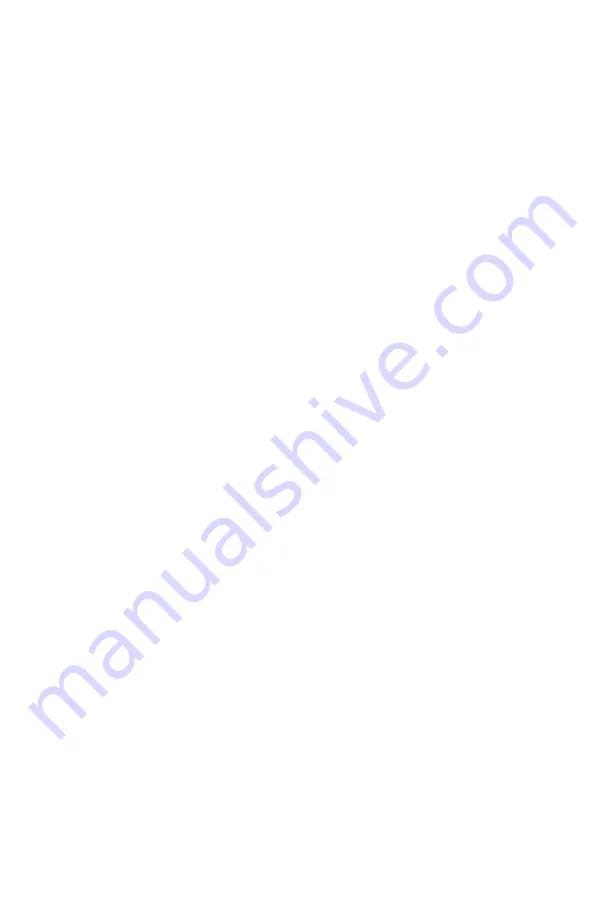
22
5.6 Calibration with Thermocouple Simulator
The Wahl Instruments thermocouple calibrator Model C65 may be utilized to calibrate
the Thermocouple Heat-Prober.
NOTE:
Allow the temperature of the meter to stabilize to the ambient temperature to
the environment. Typically, this will be 30 minutes.
1. Using the correct thermocouple wire (either “K” or “S” type), connect the
calibrator output to the Heat-Prober input terminals.
2. Set the C65 calibrator to the applicable TC mode, either “K” or “S”.
3. Set the C65 calibrator to output 3 2°F (0°C). Adjust R9 on the Heat-Prober
PC board for a display indication of 32°F (0°C).
4. Set the C65 calibrator to output to within 10% of the upper limit of the
Heat-Prober range. Adjust R22 on the Heat-Prober PC to display the same
temperature.
5. If interaction of adjustments are experienced, repeat steps 3 and 4 until no
further adjustment is required.
5.7 TA-70 Thermocouple Calibrator
The TA-70 Calibrator is a battery-operated, self-contained millivolt source which may
be conveniently utilized to calibrate and verify thermocouple-based temperature meas-
uring instruments such as Wahl Instruments’ Heat-Prober line.
Since the TA-70 is a millivolt-based instrument, the cold junction compensation is not
included. This requires that the ambient, or instrument temperature must be added to
the indicated temperature on the TA-70 selector switch.
For example:
if the ambient temperature is 70°F and the TA-70-selected calibration
temperature is 32°F, the actual output temperature of the TA-70 will be 70° + 32° = 102°F.
For the most accurate calibration of ambient temperature, utilize a thermometer with
accuracy of 0.5° traceable to NIST. Wahl’s 392M Platinum RTD meter with a 202
Summary of Contents for 2500MX
Page 8: ...4 Figure 2 1 Digital Heat Prober Major Features...
Page 14: ...10 Figure 3 2 Standard Wahl Probes Figure 3 3 Extension Probe Handle...
Page 16: ...12 Figure 3 4 Molten Metal Dipstick...
Page 28: ...24 Figure 5 2 Heat Prober with Wahl Calibrator...
Page 29: ...25 TP2 R29 R9 R20 TP1 R22 TP3 U 3 Figure 5 3 LED Adjustment Points...
Page 30: ...26 TP2 R29 R9 R20 TP1 R22 TP3 U 3 Figure 5 4 LCD Adjustment Points...
Page 32: ...28 Figure 6 1 Program Flow Chart...
Page 43: ...39 Figure 8 1 Block Diagram...
Page 44: ...40 Figure 8 2 LED Component Layout...
Page 45: ...41 Figure 8 3 LCD Component Layout...
Page 54: ...50 Figure 11 1 2500M Accessories and Special Purpose Probes...