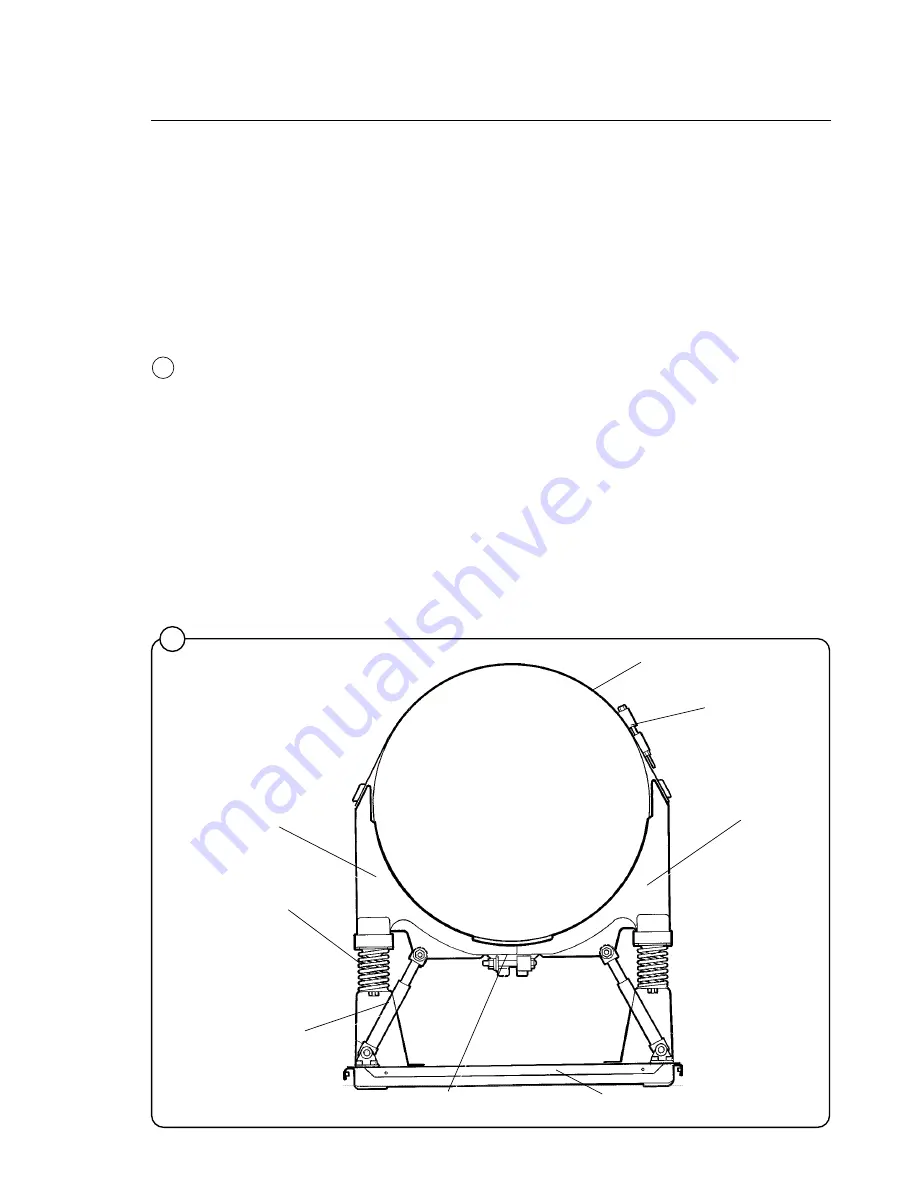
31
Mechanical and electrical design
Machine construction
Panels
The machines are equipped with a top panel made of stainless
steel. The front panel is available in different colors or in stainless
steel. The colored panels are made of phosphatized steel plate.
For servicing purposes, the panels can easily be removed.
Frame
The frame consist of a bottom plate and two balance weights. The
balance weights form a cradle for the outer drum and are
suported by four springs. There are four shock absorbers to
control the movements of the drum.
Inner cylinder
The inner cylinder is made of perforated surgical stainless steel. It
is equipped with three lifting ribs and has highly-polished side
sheets and back with maximum embossed perforated area to
assure high flow of water and supplies through fabrics.
Scientifically correct ratio of cylinder diameter and depth assures
maximum washing action.
The shaft is electrically welded to the reinforced back of the cylin-
der. A specially designed chrome-plated sleeve bushing protects
the seals from wear.
0922
Balance weight,
left-hand, front
Balance weight,
right-hand, front
Bottom plate
Clamping bolt
Spring
Shock-absorber
Tie strap
48
Clamping screw
Fig.
48