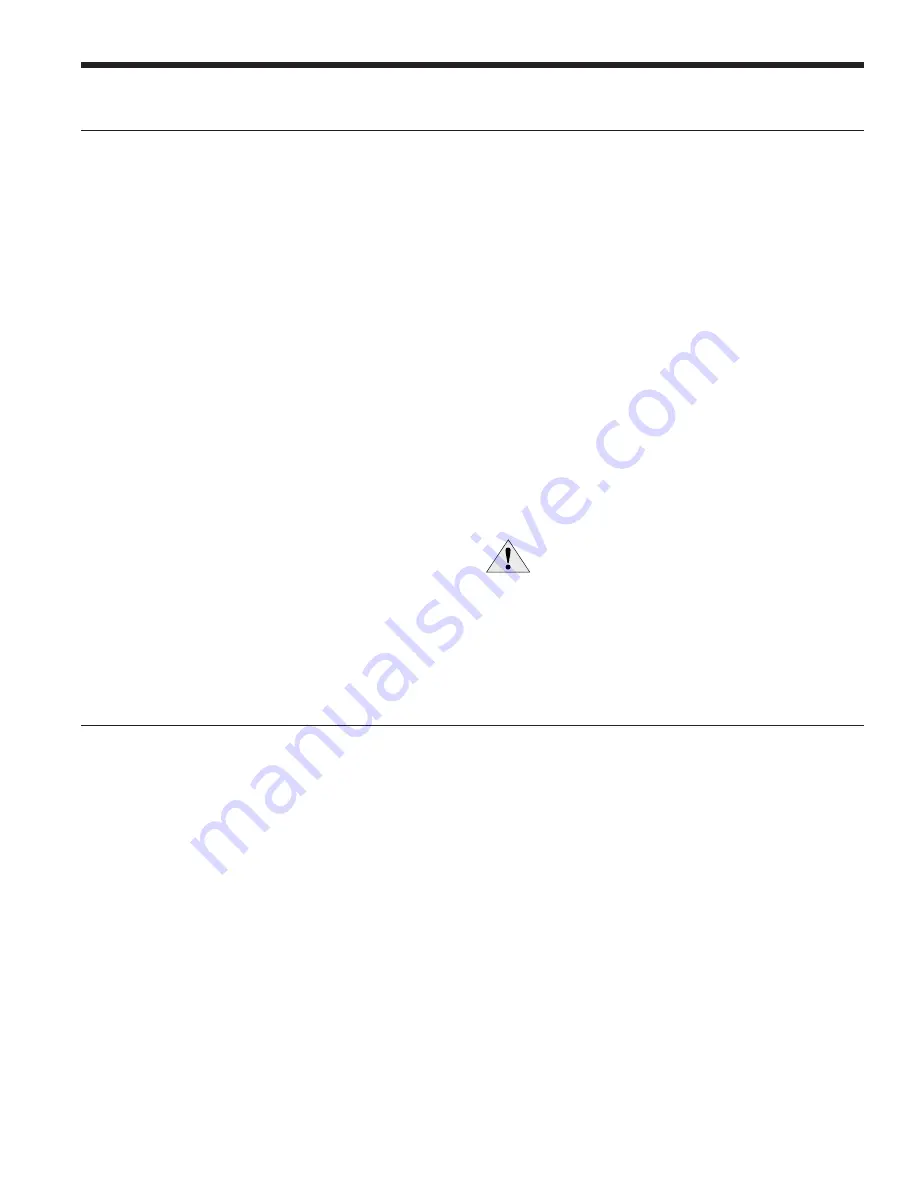
41
SYNERGY3D INSTALLATION MANUAL
Water Coil Maintenance
1. Keep all air out of the water. An open loop system
should be checked to ensure that the well head is not
allowing air to infiltrate the water line. Lines should
always be airtight.
2. Keep the system under pressure at all times. It is
recommended in open loop systems that the water
control valve be placed in the discharge line to prevent
loss of pressure during off cycles. Closed loop systems
must have positive static pressure.
NOTE:
On open loop systems, if the installation is in an area
with a known high mineral content (125 PPM or greater) in
the water, it is best to establish with the owner a periodic
maintenance schedule so the coil can be checked regularly.
Should periodic coil cleaning be necessary, use standard
coil cleaning procedures which are compatible with either
the cupronickel or copper water lines. Generally, the more
water flowing through the unit the less chance for scaling.
Other Maintenance
Filters
Filters must be clean to obtain maximum performance.
They should be inspected monthly under normal operating
conditions and be replaced when necessary. Units should
never be operated without a filter.
Obtaining Parts
When ordering service or replacement parts, refer to the
model number and serial number of the unit as stamped on
the serial plate attached to the unit. If replacement parts
are required, mention the date of installation of the unit
and the date of failure, along with an explanation of the
malfunctions and a description of the replacement parts
required.
In-Warranty Material Return
Material may not be returned except by permission
of authorized warranty personnel. Contact your local
distributor for warranty return authorization and assistance.
CAUTION:
Fin edges are sharp.
Preventative Maintenance
Condensate Drain
In areas where airborne bacteria produce a slime in the
drain pan, it may be necessary to treat chemically to
minimize the problem. The condensate drain can pick up
lint and dirt, especially with dirty filters. Inspect twice a
year to avoid the possibility of overflow.
Blower Motors
ECM blower motors are equipped with sealed ball bearings
and require no periodic oiling.
Hot Water Generator Coil
See Water Coil Maintenance section.
Air Coil
The air coil must be cleaned to obtain maximum
performance. Check once a year under normal operating
conditions and, if dirty, brush or vacuum (with a brush
attachment) clean. Care must be taken not to damage the
aluminum fins while cleaning.
Replacement Procedures
Summary of Contents for Synergy3D
Page 2: ......