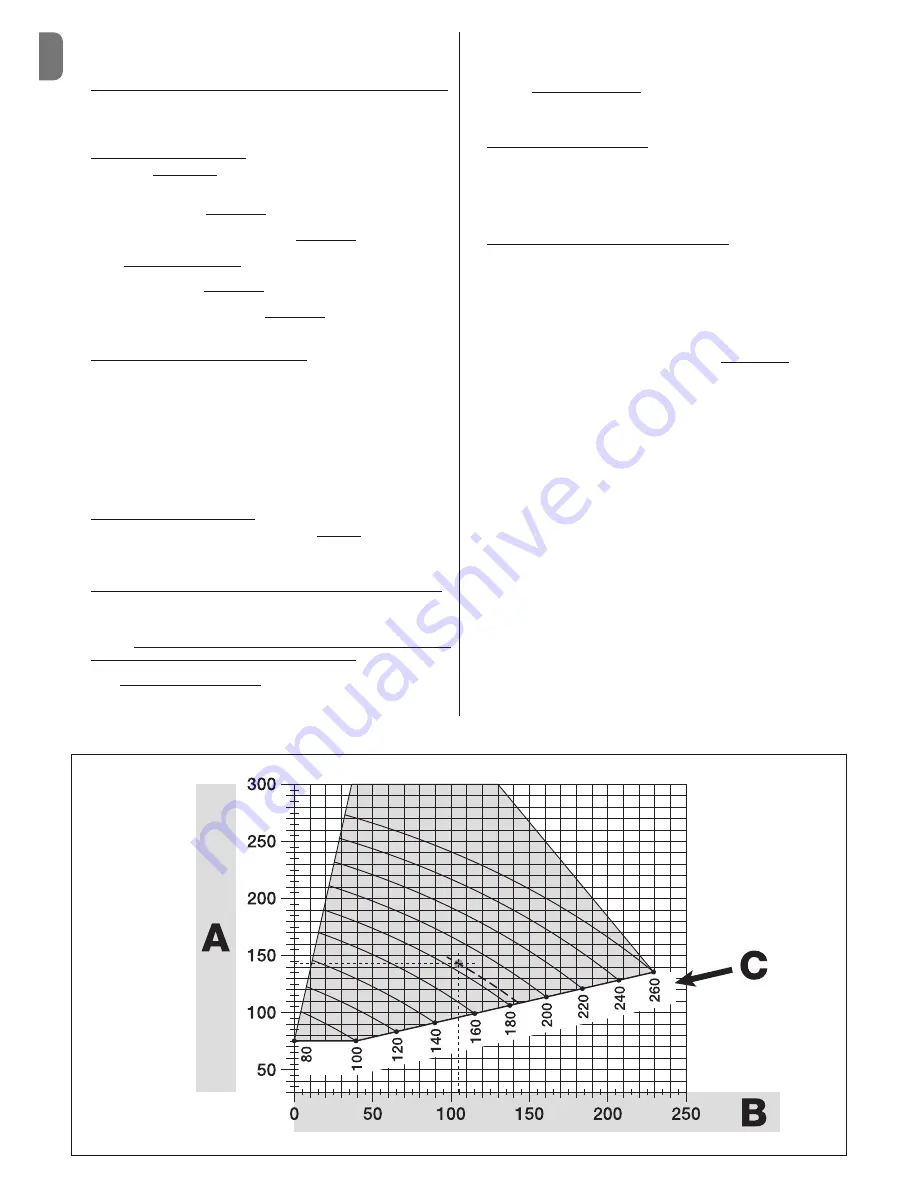
EN
4
– English
3.4.3 - Installation of a gearmotor with a SHORTENED ARM
Important!
- This part of the installation can only be carried out after 3.4.1
has been completed.
01.
Determine a new maximum opening angle for the gate leaf (max 90°):
ignoring the maximum opening position established for the leaf during pro-
cedure 3.4.1, bring the leaf to a new maximum opening position, ensuring
that the angle does not exceed 90°. Then hold the gate leaf provisionally
in
this position using a ground-mounted stop
.
02.
Determine distances A - B - C:
a)
Measure
distance B
(
fig. 10
) on the column. This is the distance
between the fulcrum of rotation of the gate leaf and the surface of the col-
umn where the rear bracket of the gearmotor will be fixed.
b)
On
Graph 2B,
mark
distance B
as measured, and trace a vertical line
from this point.
c)
On the column, determine the value for
distance A
, at which to mount
the rear bracket of the gearmotor (refer to
fig. 11)
.
N.B.! - Choose a value
for A, the smaller the better, in order to keep the motor free of the
obstacle.
d)
On
Graph 2B,
mark
distance A
as just measured and plot a horizontal
line from this point until it intersects with the vertical line traced earlier. The
meeting point of these lines defines
distance C
, i.e. the distance required
between the two pins on the slotted arm (
fig. 12
).
Example from graph 2B:
if the value of
B
is 105 mm and
A
is 143 mm, then point
C
is 182.
03.
Affix the gearmotor to the column (fig. 13):
a)
Hold the gearmotor against the column (
*
) so that its vertical centre line
corresponds with the vertical line traced earlier (distance A), and its arm
corresponds with the horizontal line traced during procedure 3.4.1. Now
ensure that the gearmotor is completely levelled: if off-axis, it can cause the
automation to malfunction.
(*) Note
- If the column surface is between 80 and 135 mm wide, then
before continuing with the installation, the gearmotor’s rear fastening
bracket will need to be rotated by 90°. To rotate the bracket, refer to
fig. 8
.
b)
Mark the fastening points, drill the required holes in the surface of the
column and insert the plugs; now fix the gearmotor in place using suitable
screws and washers.
04.
Shorten the slotted arm (fig. 14):
a)
To reduce the length of the slotted arm to
value C
(as established in
point 02-d), unscrew the nut, remove the stop, adjust the two pins so that
the distance between them is equal to value C, then fasten the nut in posi-
tion
provisionally
.
05.
Checking the length C of the slotted arm in this context (fig. 15 - 16):
a)
Bring the gate leaf into the fully Closed position;
b)
Fully open the gearmotor arm to its maximum extent (see
15, phase 1
);
c)
Bring the arm up to the gate leaf and hold the fastening bracket against
the leaf:
Important!
- push the curved arm against the leaf, until it is
secured (maximum opening - see fig. 15, phase 1a).
d)
Ensure that the gearmotor arm is levelled properly, and use a pencil to
mark
the centre
of the slot profile on the bracket, to enable fine adjust-
ments to be made to the closure alignment of the leaf in future (see para-
graph 3.7).
e)
Provisionally attach the bracket to the gate leaf and bring the leaf into its
maximum opening position against the ground-mounted stop.
f)
With the leaf in this position, perform the checks shown in
fig. 16
(run a
wire over the two pins of the slotted arm, as far as the leaf hinge).
Impor-
tant!
- If, in relation to the hinge, the wire appears in position “BB” as in
fig.
16
, it will be necessary to
extend distance C
by a few millimetres. This
must be repeated until the wire reaches position “AA” as in
fig. 16
and the
arm is no longer obstructed by the wall or other fixed obstacles.
06.
Cutting the slotted arm (fig. 17):
After checking that the articulation is operating correctly, cut the slotted
arm in the following manner.
a)
Trace a line on the slotted arm in the position exactly as indicated in
fig.
17
, phase 1. Then remove the arm from the bracket and cut the part of the
arm which is not required.
b)
Re-assemble the components of the arm (
fig. 3
).
07.
Affix the gearmotor arm tot he gate leaf (fig. 18):
a)
Drill holes in the gate leaf at the points marked.
b)
Remove the bracket from the arm and affix it to the gate leaf with suit-
able screws.
c)
Attach the arm to the bracket, inserting the pin and the Benzing retaining
ring.
Important
- Check that the bracket and the arm are completely level.
Loosen the screws of the bracket and adjust as required to ensure level.
This check can also be performed by measuring a distance of 75 mm (see
fig. 8
phase 2).
d)
Fix the end stops to the ground permanently, in the position determined
at the start of the procedure.
Important!
- Check that the gate leaf closes completely against the end
stop. To make fine adjustments to the closure alignment, refer to paragraph
3.7.
e)
Finally, bring the leaf manually to around its midpoint of travel and secure
the gearmotor using the dedicated key (see chapter 3.8) Then manually
open the leaf by a few more centimetres.
08.
If the gate being automated has two leaves, then to install the other gear-
motor repeat all the actions described here in chapter 3.4.
3.5 - Installation of the multi-purpose lamp mod. WLT on the
gearmotor model WL1024C
Warning
– WLT can operate as a flashing emergency light or courtesy light,
depending on the control unit programming.
Follow the installation steps shown in
fig. 21
, making sure the right sequence is
followed and the following warnings are adhered to:
•
for phase 4
– Rotate the power unit in the direction of the arrow, keeping a
careful eye on the cables underneath that connect it to the gearmotor.
•
for phase 7
– Open out the cables fully and insert the connector into the
FLASH output as shown; secure the cables by inserting them in the cable
gland.
•
for phase 11
– Position the electrical board on the pin of the base, depend-
ing on the desired usage:
A
= diffuse light;
B
= directional light beam (in this
case, the light beam can be directed by blocking the board in one of the holes
on the base).
GRAPH 2B
Summary of Contents for WL1024
Page 2: ......
Page 88: ......
Page 96: ...X 1 2 2a 385 mm 125 mm 85 mm ...
Page 97: ...3 XI 6 7 4 5 ...
Page 98: ...XII 1 2 3 4 45 45 1 3 a c b OK OK b a 8 a a b 5 6 7 8 9 10 11 12 13 ...
Page 99: ...XIII 75 mm 1 2 3 4 5 6 7 8 9 10 12 11 9 ...
Page 100: ...XIV 10 11 12 1 2 3 4 13 ...
Page 101: ...XV 15 2 1 4 3 2 1 14 16 2 1 ...
Page 102: ...XVI 2 3 4 1 17 2 1 4 6 3 5 18 ...
Page 103: ...2 1 19 2 1 4 6 3 5 20 XVII ...
Page 104: ...8 7 9 10 21 1 2 3 5 6 XVIII XVIII 4 ...
Page 105: ...XIX 1 2 3 1 3 2 B A 22 7 8 9 10 11 A 11 B 12 13 14 ...
Page 106: ...XX 23 24 1 2 3 4 5 6 ...
Page 108: ...XXII XXII 1 2 3 4 5 6 28 ...
Page 109: ...XXIII XXIII 29 30 1 2 3 4 5 6 ...