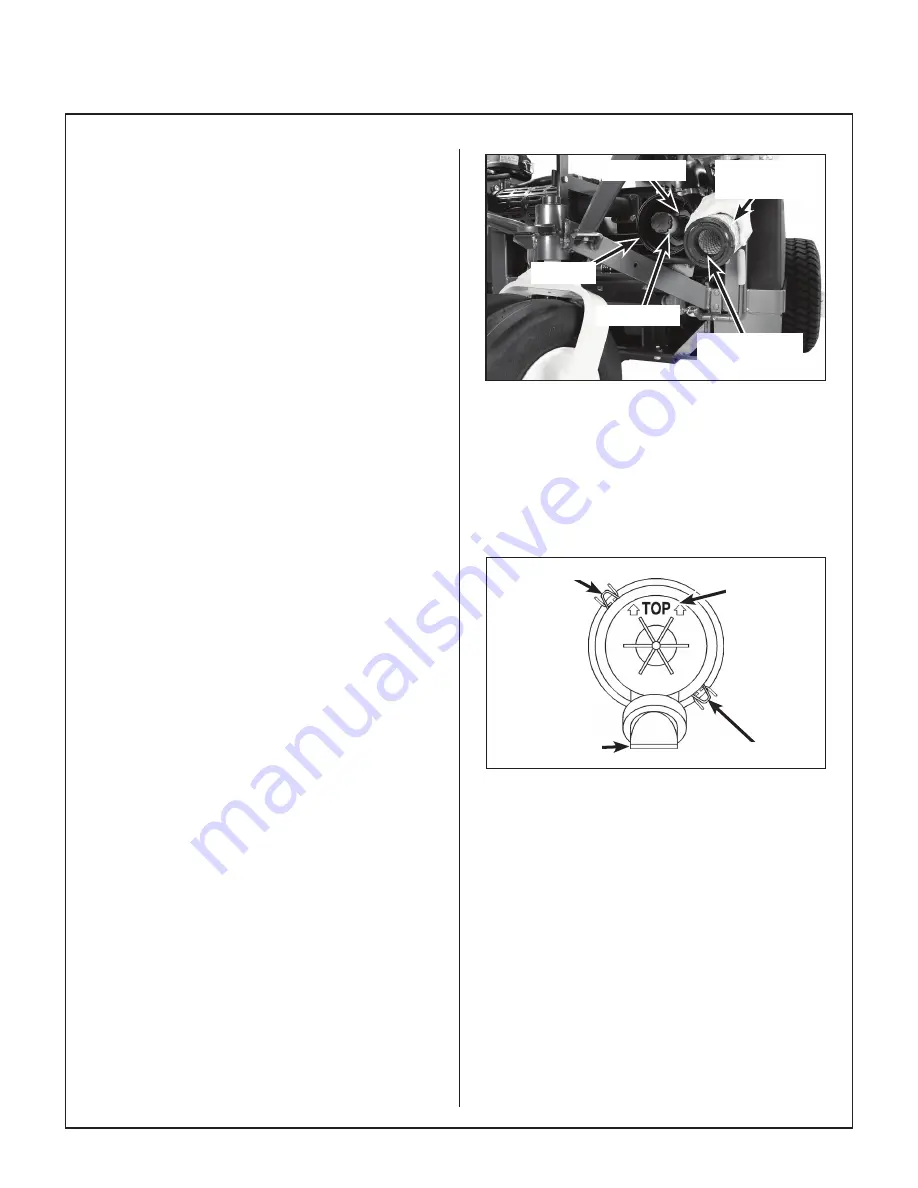
Maintenance Instructions
D21d
Cleaning
70
5. Check the condition and resilience of the radial
sealing surface (inside of the open end) of the
filter. Replace the filter if any cracks, tears, or
other damage to the sealing surface are not-
ed.
6. Without removing, visually inspect the condi-
tion of the safety filter for damage or holes.
The safety filter should only be removed for
yearly replacement
(or when dirty or dam-
aged).
IMPORTANT:
Prior to removing the safety
filter, make sure the inside surface of the air
cleaner canister is clean. This will minimize
the risk of dirt entering the outlet tube which
can cause premature engine wear.
7. After removing the safety filter, use a clean,
damp cloth and wipe the interior of the air
cleaner canister clean. Use special care to
clean
both the inside and outside
surfaces
of the outlet tube.
IMPORTANT:
Any dust left on the inside of
the outlet tube will go into the engine and
cause wear.
8. Check the outside surface of the outlet tube
for smoothness and cleanness (this is the
sealing surface).
9. Insert and seat the safety filter and primary
filter element carefully into the canister, apply-
ing pressure at the outer rim of the filter; not at
the flexible center. Make sure the filter ele-
ment is completely in place before installing
the cover.
IMPORTANT: DO NOT
use the
cover latch-
es
to force the filter into the canister–the cover
should fit on with
no extra force.
NOTE: DO NOT
use petroleum based lubri-
cants on the sealing surfaces of the filter; use
tal cum powder or dry silicone lubricants if
required for filter installation.
Radial Sealing
Surface
Primary
Filter Element
Canister
Safety Filter
Outlet Tube
Air Filter Element Replacement
10. Install the cover with the word “TOP” properly
oriented to the top of the canister. Give the
cover a slight twist as it reaches the canister to
make sure the tab inside the cover goes into a
slot, otherwise the cover will not fit properly.
Make sure both the top and bottom cover
latches are securing the cover in place.
Dust Ejection
Valve
Cover Latch
Cover Latch
Orient to Top
of Canister
Proper Orientation of Air Cleaner Cover
11. Check the air intake hose for cuts, nicks,
cracks, etc., and the hose clamps for tight-
ness.
12. Reset the air filter restriction gauge (press
button on the end of the indicator).
Engine Cooling System
Radiator Screen and Cooling Fins
To prevent the engine from overheating and pos-
sible engine damage, clean grass clippings, chaff,
and dirt from the fine mesh radiator intake screen
daily.
In certain mowing conditions (dry grass,
leaves, tree “cotton”, etc.), it may be necessary to
check and clean the screen several times during
use to prevent engine overheating.