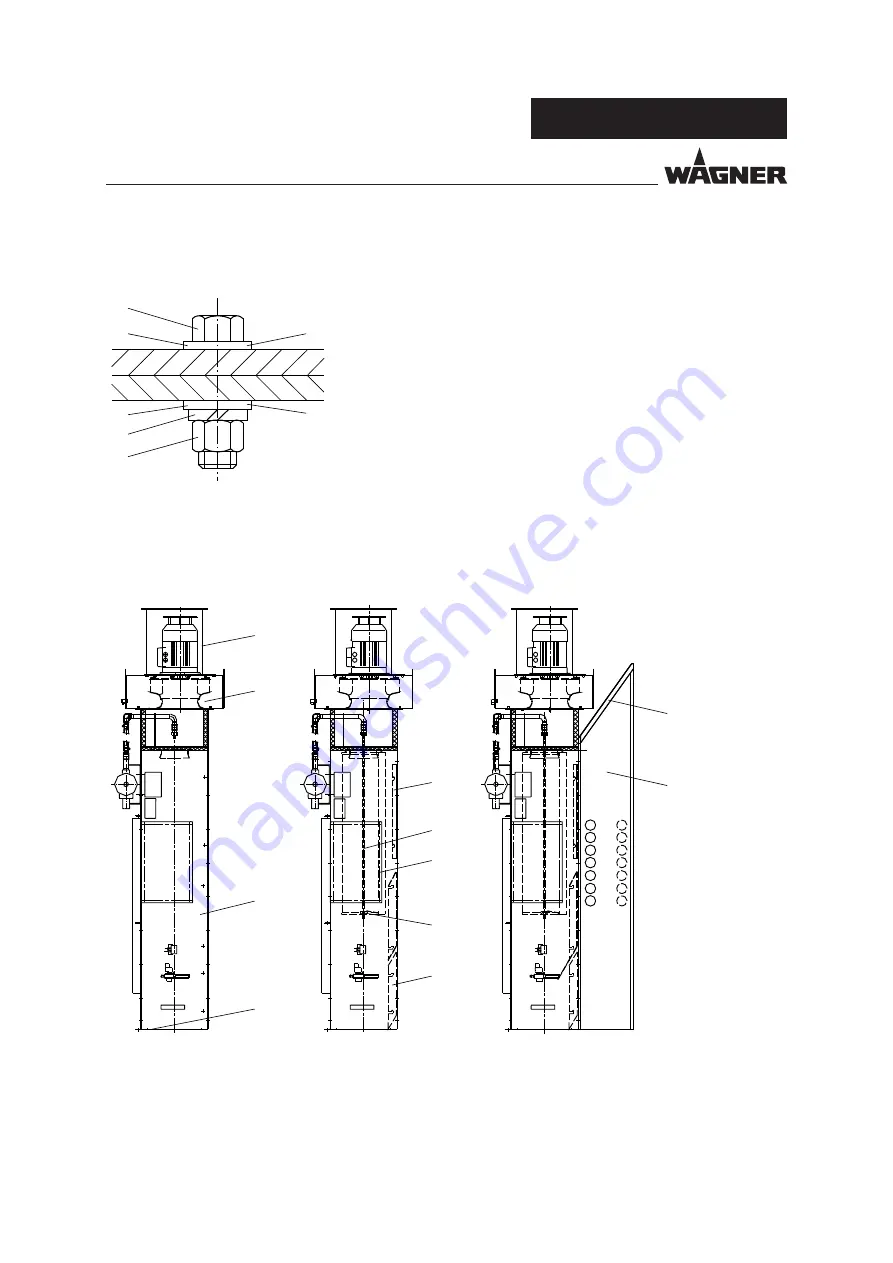
16
Basic 8000
.
A
B
B
C
D
B1
B1
P_00478
1
2
Y
X
6
4/1
3
4
5
7
8
P_00479
OPERATING MANUAL
VERSION 12/2010
ORDER NUMBER DOC 3305595
5.3
ASSEMBLY PROCEDURE
Hint:
On all connections on the booth, the M8 hexagonal screws must
have washers B below the screw head A and washers B plus
spring disks C below the hexagon nut D!
To assure a secure grounding between the elements of each
module, the washer B located in at least two positions of every
module must be replaced by a contact disk B1!
Summary of Contents for Basic 8000
Page 1: ...Spray wall Basic 8000 Version 12 2010 Translation of the original Operating manual ...
Page 2: ......
Page 35: ......