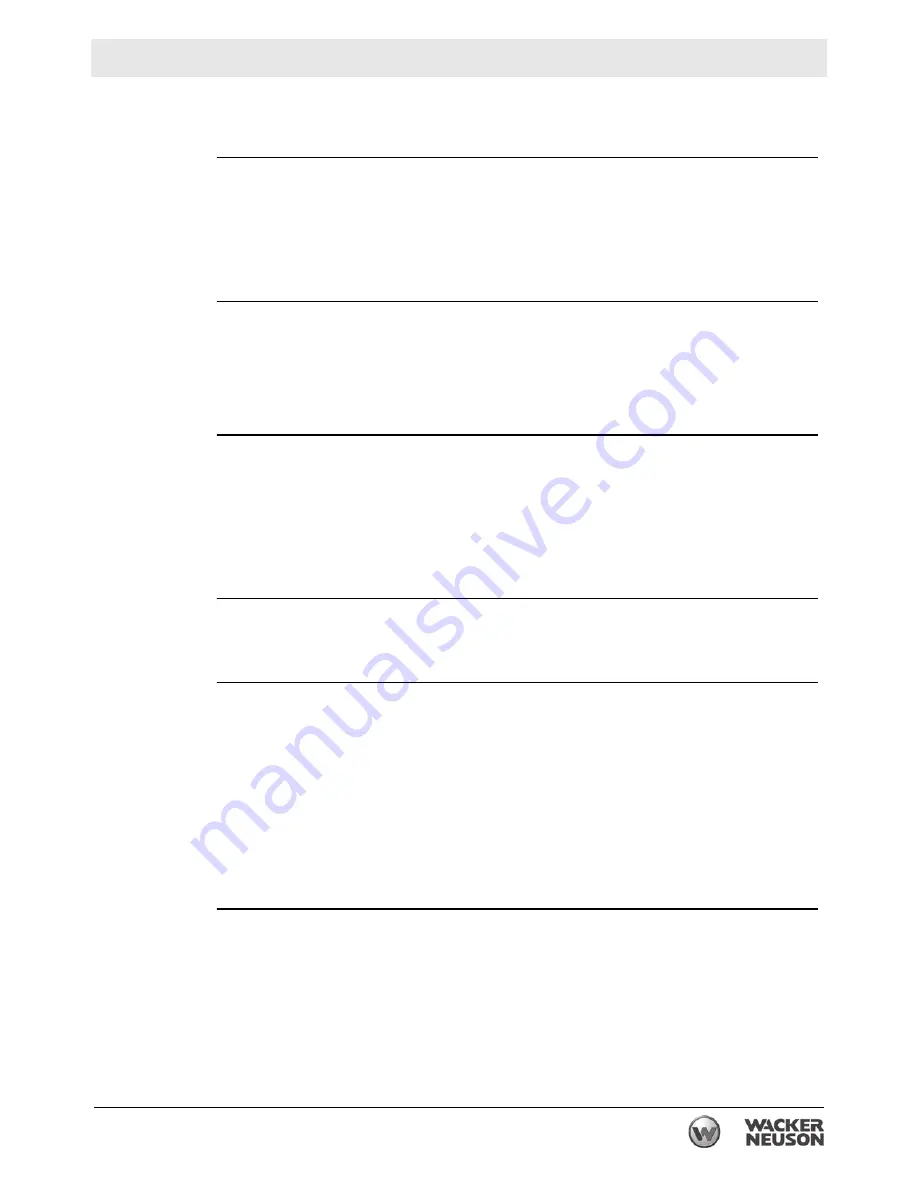
wc_tx003099gb.fm
43
LTN 6L-V
Maintenance
5.3
Cleaning the Machine
When
As needed
Requirements
Clean water supply
Mild detergent
Clean, dry cloths
NOTICE:
Do not use a pressure washer to clean this machine. Pressurized water
can severely damage the generator and sensitive electronic components.
Interior
Clean the interior of the machine.
Remove rags, containers, or other debris from the cabinet. Nothing should be
stored inside the machine.
Remove leaves and twigs from the exhaust pipe.
Wipe interior surfaces clean of oil, dust, and dirt.
Exterior
Clean the exterior of the machine with clean water and a mild detergent.
5.4
Inspecting the Machine
When
Daily
Overview
Inspect the machine before each use. A thorough inspection will help to identify
mechanical faults or potentially unsafe operating conditions. Correct these
problems before operating the machine.
External
inspection
Perform an external inspection of the machine. Check for:
External damage (dents, cracks, broken door latches, etc.)
Loose or missing fasteners
Loose or missing parts
Cut or worn insulation on electrical cords
Damaged light fixtures or lamps
Fluid leaks
Restricted air flow at the engine exhaust
Problems with the trailer (if equipped)—see “Maintaining the Trailer”
Internal
inspection
Open the access doors on both sides of the machine. Check for:
Damage to control panels, switches, or convenience receptacles
Loose or missing fasteners
Loose or missing parts
Loose or damaged hoses
Fluid leaks
Rags, containers, or other debris inside the cabinet