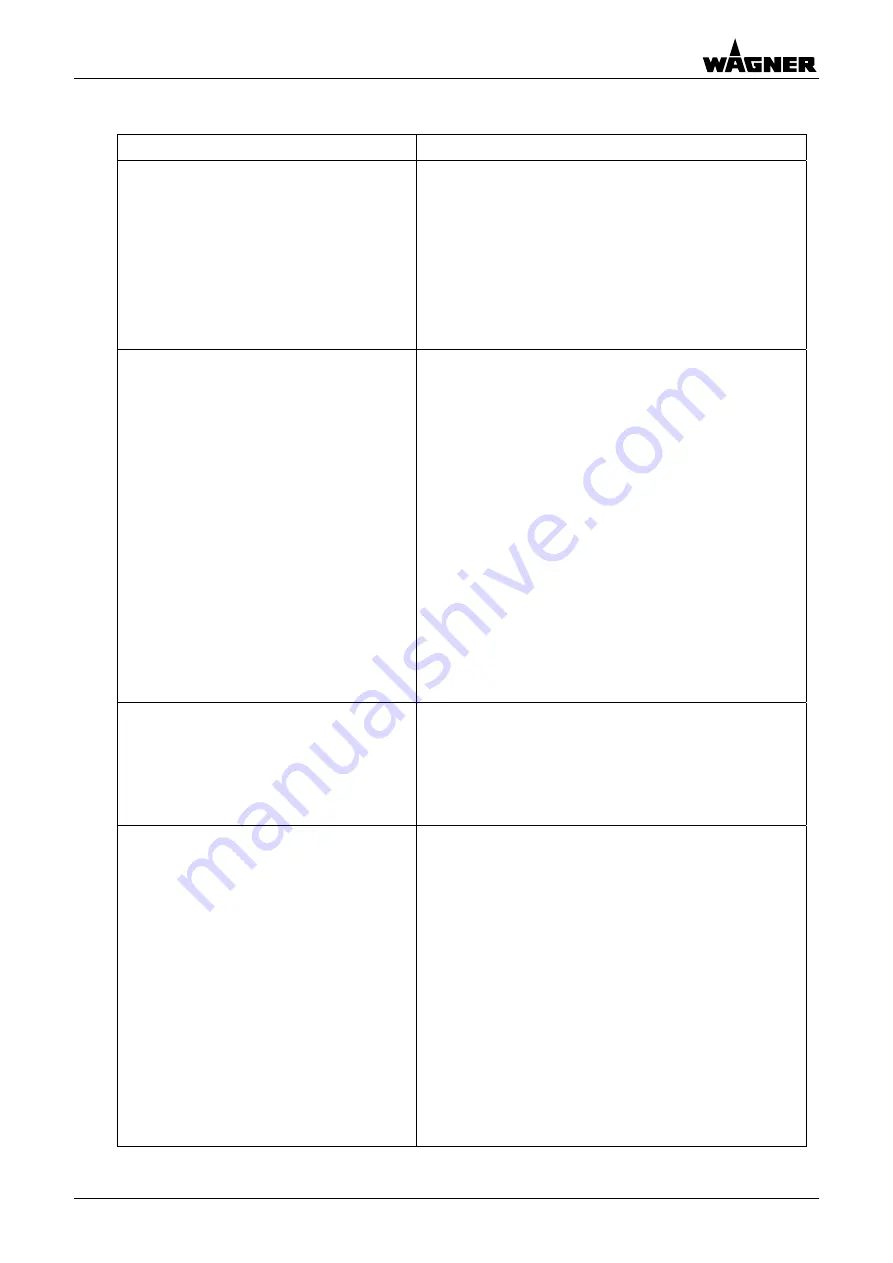
Safety regulations
05 / 2009
0351701
- PEA-T3XL
7
HAZARD PREVENTION
Electrostatic arcing may cause an explosion or fire.
Mixtures of powder and air can explode or ignite
causing property damage and/or severe injury.
•
Operator must be grounded. Grounding straps must be used
when wearing rubber soled shoes.
•
Operator must remove all metallic objects from his or her
person, which are not grounded.
•
The object being sprayed must be grounded.
•
All metallic objects within the spray area must be grounded
(including spray booth, part hangers, fire extinguishers, etc.)
•
Grounded conductive floor must be provided in spray area.
•
Turn off the Power Pack and unplug from outlet before flushing
out the gun, cleaning or replacing parts on the gun such as
changing tips.
Explosion or fire. Mixtures of powder and air can
explode or ignite causing property damage and/or
severe injury.
•
Exhaust and fresh air introduction must be provided to keep the
air within the spray area free of accumulation of flammable
atmosphere.
•
Smoking must not be allowed in spray area.
•
Fire extinguishing equipment must be present and in working
order.
•
Electrostatic arcing must be prevented.
(See Electrostatic arcing)
•
When cleaning the system, use only materials recommended
by the coatings manufacturer. Be sure Power Pack is turned off
and unplugged.
•
Avoid all ignition sources such as static electricity sparks, open
flames such as pilot lights, hot objects such as cigarettes and
sparks from connecting and disconnecting power cords and
working light switches.
•
To prevent hazardous concentrations of flammable
atmospheres, spray only in a properly ventilated spray booth.
•
Never operate spray gun unless ventilation fans are operating
properly.
•
Check and follow all National, State and Local codes regarding
air exhaust velocity requirements.
•
Ventilation must be maintained during the cleaning operation.
Toxic Substances: Some materials may be harmful if
swallowed or come in contact with the skin.
•
Follow the requirements of the Material Safety Data Sheet
supplied by the coatings manufacturer.
•
Exhaust and fresh air introduction must be provided within the
spray area to keep the air free of high powder accumulations.
•
Wear a mask or respirator. Read all instructions for the mask to
insure that it will provide the necessary protection against the
inhalation of powder.
General
•
Read all instructions and safety precautions before operating.
•
Comply with all appropriate local, state and national codes
governing ventilation, fire prevention, and operation of
Electrostatic equipment usage.
•
The United States Government Safety Standards have been
adopted under the Occupational Safety and Health Act. These
standards, particularly the General Standards, Part 1910 and
the Construction Standard, Part 1926, should be consulted.
•
NFPA Standard No. 33 is to be followed when setting up your
spray area. Contact the National Fire Protection Association,
Batterymarch Park, Quincy, Massachusetts, 02269 for more
information.
•
Check with insurance company for additional requirements.
•
Use only identical replacement parts.
•
Personnel must be given training in accordance with the
requirements of NFPA Standard No. 33 chapter 18.
•
It is the duty of all personnel responsible for the spray
equipment operation and maintenance to read and understand
all safety information furnished with this equipment.