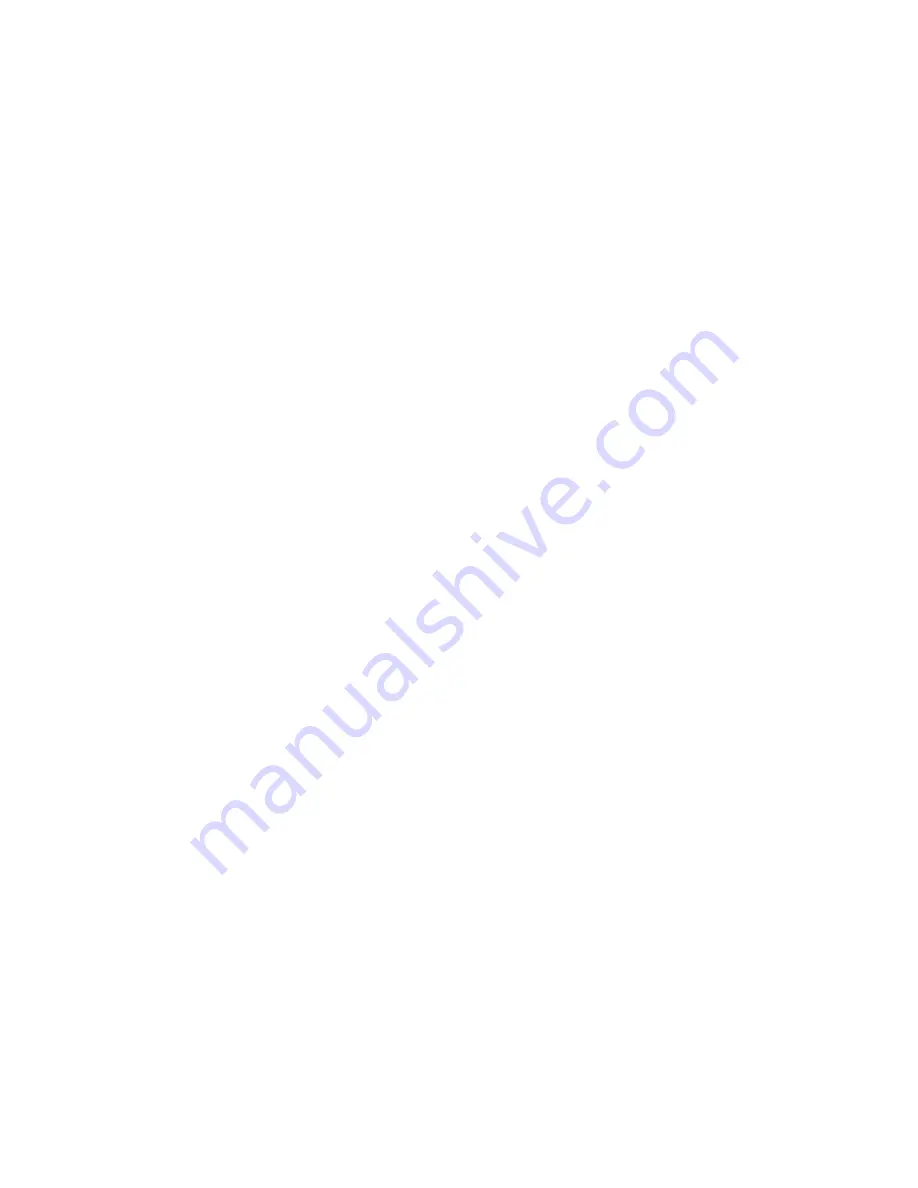
www.Warming-Trends.com | 303 346 2224 | [email protected]
23
JET ORIFICE CLEANING
Annual inspection and cleaning of the fire feature is rec-
ommended. If at any time the flames exhibit any abnormal
shapes or behavior, or if burner fails to ignite properly,
then the burner holes located in bottom of gas jet orifices
may require cleaning. The appliance can be cleaned by
carefully removing the logs and media to allow access to
burner. Use a brush to carefully remove dust, spider webs
and loose particles. Periodical inspection by a qualified
service technician of the air-intake is required to ensure
your fire feature performs properly.
Use a wire or small puncture tool and carefully insert in
jet. Tool should be size of a small paper clip. If evidence
of damage, burner must be replaced with the appropriate
CROSSFIRE
®
burner specified by manufacturer.
PILOT ASSEMBLY/THERMOCOUPLE CLEANING OF SOOT
Every six months or as needed, remove media, lava rock,
or glass from around the pilot assembly. Clean the ther-
mocouple of any soot using soft brush. Be careful not to
damage the igniter element. Be sure when returning your
media to the pit to cover your orifices to avoid blocking
the jets as mentioned on page 6.
Once pilot assembly is clean, inspect to see flame that
covers 3/8" to 1/2" of the thermocouple. Cleaning of pilot
gas orifice may be required by removing pilot hood and
removing orifice and cleaning out orifices from debris,
soot or anything that may be preventing gas flow from
exiting the pilot gas orifice.
For Push Button only, visually inspect electrode and jet
used for conductivity regularly to make sure it is free of
debris and soot. Soot build up or obstructions of any kind
can reduce effectiveness of spark. Without a strong spark,
burner will not light. If spark is not strong enough, clean
off/remove any soot from jet and, using fine grit sand
paper, gently remove any rust from electrode. If spark
is still not strong enough to light burner, check/replace
batteries. If new batteries don’t fix the problem, replace
the spark electrode.
TROUBLESHOOTING
MATCH LIT / PUSH BUTTON
Below are some potential causes and countermeasures to
the symptoms listed:
• No flame — Make sure the key valve is on. Turn key to
the left to open valve and allow gas flow.
• Low or Weak Flame — Verify correct gas pressure
using the Water Column Pressure Chart.
• One or more jets will not light — Clean the orifices and
check jets for obstruction.
• Fire feature is making a whistling sound — Make sure
that the flex line is the whistle-free, without sharp
bends, and installed correctly. Check the pressure to
be sure it is within recommended ranges.
• Contact a certified gas technician for service and re-
pair if these suggestions do not solve the issue.
ELECTRONIC IGNITION SYSTEMS
Below are some potential causes and countermeasures to
the symptoms below.
• No Pilot Flame — Pilot sparks or glow plug glows but
pilot won’t light.
o Air in the gas line. If this is a new install it may take
several attempts to purge the air.
o Debris is in the gas line. Clear the gas line.
o Water/Moisture is in the gas line. Clear the gas line.
o Incorrect Gas pressure. Confirm proper gas pres-
sure.
o Pilot gas orifice is dirty. Remove the pilot head and
clean.
o Electrical current is not strong enough to support
igniter — either spark on spark igniter isn’t strong
enough to ignite pilot flame (3V or Spark Igniter) or
glow plug is not getting hot enough to ignite pilot
flame (Hot Surface Igniter).
o Improperly applied media.
o Wind conditions might be too severe.
• No Main Burner — Pilot lights but main burner will not
light.
o Gas pressure is incorrect. Confirm proper gas
pressure.
o Small pilot flame. Remove the pilot head and clean
pilot gas orifice.
o Dirty thermal sensor. Clean using soft brush.
o CROSSFIRE™ Burner has an obstruction. Confirm
there is no debris blocking gas orifice jets in main
burner, purge water and air from gas lines or in the
burner, and confirm there is no debris in gas lines.
• Main Burner Turning On and Off Intermittently
o Small pilot flame. Remove the pilot head and clean
as described in the maintenance section.
o Improperly applied media — Make sure your media
is not covering the pilot assembly and that your
logs are not placed over or too near the wind cage.
o Gas pressure is incorrect — Confirm proper gas
pressure by checking at the gas stub to the pit and
the Water Column Pressure Table.
o Thermal sensor is dirty or defective — Gently clean
thermal sensor, or change the pilot assembly.
o Wind conditions — Confirm the burner is properly
located 4-6” inside the pit, and be sure the wind
conditions are not too severe for safe use.
o Fire Feature is Making a Whistling Sound — Make
sure that the flex line is the correct size and that
there are no kinks or tight bends in the line. If the
whistling sound is coming from the jets, please
check your pressure against the Water Column
Pressure Table in this manual to make sure it is
within recommended ranges. Adjust as needed.
Please contact your retailer or certified technician for
service and repair if these suggestions do not solve the
issue. If replacement parts are required — contact your
retailer or licensed technician for authorized replacement
parts. Warranty is null and void if unauthorized parts are
used.