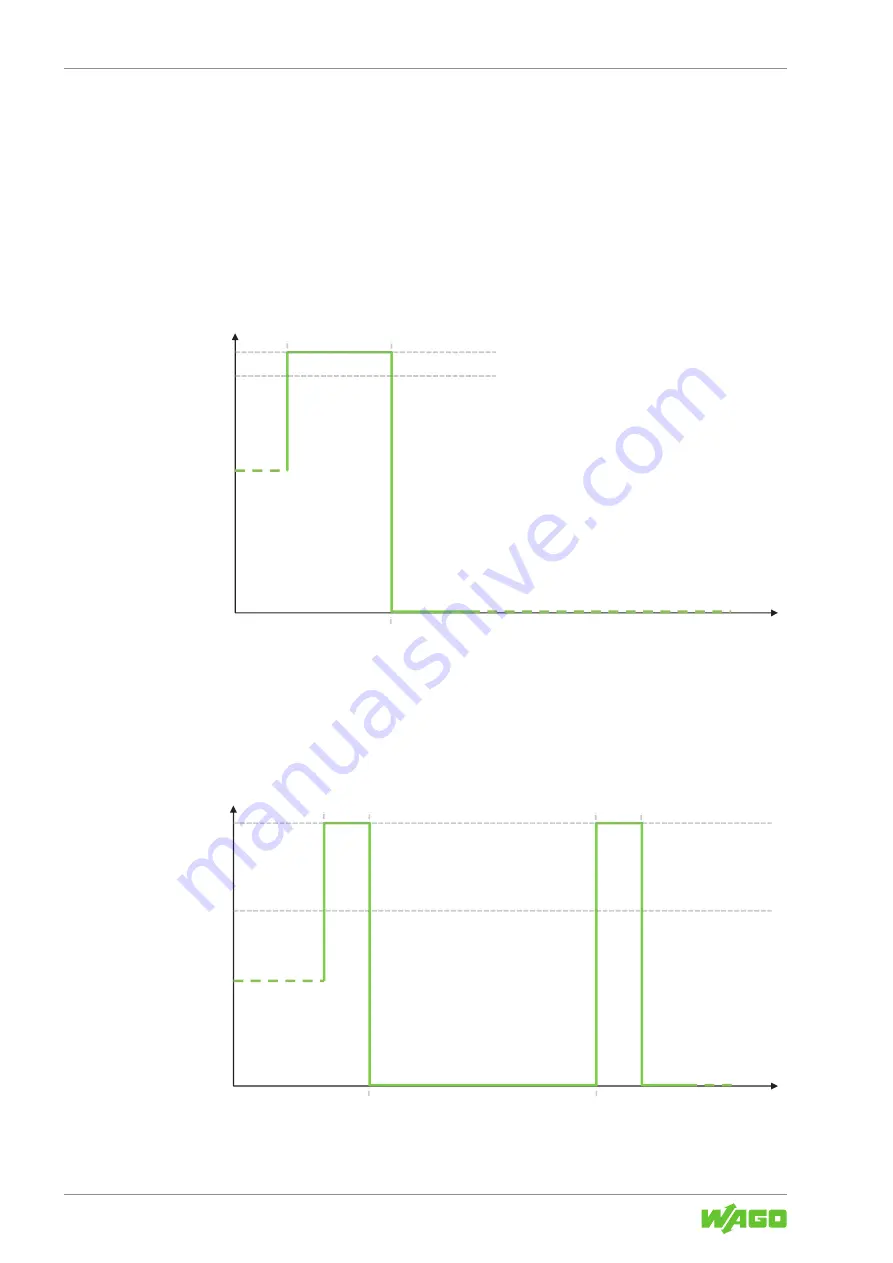
2787-2154
Notes on Operation
64
Product manual | Version: 1.0.2
Power Supply Pro 2
11.5.2 “Constant Current with Latching Shutdown” Mode
In this mode, the load current on the output is limited if the nominal output current is ex-
ceeded by a significant amount. The load current is limited to about 110 % of the nominal
output current. This occurs for 20 seconds.
If the overload lasts longer, the output is switched off. To switch the output back on, man-
ual intervention is necessary. The following options are available for this:
• Communication interface
• Buttons
• Digital input
t
>110%
100%
20s
I
OUT
/ I
N
Figure 40: “Constant Current with Latching Shutdown” Mode
11.5.3 “Hiccup” Mode
In this mode, the output voltage is switched off if the nominal output current is exceeded
by a significant amount. After a few milliseconds, the output voltage is switched back on
to check whether the overload is still present. If the overload is still present, the output
voltage is switched back off. This process repeats until the overload has been eliminated.
t
100ms
500ms
>150%
100ms
100%
I
OUT
/ I
N
Figure 41: “Hiccup” Mode