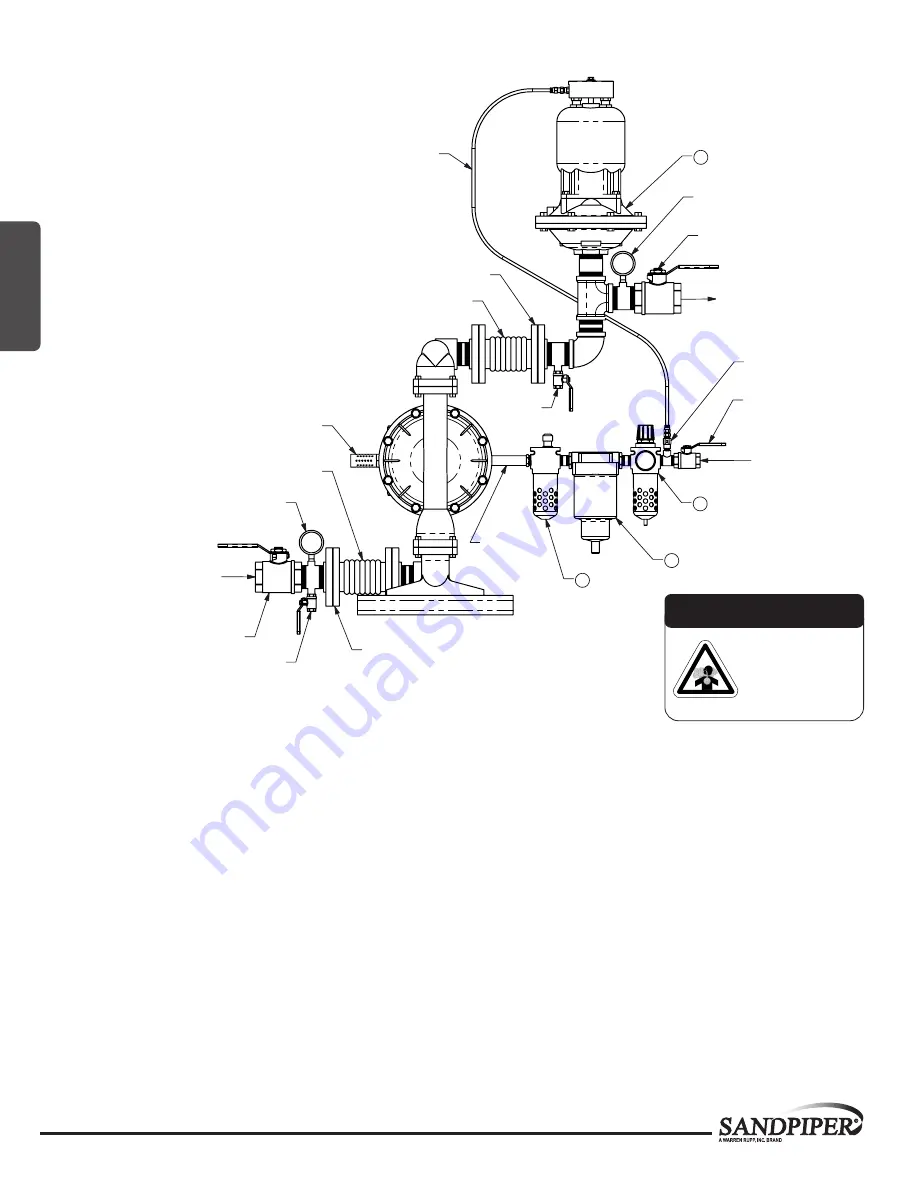
hp20mdl1sm-rev0621
10
• Model HP20 High Pressure
sandpiperpump
.
com
Installation And Start-Up
Locate the pump as close to the product being pumped as possible. Keep the suction line length and number of fittings to a minimum. Do not reduce the suction line
diameter.
Air Supply
Connect the pump air inlet to an air supply with sufficient capacity and pressure to achieve desired performance. A pressure regulating valve should be installed to
insure air supply pressure does not exceed recommended limits.
Air Valve Lubrication
The air distribution system is designed to operate WITHOUT lubrication. This is the standard mode of operation. If lubrication is desired, install an air line lubricator
set to deliver one drop of SAE 10 non-detergent oil for every 20 SCFM (9.4 liters/sec.) of air the pump consumes. Consult the Performance Curve to determine air
consumption.
Air Line Moisture
Water in the compressed air supply may cause icing or freezing of the exhaust air, causing the pump to cycle erratically or stop operating. Water in the air supply can
be reduced by using a point-of-use air dryer.
Air Inlet And Priming
To start the pump, slightly open the air shut-off valve. After the pump primes, the air valve can be opened to increase air flow as desired. If opening the valve
increases cycling rate, but does not increase the rate of flow, cavitation has occurred. The valve should be closed slightly to obtain the most efficient air flow to pump
flow ratio.
1 Surge Suppressor
Flexible Connector
Pipe Connection
(Style Optional)
Shut-Off Valve
Pressure Gauge
Drain Port
Muffler
(Optional Piped Exhaust)
Flexible
Connection
3 Dryer
2 Filter Regulator
Unregulated Air
Supply to Surge
Suppressor
Shut Off
Valve
Flexible Connector
Pipe Connection
(Style Optional)
Drain Port
Shut-Off Valve
Compound
Gauge
Note
: Surge Suppressor and
Piping, including air line,
must be supported after
the flexible connections.
Check
Valve
Air Inlet
Suction
Discharge
4 Lubricator
Recommended Installation Guide
Available Accessories:
1.
Surge Suppressor
2.
Filter/Regulator
3.
Air Dryer
4.
Lubricator
CAUTION
The air exhaust should
be piped to an area
for safe disposition
of the product being
pumped, in the event of
a diaphragm failure.
2: INST
AL
& OP