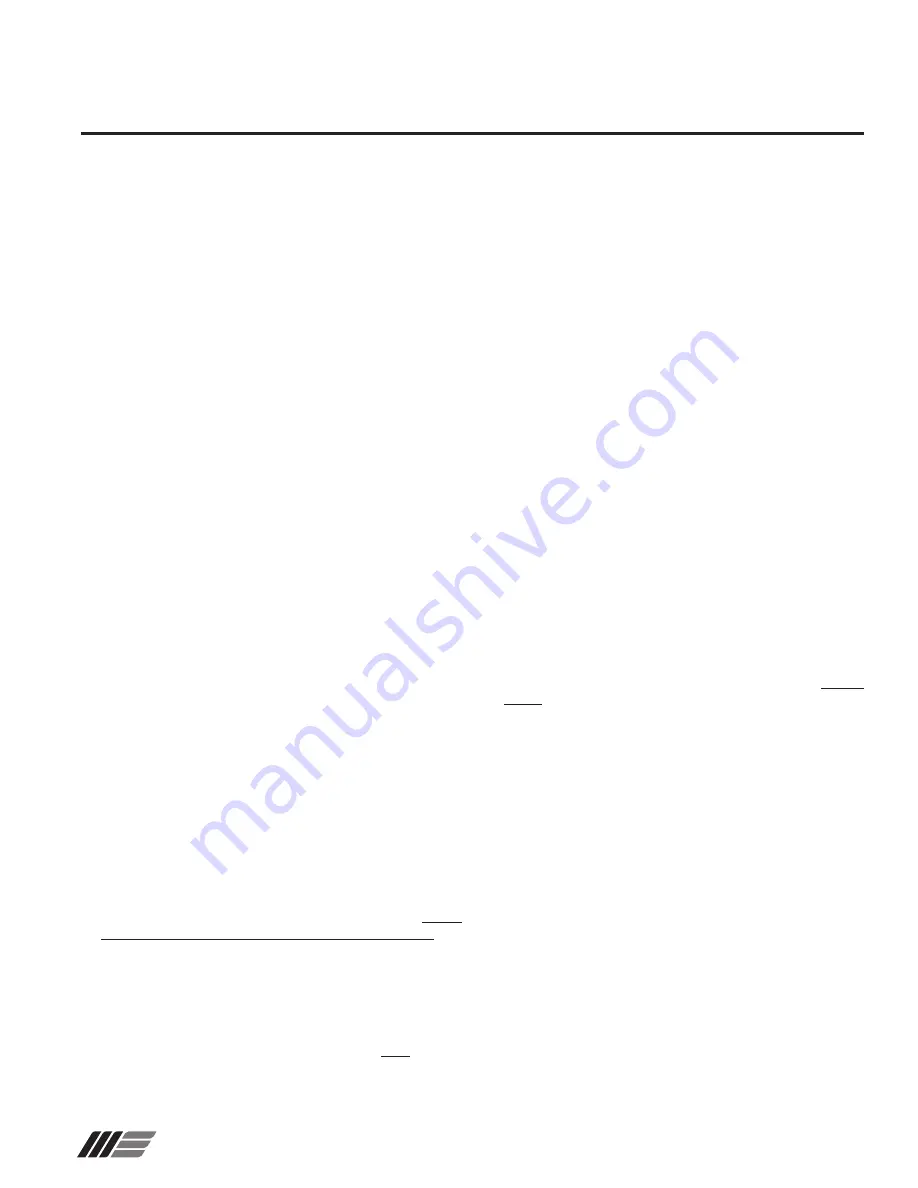
7
Wanner Engineering, Inc.
United States
Instant Information: www.wannereng.com
(61) 33-5681 Fax (61) 33-6937
SCK-991-400B
Inspection
Impeller.
Replace if the impeller shows excessive erosion
(especially on the pump-out vanes on the back side of the
impeller), corrosion, extreme wear, or vane breakage. The O-
ring groove and impeller hub must be in good condition. Check
the impeller balance.
Shaft.
Check for runout to see that the shaft has not been bent.
If runout exceeds 0.002 in., replace the shaft. Bearing seats
and the oil seal area must be smooth and free of scratches or
grooves. The shaft threads must be in good condition. Replace
the shaft if necessary.
Shaft Sleeve.
The sleeve surface in the stuffing box must be
smooth and free of grooves. If grooved, replace it.
Mechanical Seal.
The seal faces, gaskets, and shaft sealing
components must be in perfect condition or excessive leakage
may result. Replace worn or damaged parts.
Ball Bearings.
Replace bearings if worn, loose, or rough and
noisy when rotated. Do not unwrap new bearings until ready for
use. Replacement bearings must be of the proper size and type
as supplied with the original equipment.
Oil Seals.
Replace if torn or otherwise damaged.
Note:
The oil seals are held by a press fit. The lips on the seals
must face inward (toward the bearings).
General.
All parts should be clean before reassembly. This is
especially important at the retaining ring and O-ring grooves,
threads, gasket surfaces, and bearing and bearing housing
lubricated areas. Remove any burrs with crocus cloth.
Reassembly
1. Lubricate the shaft liberally with grease in the area where the
outboard bearings (12) seat.
The outboard bearings are
angular-contact duplex-mounted and must be installed
facing the proper direction.
Start the first bearing so that it
is square with the shaft and the stamped face is away from
the shaft shoulder. Press the bearing onto the shaft until it
seats against the shoulder.
Press only on the inner race.
Lightly lubricate the shaft again with grease and start the
second bearing so that the stamped faces of the bearings
are together. Press the second bearing onto the shaft until
it seats against the first bearing. Install the lock washer (13)
and lock nut (14). Tighten the lock nut firmly until one washer
tab aligns with a slot in the nut. Bend the lock washer tab into
the slot.
2. Place the tapered snap ring (17) loosely over the shaft so that
the tapered side faces away from the outboard bearing.
3. Lubricate the shaft lightly with wheel grease in the area where
the inboard bearing (11) mounts. Start the bearing squarely
on the shaft. Press the bearing onto the shaft until it seats
against the shoulder.
Press only on the inner race.
4. Lubricate the sealing element of the outboard oil seal (21)
(grease on outside of seal and inside of housing). Press the
oil seal into the bearing housing (15) until it is flush with the
outboard surface.
Service
5. Lubricate the area of the shaft which enters the outboard
oil seal. Start the shaft and outboard bearings squarely into
the bearing housing. Be careful that the shaft enters the oil
seal properly. The outer races may be mounted with a hand
push or light tapping.
Apply force only to the outer race.
The bearings should bottom out in the bearing housing, just
exposing a tapered groove in the I.D. of the housing.
Note:
The beveled face of the snap ring must face out of the
bearing housing.
Using a Truarc pliers No. S-6700 (No. S-6500 for AA or AB
pumps), install the snap ring in this groove.
6. Grease the sealing element of the inboard oil seal (20). Press
the oil seal into the frame (18) until it is flush with the outside
surface.
7. Install the O -ring (16) into the groove in the O.
D. of the bearing housing. Lubricate the O.D. of the housing
and the I.D. of the frame with grease.
8. Guide the impeller end of the shaft into the frame and through
the inboard seal until the bearing housing flange stops against
the frame.
Inspect the seal for proper fit. Use a small dull tool to push
the seal into place if needed.
Build from the back and go forward.
9.
Loosely install the three bolts (36) and nuts (40-D) which
secure the housing to the frame, and tighten them hand-
tight. Install three jam bolts (37) and jam nuts (40-D) in
the threaded holes of the frame flange.
10.
On pump sizes other than AA or AB, secure the frame
support (19) to the frame using two cap screws (38).
11. Drive the sleeve drive pin (9) into its hole in the shaft until it
bottoms out with a punch.
12.Carefully press the deflector (26) over the shaft. Do not
break.
13. Install the sight oil gauge (22), oiler assembly (23), drain plug
(24), and breather (25) in the appropriate tapped holes in the
frame.
14. Place the casing (1), front plate (31), and casing support (32)
in position, if they were removed.
15. Use socket-head cap screws (42 and 43) to reinstall the
suction and discharge flanges (33 and 34), if they were
removed.
Note:
The torque values given below are a guide for initial
assembly of new components at room temperature. Extended
service life and/or operating temperature extremes may
require different values, based on your judgment.
16. With the back cover (2) and mounting plate (28) assembled,
place the back cover on a flat surface with the mounting plate
studs facing up.
17. Place the adaptor (27) over the studs in the mounting plate
(28). Secure with four hex nuts (40-B).
Torque to 3-5 ft-lbs
(2-4 ft-lbs on AA or AB pumps).
Note:
If a double seal is used, ignore steps 18-20 and go on
to step 21.