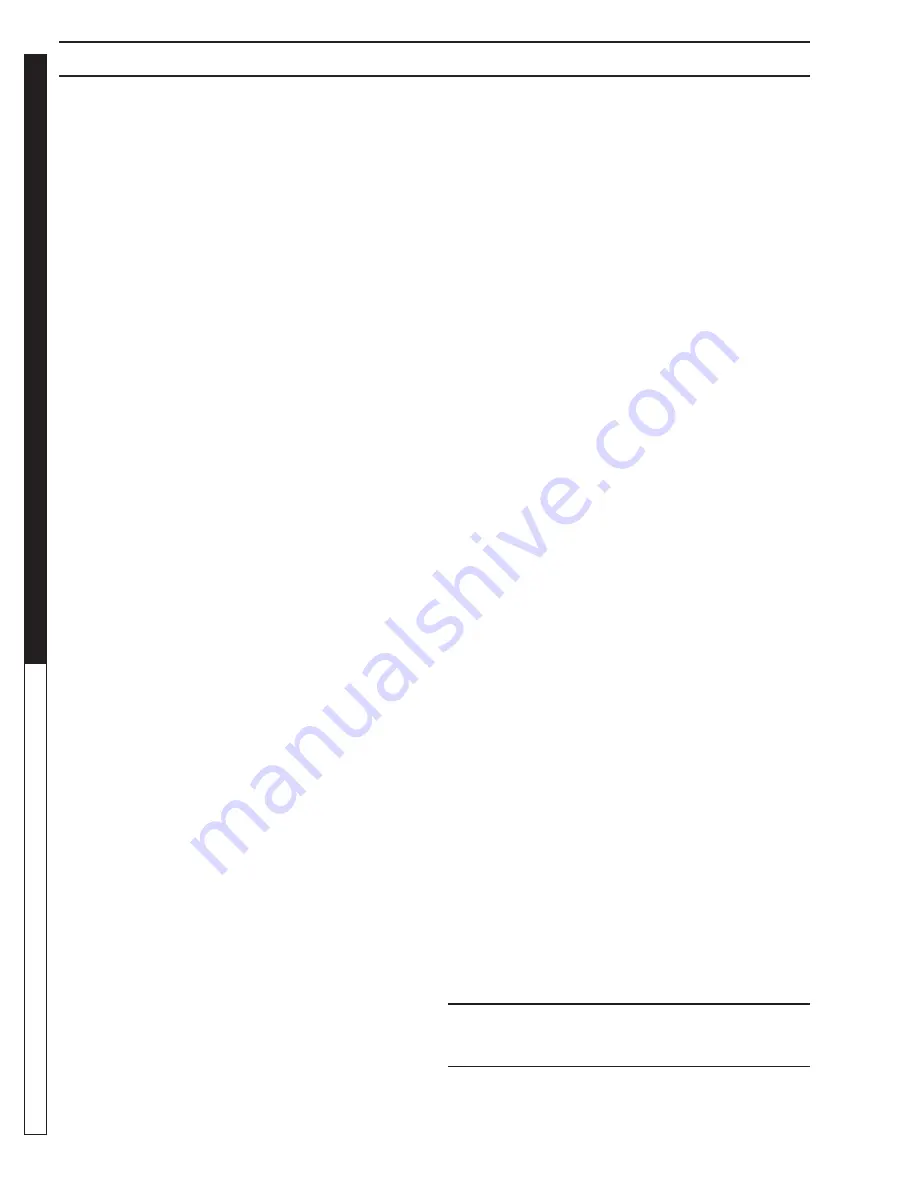
8.913-970.0 - L • WATERMAZE CLP 5024/7034
OPERA
T
OR’S MANU
AL
W
A
TER TREA
TMENT
SYSTEM
12
OPERATING INSTRUCTIONS
Water is gravity fed from the 600 gallon tank to Tank #1
and remains there until Tank #2 requires water. When
water is consumed from Tank #2 (by pressure washer,
recirculation or sewer discharge) the fi lter pump circu-
lates water from Tank #1 through the fi lters to Tank #2.
Flow rates through the fi lters can be adjusted up to 30
gallons per minute (GPM). For best results the fl ow rate
should be set to the lowest GPM that still allows the
entire system to operate correctly (the lower fl ow rate
increases wastewater/fi lter contact time and reduces the
fi lters solids loading).
Water remains in Tank #2 until it is either discharged
to the sewer (check your local regulations for limits in
your area), reused by the pressure washer or used for
recirculation of the pits and fi lters (see recirculation
mode). In the event an excess amount of water enters
the system (through rinse water or rain water) water is
automatically discharged from Tank #2 through the rain
water overfl ow solenoid valve to either the sewer or to
a holding tank. If the system's water level becomes too
low (i.e. evaporation, vehicle carry off), a fresh water
make-up solenoid valve feeds fresh water to Tank #2
until proper levels are maintained.
Filters
To ensure optimum filter performance and life, the
multi-media and carbon fi lters must periodically be
backwashed (see automatic backwash mode).
• The multi-media fi lter consists of a blend of sand,
garnet, gravel and anthracite. The media blend is
effi cient in screening out solids to 25-30 microns.
During the recirculation mode, the constant fl ow
through the media fi lter provides a fi nal
polish
to
the water.
• The carbon fi lter consists of degassed, virgin ac-
tivated carbon. Carbon removes, through absorp-
tion, pesticides, solvents, benzene, diesel fuels,
acetone and other hydrocarbons as well as low
levels of heavy metals.
Automatic Backwash Mode
Backwashing the media fi lters is required to rejuvenate
the fi lter media. Backwashing removes collected materi-
als and disperses the media to eliminate any channeling.
During normal operation of the CLP-5024/7034, the
multi-media fi lter, carbon fi lter or both may become
impacted with fi ltered solids, resulting in pressure head
loss through the fi lters and in poor overall performance.
The CLP-5024/7034 will backwash everyday if it needs
to or not. The multi-media will start backwashing at
midnight for 30 minutes. The CLP will then recover the
water level in Tank #1 and then backwash the carbon
fi lter. The operator cannot use the pressure washer at
that time, so it is important that the program imitates
your schedule. If it doesn't, call factory for assistance in
reprogramming your controller.
To backwash, the affected fi lter is isolated and the fl ow is
reversed via air actuated three way valves. A slip stream
solenoid is activated to allow proper water fl ow (30 GPM
for multi-media valve 20, 15-20 GPM for carbon valve
21) and water is pumped from Tank #1 through the fi lter
by the fi lter pump. This process continues for 30 minutes
and the resulting backwash outfl ow is returned to the
wash pad catch basin.
Once backwashing of the fi rst fi lter is completed the
second fi lter will then be backwashed. At no time will
both fi lters be backwashed at the same time.
Recirculation Mode
The purpose for recirculating the water through the pit
system and the fi lters is to minimize odor, kill bacteria
and provide high quality polished water.
Once each day the CLP will enter a recirculation mode.
This mode consists of two separate stages.
Stage 1:
The transfer pump sends water from Tank #2
through the return line to the wash pad catch
basin. To prevent odor and kill bacteria, the
return water is ozonated via a mazzi injector.
Stage 2:
Water is recirculated through the fi lter pack.
The transfer pump circulates water from
Tank #2 through a mazzi injector to Tank #1.
From Tank #1 the fi lter pump circulates water
through the fi lters to Tank #2.
Automatic Sludge Dump
During normal operation, the settling properties of the
solids will result in sludge build-up inside the cone bottom
tank cone. This sludge must be periodically removed.
This is accomplished once each day by an automated
sludge dump system.
To dump sludge, an air activated dump valve opens while
simultaneously a water solenoid activates (to stir-up any
impacted material in the bottom of the cone bottom tank)
to allow sludge to fl ow to the sludge collection bag. To
reduce excess water in the sludge bag, the water sole-
noid is only activated for a few seconds. Once the dump
valve closes, the sludge bag is allowed to de-water and
excess water is returned, via gravity feed, to the wash
pad catch basin.
If at any time, the user needs an additional sludge dump, a
manual switch enables the automatic sludge dump cycle.
AUTOMATIC MAINTENANCE
CONTROLLER; 5024, 7034