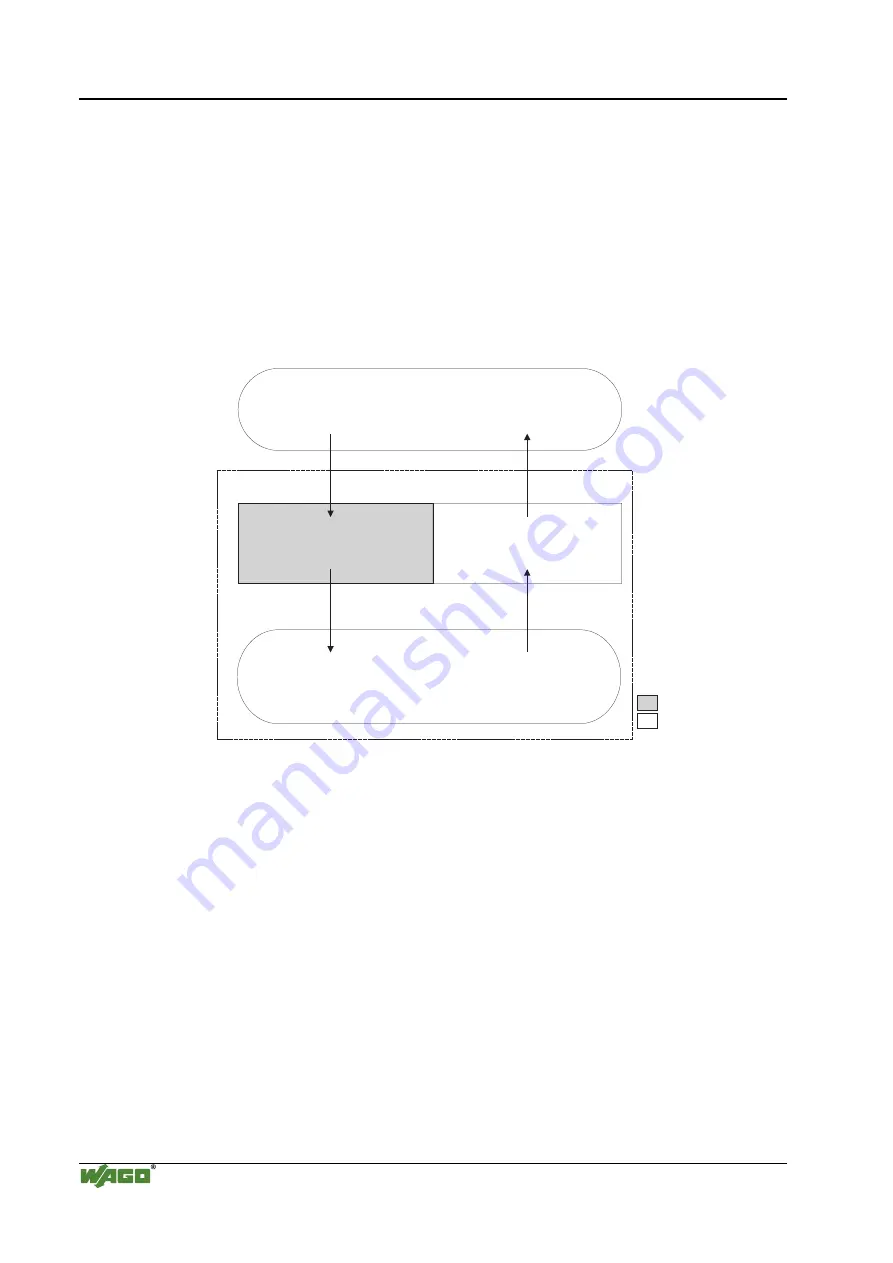
64 • Fieldbus Controller
Fieldbus Controller 750-872/020-000
WAGO-I/O-SYSTEM
750
ETHERNET TCP/IP
3.1.6.5 Data Exchange between PLC Functionality (CPU) and I/O Modules
Through absolute addresses, the PLC functionality of the controller can
directly address the I/O module data.
The PFC addresses the input data with absolute addresses. The data can then
be processed, internally in the controller, through the IEC 61131-3 program,
whereby the flags are filed in a permanent memory area. Following this, the
linking results can be directly written in the output data via absolute
addressing.
%IW0
%
Q
W0
%
Q
W255
%IW255
%IW512
%IW1275
%
Q
W512
%
Q
W1275
PII = Process Input
Image
PIO = Process Output
Image
Inputs
Outputs
I/O modules
750-4xx....6xx
PII
PIO
PLC functionality (CPU)
Inputs
Outputs
Programmable Fieldbus Controller
Fig. 3.1-10: Data exchange between PLC functionality (CPU) and I/O modules
15043e
3.1.6.6 Data Exchange between Master and PLC Functionality (CPU)
The fieldbus master and the PLC functionality of the controller regard the data
in a different manner.
Variable data created by the fieldbus master reaches the PFC as input
variables. Data created in the PFC is sent to the fieldbus master through
output variables.
In the PFC, the controller can access the MODBUS TCP PFC variable data
from word address 256 to 511 (double word address 128-255, byte address
512-1023) and the Ethernet IP PFC variable data from word address 1276 to
1531 (double word address 638-765, byte address 2552-3063).