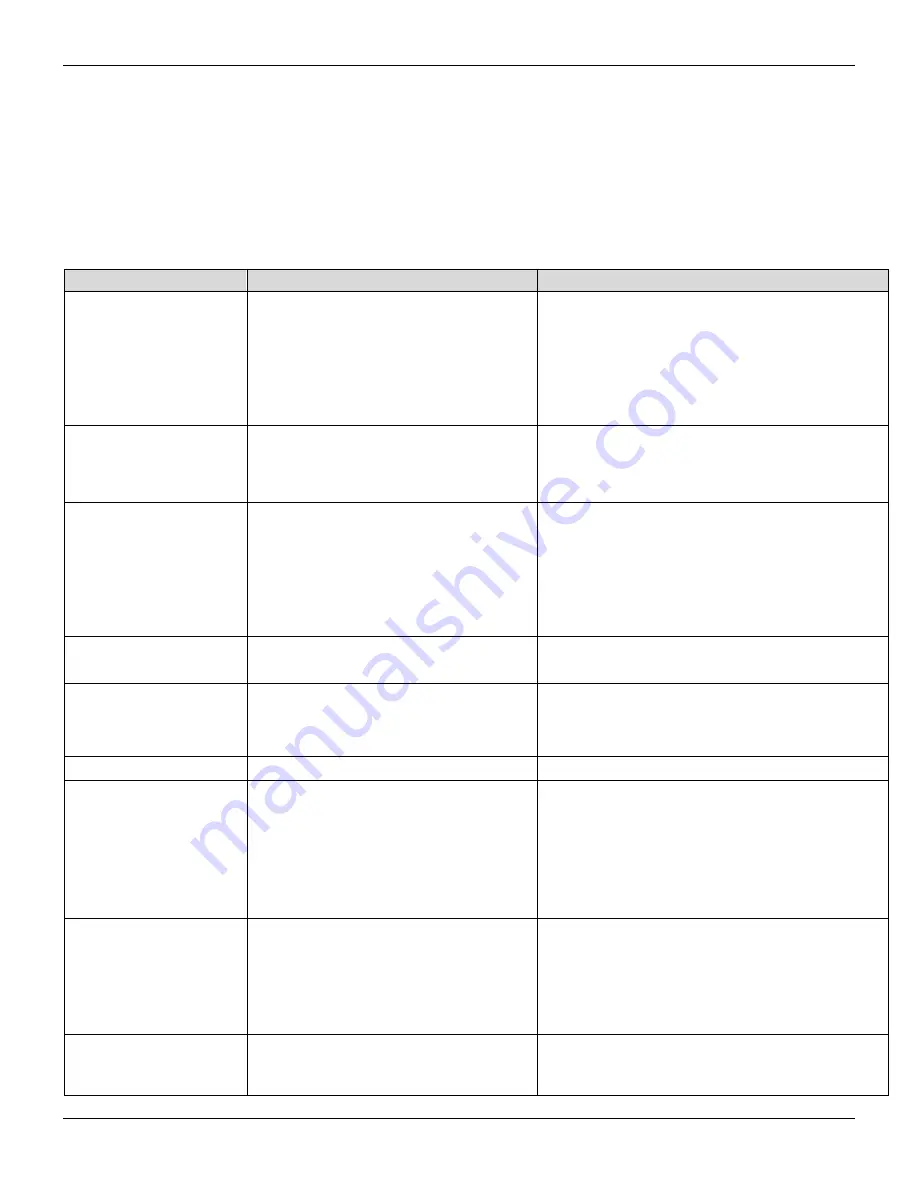
Page 14
TROUBLESHOOTING
SERVICE SHOULD BE PERFORMED BY QUALIFIED SERVICE PERSONNEL ONLY.
WARNING: Turn off the "Power-Fill” toggle switch. Unplug the power supply cord and allow the coffee appliance to cool before
servicing unless electrical testing is required.
WARNING: Make sure installation instructions have been followed before attempting to test this appliance.
Note: Allow the brewer appliance to heat up to brewing temperature BEFORE testing the temperature, water volume or the hi-limit
thermostat.
Symptom
Possible Causes
Remedies
1. The brewer appliance will
not turn ON when the
power switch is turned ON.
The power supply cord is not plugged in.
No power at the wall outlet.
The hi-limit thermostat has tripped.
The circuit breaker tripped.
Plug the power supply cord into an appropriate wall
receptacle.
Test the wall receptacle and the circuit breaker in the
building.
Call for service assistance.
Call for service assistance.
2. The brewer appliance trips
the building’s circuit
breaker.
Too many appliances are connected on one
electrical circuit.
The electrical circuits’ amperage rating is too low.
Remove any other appliances from the current circuit or call
an electrician to correct this problem.
Locate a correctly rated circuit, or call an electrician to correct
this problem.
3. The water for brewing is
not hot enough.
The brewing temperature has not been adjusted
correctly.
Adjust temperature program to higher setting.
WARNING: Hot coffee/water can cause serious burns. Make
sure that the coffee/water has stopped coming out of the
brew cone before you remove it from the appliance.
HANDLE HOT COFFEE/WATER CAREFULLY AND
PRACTICE CARE WHEN DRINKING
4. The coffee/water for
brewing is too hot.
The brewing temperature has not been adjusted
correctly.
Adjust temperature program to lower setting.
5. Incorrect or inconsistent
beverage level.
The water supply pressure may not meet
requirements.
Test the incoming water supply pressure. Water pressure
should be between 30 and 80 psi. If the water pressure
exceeds 80 psi, install a water pressure regulator and reduce
the water pressure to 50 psi.
6. The unit does not heat.
Call for service assistance.
7. The coffee appliance is
making unusual noises.
The water supply tube may be touching the
appliance, counter top or walls.
The water pressure may be excessive.
Adjust the tubing so it does not touch the appliance, counter
top or wall.
Test the incoming water supply pressure. Water pressure
should be between 30 and 80 psi. If the water pressure
exceeds 80 psi, install a water pressure regulator and reduce
the water pressure to 50 psi.
Call for service assistance.
8. Service Light comes on at
power on.
Defective Temp. Sensor. Defective Control Board
Temp. Sensor not connected to Control Board
Hot water temperature exceeds the “Set
Temperature”.
Water inlet was open for longer than 15 – 20
minutes.
Unplug the machine power cord from the wall outlet and re-
plug the machine power cord. Machine should operate
properly. If the machine still fails to operate properly, Call for
service assistance.
9. Water continuously flowing
from the spray head and
will not stop
Defective Inlet Valve.
Defective Control Board
Defective Power Supply Board
Call for service assistance.
Summary of Contents for AlwaysFresh H2O AP-UCBS-KIT
Page 19: ...Page 19 NOTES...