incendios, sustituir los fusibles por aquellos del tipo y
características impresos en los paneles adyacentes a las cubiertas de los fusibles del
instrumento.
警告:
為了避免火災,更換保險絲時,請使用與儀器保險絲蓋旁面板上所印刷之相同類
型與規格的保險絲。
警告:
为了避免火灾,应更换与仪器保险丝盖旁边面板上印刷的类型和规格相同的保险
丝。
경고:
화재의 위험을 막으려면 기기 퓨즈 커버에 가까운 패널에 인쇄된 것과 동일한 타
입 및 정격의 제품으로 퓨즈를 교체하십시오.
警告:
火災予防のために、ヒューズ交換では機器ヒューズカバー脇のパネルに記載されているタイプお
よび定格のヒューズをご使用ください。
Finding fuse types and ratings when that information does not appear on the
instrument or device:
Warning:
To protect against fire, replace fuses with those of the type and rating
indicated in the “Replacing fuses” section of the Maintenance Procedures chapter.
Avertissement :
pour éviter tout risque d'incendie, remplacez toujours les fusibles
par d'autres du type et de la puissance indiqués dans la rubrique "Remplacement des
fusibles" du chapitre traitant des procédures de maintenance.
Warnung:
Zum Schutz gegen Feuer die Sicherungen nur mit Sicherungen ersetzen,
deren Typ und Nennwert im Abschnitt "Sicherungen ersetzen" des Kapitels
"Wartungsverfahren" angegeben sind.
Avvertenza:
per garantire protezione contro gli incendi, sostituire i fusibili con altri
dello stesso tipo aventi le caratteristiche indicate nel paragrafo "Sostituzione dei fusibili"
del capitolo "Procedure di manutenzione".
Advertencia:
Para evitar incendios, sustituir los fusibles por aquellos del tipo y
características indicados en la sección "Sustituir fusibles".
December 5, 2017, 715004751 Rev. C
Page 73