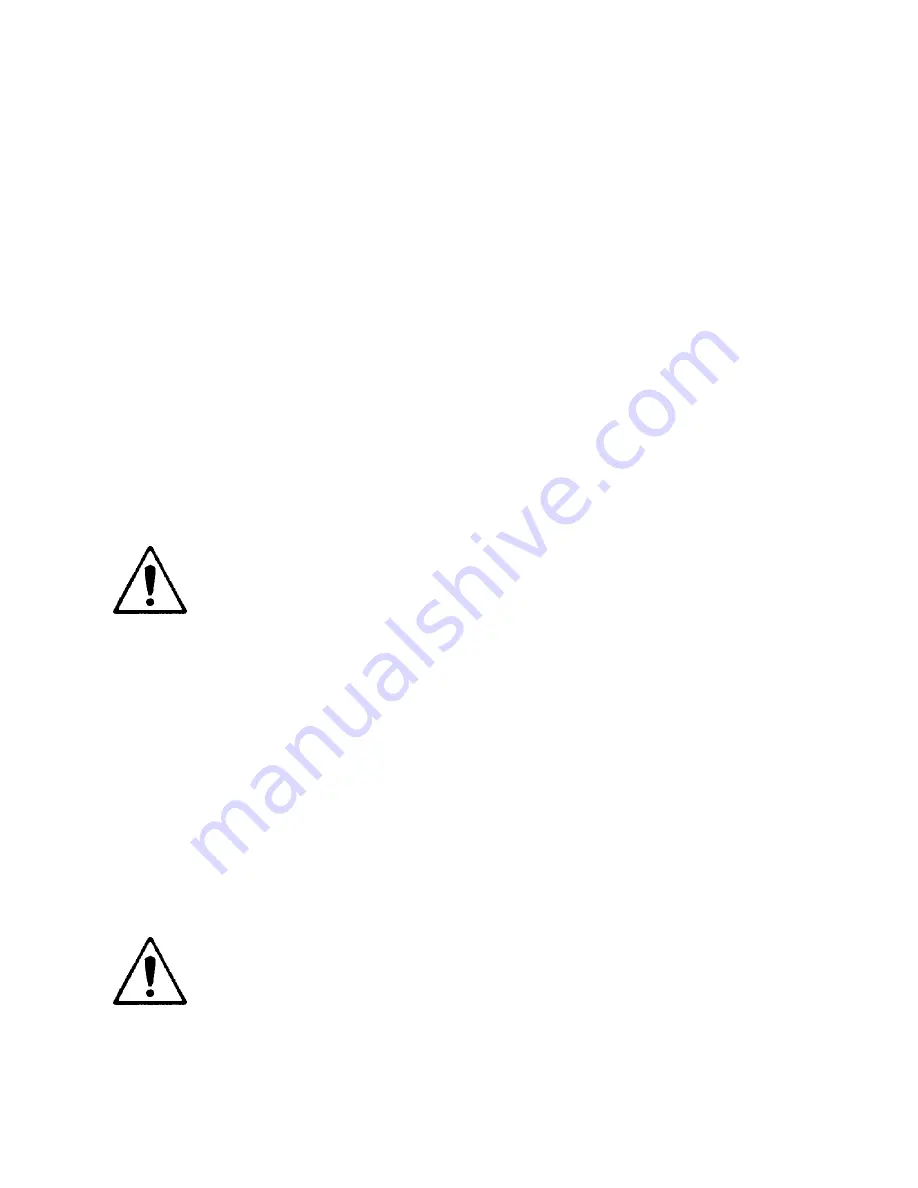
page 9
INLET/OUTLET PLUMBING: Connect to a supply line downstream of outdoor spigots. Install an inlet shutoff valve
and plumb to the unit’s bypass valve inlet located at the right rear as you face the unit. There are a variety of
installation fittings available. They are listed under Installation Fitting Assemblies. When assembling the installa-
tion fitting package (inlet and outlet), connect the fitting to the plumbing system first and then attach the nut, split
ring and o-ring. Heat from soldering or solvent cements may damage the nut, split ring or o-ring. Solder joints should
be cool and solvent cements should be set before installing the nut, split ring and o-ring. Avoid getting solder flux,
primer, and solvent cement on any part of the o-rings, split rings, bypass valve or control valve. If the building’s
electrical system is grounded to the plumbing, install a copper grounding strap from the inlet to the outlet pipe.
Plumbing must be done in accordance with all applicable local codes.
DRAIN LINE: First, be sure that the drain can handle the backwash rate of the system. Solder joints near the drain
must be done prior to connecting the drain line flow control fitting. Leave at least 6" between the drain line flow
control fitting and solder joints. Failure to do this could cause interior damage to the flow control. Install a
˚" I.D. flexible plastic tube to the Drain Line Assembly or discard the tubing nut and use the
∫
" NPT fitting for rigid
pipe. If the backwash rate is greater than 7 gpm, use a
∫
" drain line. Where the drain line is elevated but empties
into a drain below the level of the control valve, form a 7" (18 cm) loop at the discharge end of the line so that the
bottom of the loop is level with the drain connection on the control valve. This will provide an adequate anti-siphon
trap. Where the drain empties into an overhead sewer line, a sink-type trap must be used. Run drain tube to its
discharge point in accordance with plumbing code. Pay special attention to codes for air gaps and anti-siphon
devices.
IMPORTANT:
Never insert a drain line directly into a drain, sewer line, or trap. Always allow an air gap
between the drain line and the wastewater to prevent the possibility of sewage being
back-siphoned into the conditioner.
BRINE TANK CONNECTION: Install a
3
/
8
" O.D. polyethylene tube from the Refill Elbow to the Brine Valve in the brine
tank.
OVERFLOW LINE CONNECTION:
AN OVERFLOW DRAIN LINE IS RECOMMENDED WHERE A BRINE OVERFLOW COULD DAMAGE FURNISH-
INGS OR THE BUILDING STRUCTURE.
Your softener is equipped with a brine tank safety float which greatly reduces the chance of an accidental brine
overflow. In the event of a malfunction, however, an OVERFLOW LINE CONNECTION will direct the “overflow” to the
drain instead of spilling on the floor where it could cause considerable damage. This fitting should be on the side of
the cabinet or the brine tank.
To connect overflow fitting, locate hole in side of brine tank. Insert overflow fitting into tank and tighten with plastic
thumb nut and gasket from the inside. Attach a length of ˚" (1.3 cm) I.D. tubing (not supplied) to fitting and run to
drain. Do not elevate overflow line higher than 3" (7.6 cm) below bottom of overflow fitting. Do not “tie” this tube into
the drain line of the control valve. Overflow line must be a direct, separate line from overflow fitting to drain, sewer, or
tub. Allow an air gap as per the drain line instructions.
IMPORTANT:
Never insert a drain line directly into a drain, sewer line, or trap. Always allow an air gap
between the drain line and the wastewater to prevent the possibility of sewage being
back-siphoned into the conditioner.
INSTALLATION
Summary of Contents for FUSION2 F Series
Page 9: ......