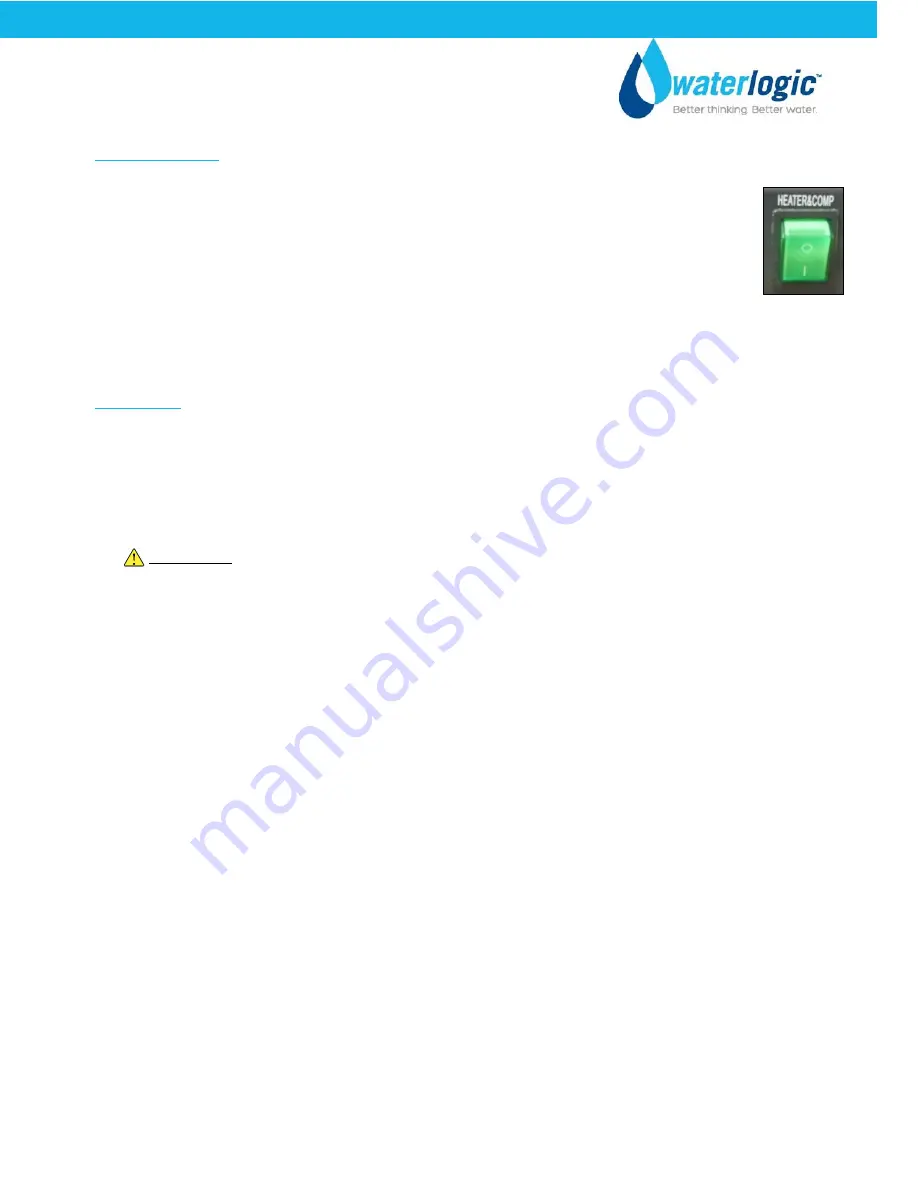
Compressor Test
34.
Switch Green Heater/Compressor to on
I=ON position
. Always ensure tanks are full
of water before turning on the heater or the overload (high limit) will open and
require manual reset. If the wire condenser at back of the unit is warm, the
refrigeration system is working.
35.
Once the machine reaches its target temperature, the compressor will shut off. Draw a glass of
cold water and verify it is has been chilled to proper temperature.
Heater Test
36.
Always ensure tanks are full of water before turning on the heater or the overload (high limit) will
open and require manual reset. It will take the heater approximately 10 minutes to heat the
water from ambient 75
°
F to the factory set point of 185
°
F. Dispense a cup of hot water to ensure
the temperature/odor/taste is acceptable.
WARNING!
VERY HOT WATER CAN BURN OR SCALD.
Hot water should be dispensed carefully into insulated container to avoid
WL400
Operating, Installation, and Service Manual Page 30 - Revision: 5-29-2015