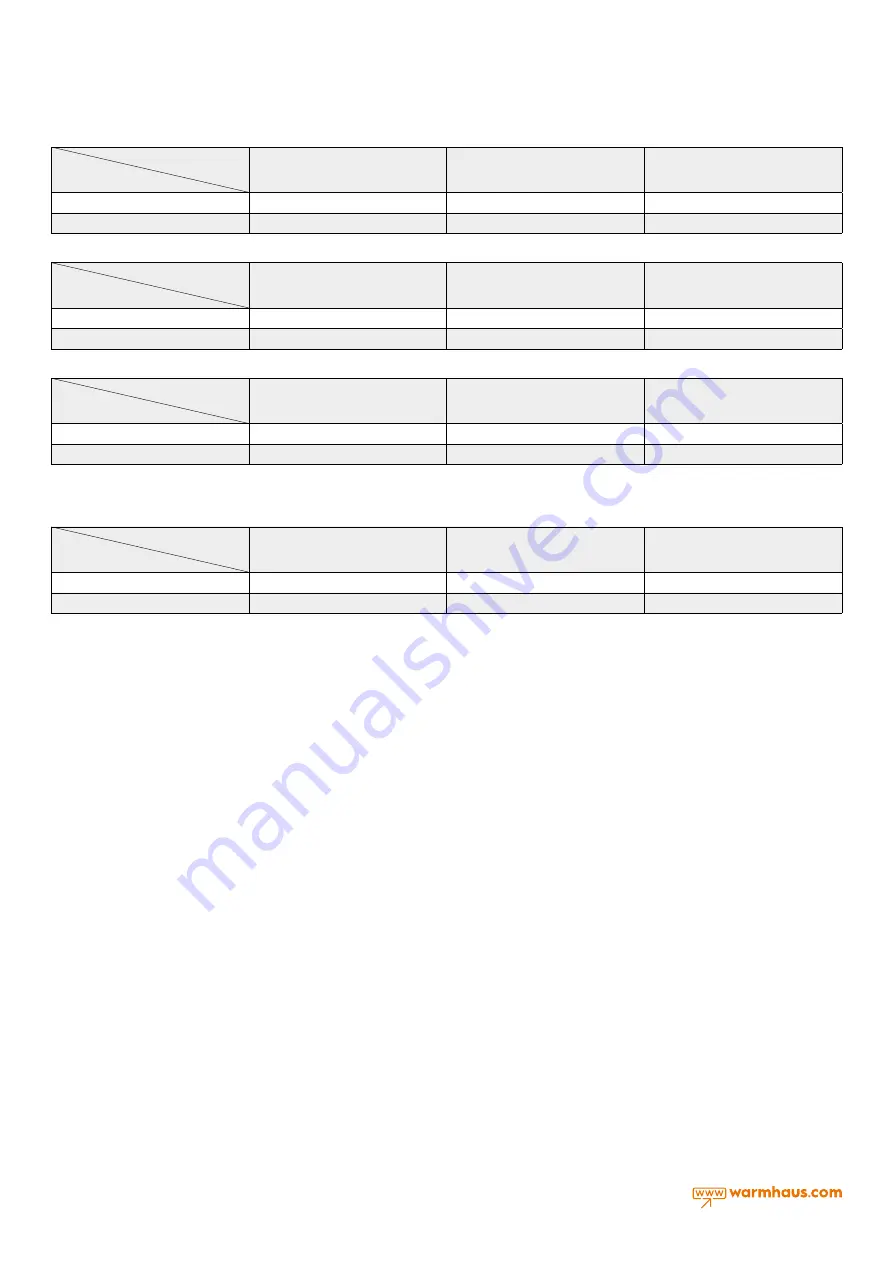
10
Room Sealed Appliances Installed within an Enclosure (Natural ventilation requirements direct to Outside Air)
System Type
Grille Location
600m from any obstruction
Heating &/or HWS
Operation < 50% during summer months
Heating &/or HWS
Operation > 50% < 75% during summer
months
Heating &/or HWS
Operation > 75% during summer months
High Level (Free Area/kW)
5 cm
2
6 cm
2
7 cm
2
Low Level (Free Area/kW)
5 cm
2
6 cm
2
7 cm
2
Room Sealed Appliances Installed within an Enclosure (Natural ventilation requirements Via an internal Space)
System Type
Grille Location
600m from any obstruction
Heating &/or HWS
Operation < 50% during summer months
Heating &/or HWS
Operation > 50% < 75% during summer
months
Heating &/or HWS
Operation > 75% during summer months
High Level (Free Area/kW)
10 cm
2
11 cm
2
12 cm
2
Low Level (Free Area/kW)
10 cm
2
11 cm
2
12 cm
2
Room Sealed Appliances Installed within a Boiler Room / Heated Space (Natural ventilation requirements direct to Outside Air.)
System Type
Grille Location
600m from any obstruction
Heating &/or HWS
Operation < 50% during summer months
Heating &/or HWS
Operation > 50% < 75% during summer
months
Heating &/or HWS
Operation > 75% during summer months
High Level (Free Area/kW)
2 cm
2
3 cm
2
4 cm
2
Low Level (Free Area/kW)
2 cm
2
3 cm
2
4 cm
2
Max Operating Pressure < 100mbar, Room Air Change Rate >0.5/hour = No Additional Ventilation. If the air change rate is less than 0.5/hour them
the following must be applied.
Appliances without draught diverters with or without draught stabilisers
System Type
Grille Location
600m from any obstruction
Heating &/or HWS
Operation < 50% during summer months
Heating &/or HWS
Operation > 50% < 75% during summer
months
Heating &/or HWS
Operation > 75% during summer months
High Level (Free Area/kW)
1.35 +/- 0.18 (m
3
/h/kW)
1.35 +/- 0.18 (m
3
/h/kW)
1.35 +/- 0.18 (m
3
/h/kW)
Low Level (Free Area/kW)
2.6 (m
3
/h/kW)
3.32 (m
3
/h/kW)
4.04 (m
3
/h/kW)
VENTILATION
“Viwa 90 - 150” boilers an be installed in boiler rooms whose size and
requirements meet current regulations. The following is provide for your
guidance only, and assumes the ventilation air is taken directly from
outside. The sizes of the vents may need to be increased inrespect
of other appliances installed in the same area, and seasonal use. Take
care that the position of low level vents would not subject to adverse
weather conditions, ie flooding.
Ventilation requirements for Viwa 90 -150 boilers and cascade systems.
BS6644 has a requirement that the temperatures in a room or
compartment do not exceed certain levels:
- +25 °C at floor level (0-100 mm)
- +32 °C at mid level (1.5 m above the floor level)
- +40 °C at ceiling level (0-100mm from ceiling)
When installed as a class B appliance (open flued, not roomed sealed).
Installed in a room High level (within 15% of the room height from
ceiling) - 2 cm²/kW of net heat input Low level (low as possible within
1 metre from floor natural gas ) – 4 cm²/kW of net heat input A single
Viwa 125 (116 kW net input) boiler would require 232 cm² at high level
and 464 cm² at low level. Installed in a compartment or enclosure
High level (within 15% of the room height from ceiling) - 5 cm²/kW of
net heat input Low level (low as possible within 1 metre from floor
natural gas) –10 cm²/kW of net heat input. A single Viwa 125 (116 kW net
input) boiler would require 580 cm² at high level and 1160 cm² at low
level. When installed as a class C appliance (room sealed). Installed in
a room High level (within 15% of the room height from ceiling) - 2 cm²/
kW of net heat input Low level (low as possible within 1 metre from
floor natural gas) – 2 cm²/kW of net heat input A single Viwa 125 (116
kW net input) boiler would require 232 cm² at high level and 232 cm²
at low level.
2.4. NATURAL GAS CONNECTION (DEVICE
CATEGORY I
2H
)
Our boilers were manufactured to run with methane gas (G20).
Gas supply pipes must be equal to or greater than 3/4 "G boiler
connections. Before connecting the gas, a careful internal cleaning of
the pipe laying of the entire fuel supply installation must be carried
out, since possible waste will damage the best performance and
efficiency of the boiler. It must be checked that the gas distributed
from the main line is in the type stipulated for the boiler (see the label
on the boiler).
In addition, the network dynamic pressure (methane) to be used
in feeding the boiler and in case of it is inadequate, that may
affect the power of the boiler and cause difficulties for the user.
Make sure the gas valve connection is made correctly. The
flammable gas supply pipe must be designed and dimensioned
according to the current MMO and local gas company
specifications and instructions in order to ensure that the boiler is
capable of delivering sufficient gas to the burner while the boiler
is operating at maximum power and the device is efficient. The
connection system must comply with legal regulations.
2.4.1. Flammable Gas Quality
The boiler is designed to be used with pure fuel which does not
contain foreign substance in; for this reason it is absolutely necessary
to add the necessary filter systems in the gas supply line (in order to
ensure that the fuel is purified).