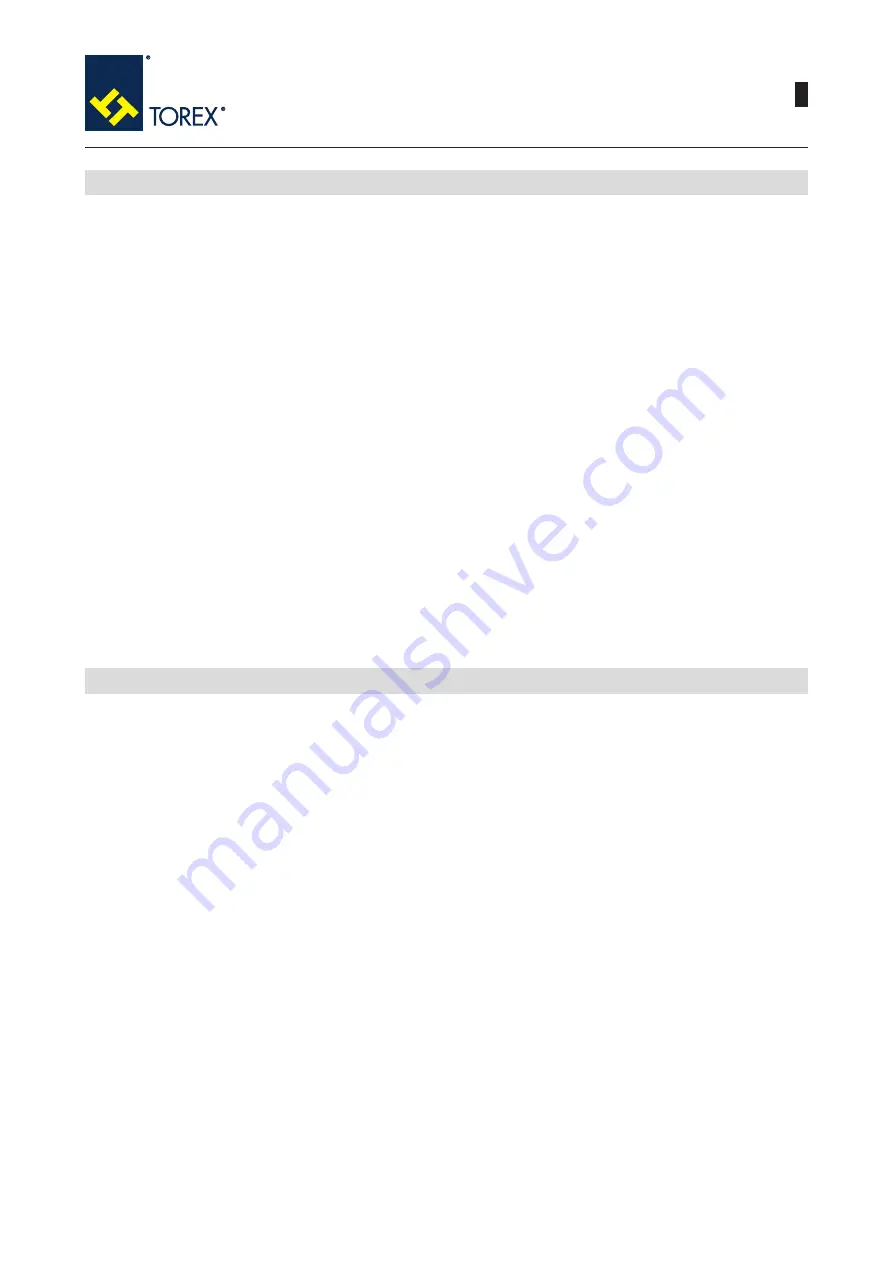
2.0 INFORMATION REGARDING SAFETY
VM
2
TOR.VM.--.M.A.0518.EN Issue: A
05.18
6
2.1 General safety prescriptions
2.2 Safety prescriptions for transport and handling
Carry out all the handling and transport operations in accordance with the procedures and instruc
-
tions shown on the packaging and in the Manual supplied.
All the operations must be performed by qualified authorized personnel.
Those authorized to carry out the handling operations must have the capabilities and experience re-
quired to adopt all the necessary measures to guarantee one’s safety and the safety of persons di-
rectly involved in the operations.
The chosen features of the lifting and handling means (crane, bridge crane, forklift truck etc.) must
take into account the weight to be handled, the dimensions and the gripping points.
Read the Instruction Manual carefully and strictly follow the instructions it includes, especially those
regarding safety.
Most accidents at the workplace are caused by negligence, failure to follow the most elementary safety
regulations and incorrect or improper use of tools and equipment.
Accidents can be prevented and avoided by taking due care, using suitable equipment and adopting
adequate preventive measures.
Apply and comply with the standards in force regarding workplace hygiene and safety.
The personnel trained for and authorized for the operations has to have the psychological/physical
requisites, experience in the sector concerned and the necessary technical skills for carrying out the
operations assigned to them.
All workers involved in any kind of operation must be prepared, trained and informed as regards the
risks and the behaviour to be adopted.
Pay attention to the meaning of the notices applied on the valve, keep these legible and respect the
information indicated.
Use instruments, equipment and tools that have been approved and are intrinsically safe, and cannot
alter the safety level of the operations or damage the valve during installation, use and maintenance.
Modifications to the valve components should not be made for any reason whatsoever, without the
Manufacturer’s permission.