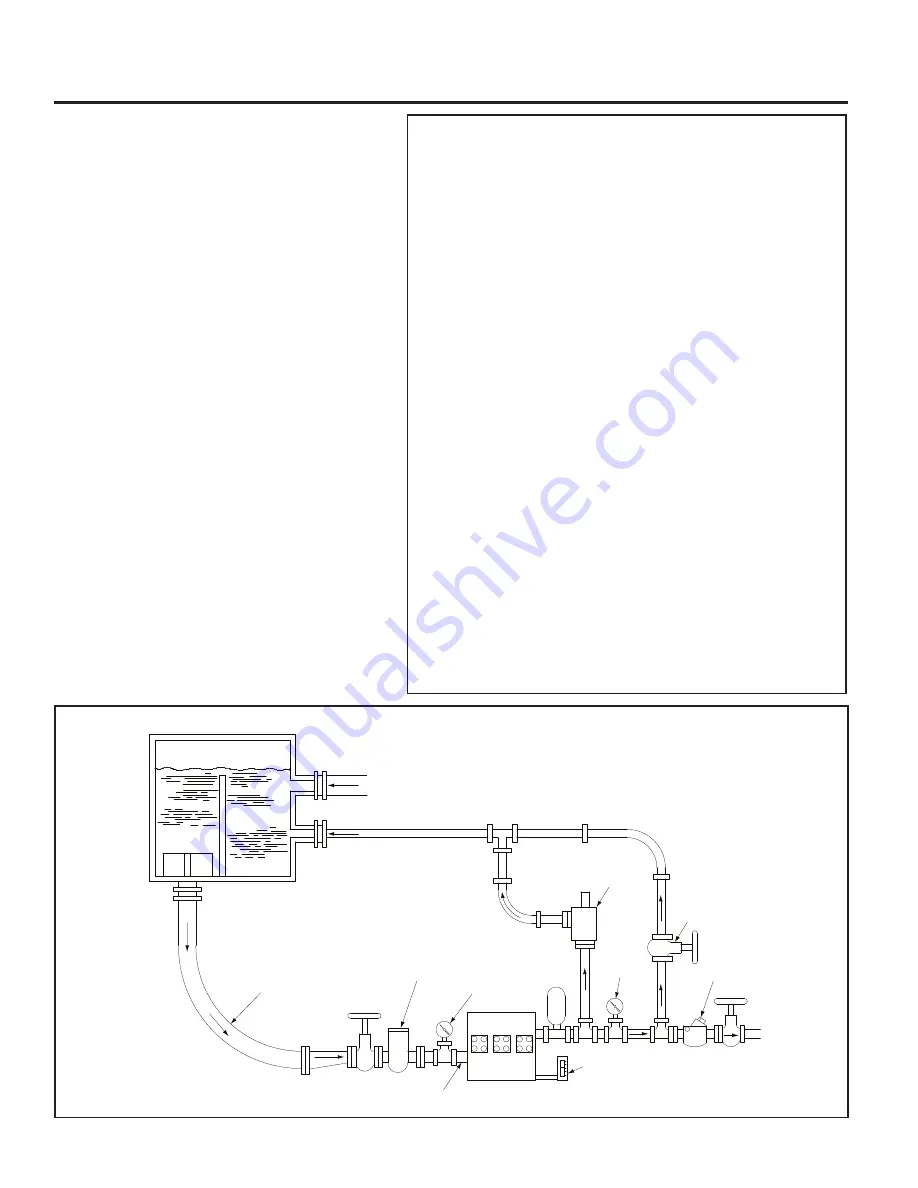
8
177-999H
T100 Series Medium Pressure - Installation
Important Precautions
Adequate Fluid Supply.
To avoid cavitation and premature pump
failure, be sure that the pump will have an adequate fluid supply and
that the inlet line will not be obstructed. See “Inlet Piping” and consult
NPSH chart.
Positive Displacement.
This is a positive-displacement pump. Install
a relief valve downstream from the pump. See “Discharge Piping”.
Safety Guards.
Install adequate safety guards over all pulleys,
belts, and couplings. Follow all local codes and regulations regarding
installation and operation of the pumping system.
Shut-Off Valves.
Never install shut-off valves between the pump and
discharge pressure regulator, relief valve, or in the regulator bypass line.
Freezing Conditions.
Protect the pump from freezing. See also the
Maintenance Section.
Vacuum at Outlet.
Do not allow a vacuum at the pump outlet during
shutdown. A vacuum can damage the diaphragm at start-up. If there is a
vacuum at the pump outlet, allow atmospheric pressure at the outlet for
30 minutes before starting. Wanner Engineering recommends installing
an outlet check valve with a 65 psi (4.5 bar) cracking pressure to prevent
a vacuum condition during shutdown.
Consult the Factory for the following situations:
• Fluid temperature applications – above 180° F (82° C) or below 40° F (4.4°
C)
• Pressure feeding of pumps over 500 psig (34.5 bar)
• Viscous fluid applications above 100 Cps
• Chemical compatibility problems
• Hot ambient temperatures – above 110° F (43° C)
• Conditions where pump oil may exceed 200° F (93° C) because of
a combination of hot ambient temperatures, hot fluid temperature,
and full horsepower load — an oil cooler may be required
• Pump rpm less than 200
Location
Locate the pump as close to the fluid supply source as
possible.
Install it in a lighted clean space where it will be easy to
inspect and maintain. Allow room for checking the oil level,
changing the oil (drain plug on the bottom of pump), and
removing the pump head components (inlet and discharge
retainer plates, manifold, and related items).
Rigging Provisions and
Procedures
Lift pump by attaching rigging to all four eyebolts (14).
Adjust attachment lengths to keep pump level during lifting.
CAUTION: Eyebolts (14) are rated to lift the weight of
the pump only. Also see center of mass references in
the Dimension Drawings Section.
Mounting
CAUTION: The pump shaft rotation direction is
indicated by arrows on the pump housing.
To prevent vibration, mount the pump and motor securely
on a level rigid base.
On a belt-drive system, align the sheaves accurately; poor
alignment wastes horsepower and shortens the belt and
bearing life. Make sure the belts are properly tightened,
as specified by the belt manufacturer.
On a direct-drive system, align the shafts accurately.
Unless otherwise specified by the coupling manufacturer,
maximum parallel misalignment should not exceed 0.015
in. (0.4 mm) and angular misalignment should be held to 1°
maximum. Careful alignment extends life of the coupling,
pump, shafts, and support bearings. Consult coupling
manufacturer for exact alignment tolerances.
MINIMUM LIQUID LEVEL
VORTEX
BREAKER
WEIR
PLATE
FEED IN
LINE VELOCITY
5-15 FT/SEC.
LONG-RADIUS
ELBOW
SUCTION LINE
VELOCITY 1-3 FT/SEC.
FULL-OPENING
VALVE
ECCENTRIC REDUCER
W/ FLAT SIDE UP
(OPTIONAL)
SUCTION
STABILIZER
AMPLE NPSHA
PUMP FLUID
CYLINDER
LINE VELOCITY
3-10 FT/SEC.
MINIMUM NUMBER OF ELBOWS
WITH AMPLE PIPE SUPPORTS
(OPTIONAL)
PULSATION
DAMPENER
RELIEF VALVE W/
10 PERCENT MAX.
PRESSURE
ACCUMULATION
PRESSURE
GAUGE
PRESSURE
GAUGE
Typical Installation
START-UP AND
CAPACITY-CONTROL
VALVE
W0511A
CHECK VALVE
65 psi cracking pressure
OIL LEVEL
MONITOR