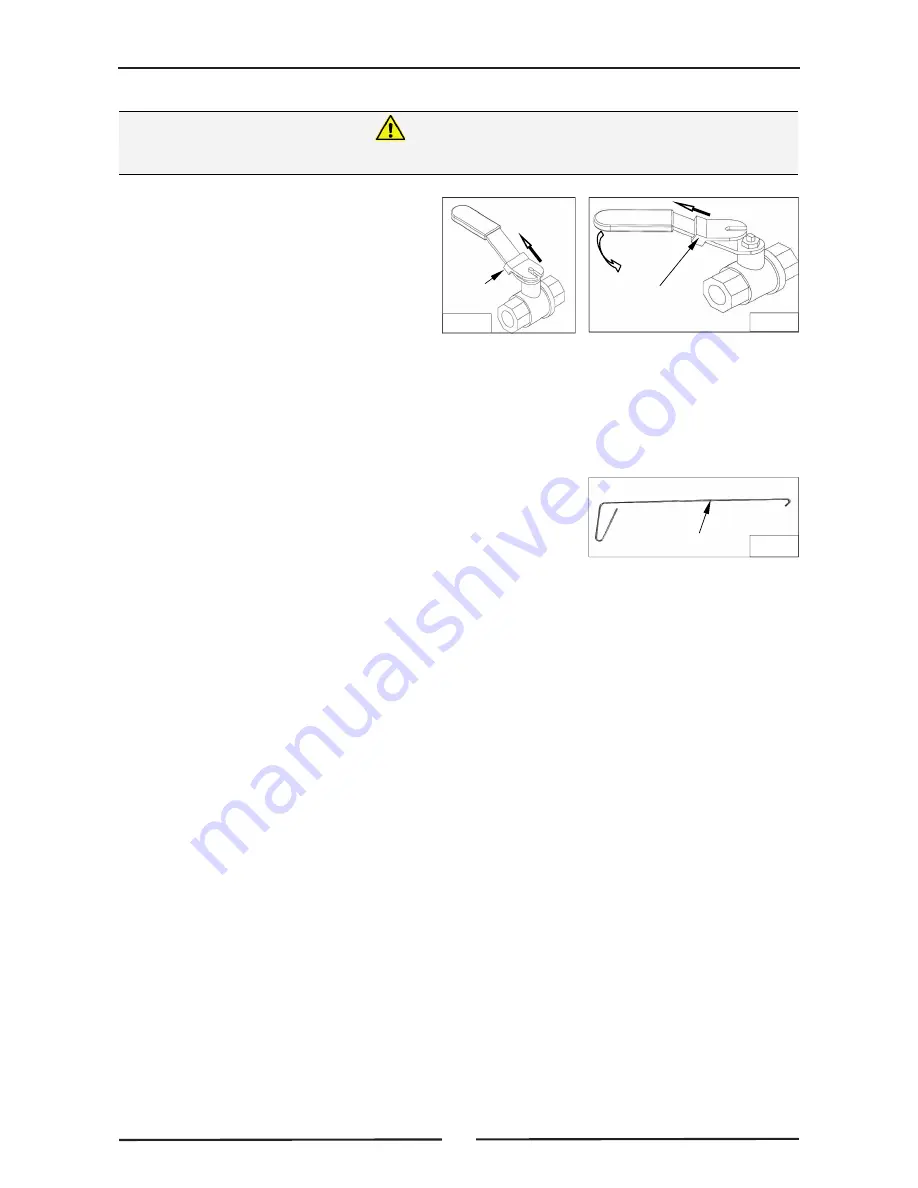
19
Cleaning and Maintenance
Opening the Drain Valve
a. Lift locking slide on valve handle
(Fig 11) to release valve.
b. While holding locking slide in
withdrawn position, rotate handle
anticlockwise (Fig 12) to open valve.
c. When valve is closed, locking slide will
drop down over locking valve to
prevent accidental opening of valve as
shown in Fig.11.
4.
Do not empty total fryer contents into one large container, as this will be dangerous and may be
difficult, when lifted up, to pour hot oil back into tank.
5.
Slip a muslin or other suitable filter bag over the end of the drain valve. Crumbs will be caught in
the bag but frying medium will strain freely through into receptacle.
6.
Open drain valve slowly to minimise splashing, and take care not to overfill container.
7.
If necessary, use the drain stick (see Fig 13) to dislodge any
blockages in the drain.
8.
When tank has been drained, use a ladle or small pan with a
handle and dip into hot frying medium from container and pour
around sides and bottom of tank to wash out crumbs and
particles adhering to tank.
9.
Continue to dip and pour until all crumbs are washed down and into filter bag.
10. Open drain valve fully and check for any particles or crumb residue lodged in valve. Clean out valve
with a stiff nylon brush. Do not use a wire brush as this can damage valve seating and will
eventually lead to leakage. If obstruction cannot be removed with a brush, use a wooden probe to
dislodge obstruction.
11. Wipe all exterior panels with a cloth dampened with detergent and rinse off any residue with clean
warm water.
12. Clean Control Panel with a damp cloth lightly moistened with a solution of water and a commercial
quality foodservice approved detergent.
13. Once the daily cleaning operation is completed, close drain valve and pour frying medium back into
tank.
H
OT
OIL
WILL
BURN
- D
O
N
OT
RUSH
THIS
JOB
.
Warning
Fig 12
Fig 11
Locking Slide
Locking
Slide
Fig 13
Drain Stick
Summary of Contents for FN8120GE
Page 37: ......