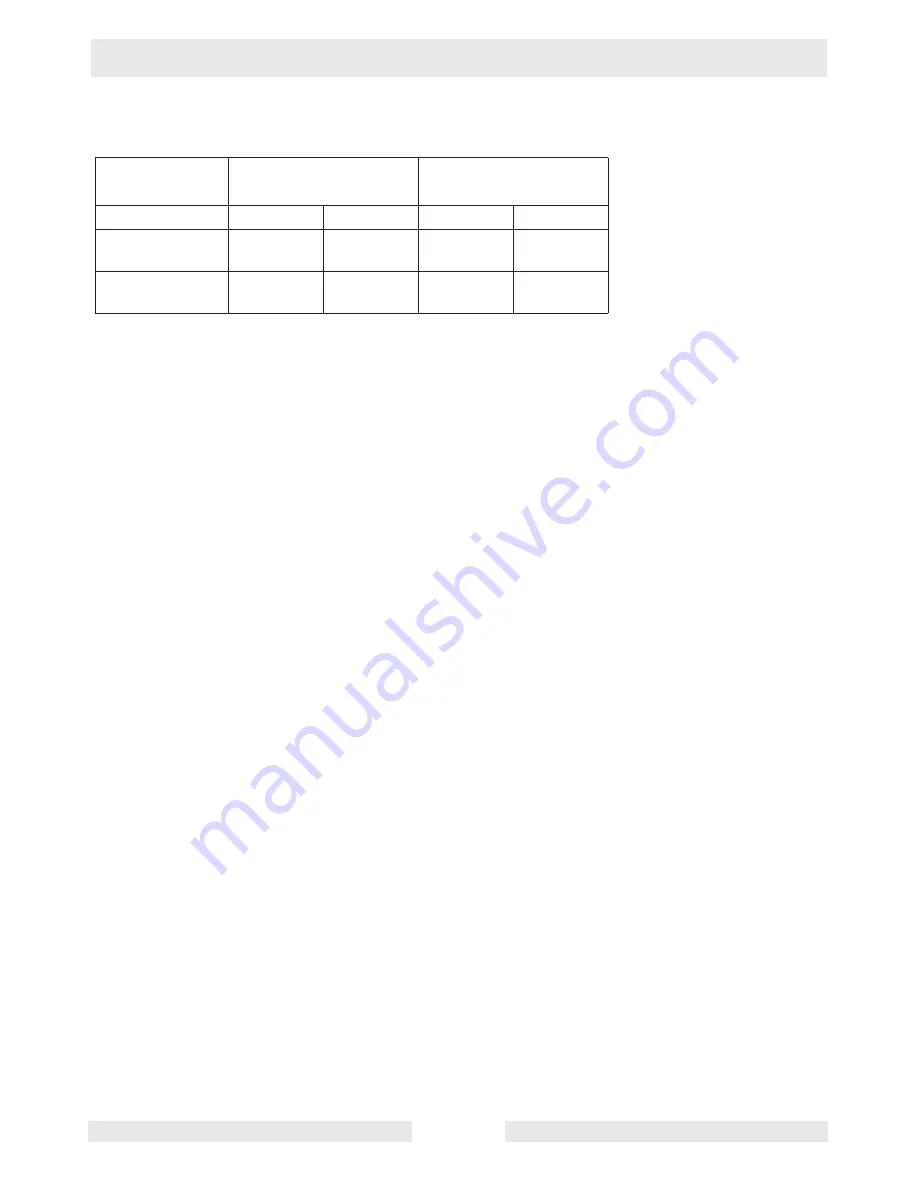
Technical Data
RD 12/RD 12A
wc_td000311gb.fm
132
11.7 Hydraulic Pressures
* Values for hard-packed surface shown. Values may differ depending on surface.
** Charge pressure: 11.4 – 12.8 bar (165–185 psi).
System
Operating Pressure
Relief Pressure
bar
psi
bar
psi
Drive**
55–69
800–1000
200
2900
Steering*
—while turning
0–41
0–725
45–51
650–725
Vibration
—single drum
55–76
800–1100
200
2900
Summary of Contents for RD 12A
Page 1: ...5000192242 02 0912 5 0 0 0 1 9 2 2 4 2 Repair Manual Roller RD 12 EN...
Page 15: ...RD 12 RD 12A Safety Information wc_si000302gb fm 15 1 4 Label Locations X FF...
Page 21: ...RD 12 RD 12A Safety Information wc_si000302gb fm 21 Notes...
Page 25: ...RD 12 RD 12A Operation wc_tx000865gb fm 25 53 47 54 61 50 62 55 wc_gr004114 56...
Page 29: ...RD 12 RD 12A Operation wc_tx000865gb fm 29 wc_gr002951 N F R 55 42 44 54 10 15...
Page 119: ...RD 12 RD 12A Disassembly Assembly wc_tx000671gb fm 119...
Page 120: ...Schematics RD 12 RD 12A wc_tx001073gb fm 120 10 Schematics 10 1 Hydraulic Schematic...
Page 122: ...Schematics RD 12 RD 12A wc_tx001073gb fm 122 10 4 Electrical Schematic A RD 12A...
Page 124: ...Schematics RD 12 RD 12A wc_tx001073gb fm 124 10 6 Electrical Schematic B RD 12A...
Page 126: ...Schematics RD 12 RD 12A wc_tx001073gb fm 126 10 8 Electrical Schematic RD 12...
Page 137: ......