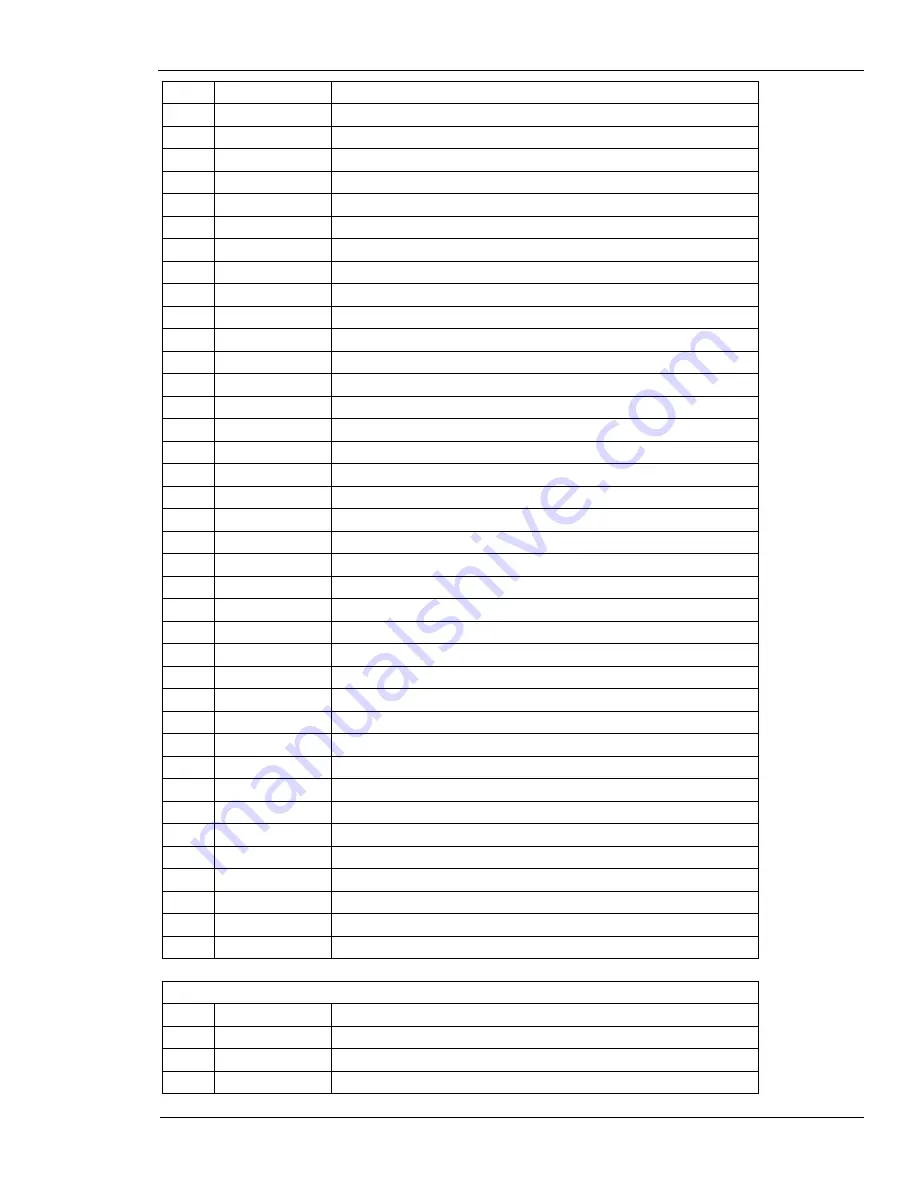
Chapter
8
,
Parts List and Ordering: Parts List
E.H. Wachs Company
Part No. 06-150-520-MAN, Rev. 0-0607
67
2
PIN, 1/4 x 5/8 LG DOWEL
4
PIN, 5/16" x 1-1/4" LG. DOWEL
2
PIN, 5/16" x 1-1/2" LG. DOWEL
4
PIN, 3/8" x 1-1/2" LG. DOWEL
1
PIN, 1/2" x 1" LG. DOWEL
3
PIN, 1/2" x 1-1/4" LG. DOWEL
8
PIN, 1/2 x 1-1/2" LG. DOWEL
2
PIN, 3/4" x 1" LG. DOWEL
2
PIN, 1" x 2" LG DOWEL
2
PIN, 1" x 2-1/2" LG DOWEL
2
PIN, 1/4" x 1-1/2" LG. ROLL (18-8 STAINLESS STEEL)
4
PIN, 3/4" x 3" LG. ROLL
2
SHCS, 3/8-16 x 2-1/4" LG. (18-8 STAINLESS STEEL)
6
SHCS, 1/2-13 x 1-1/4" LG. (18-8 STAINLESS STEEL)
4
SHCS, 1/2-13 x 1-1/2" LG. (18-8 STAINLESS STEEL)
4
SHCS, 1/2-13 x 3" LNG. (18-8 STAINLESS STEEL)
4
SHCS, 1/2-20 x 1-1/4" LG. (18-8 STAINLESS STEEL)
1
HHCS, 3/4-16 x 2-1/2" LNG - SS
2
FHCS, 1/4-20 x 7/8" LG. (18-8 STAINLESS STEEL)
7
FHCS, 5/16-18 x 1-1/4" LG. (18-8 STAINLESS STEEL)
8
FHCS, 1/2-13 x 1-1/2" LG. (18-8 STAINLESS STEEL)
4
FHCS, 1/2-20 x 1-1/2" LG. (18-8 STAINLESS STEEL)
6
FHCS, 1/2-13 x 1-3/4 (18-8 STAINLESS STEEL)
4
FHCS, 1/2-13 x 2-1/2" LNG. (18-8 STAINLESS STEEL)
2
FHCS, 3/4-10 x 4" LG. (18-8 STAINLESS STEEL)
10
HHCS, 3/8-16 x 1-1/4 (18-8 STAINLESS STEEL)
12
HHCS, 1/2-13 x 2" LNG. (18-8 STAINLESS STEEL)
4
HHCS-SS, 1/2-20 x 2-1/2" LG. (18-8 STAINLESS STEEL)
2
HHCS-SS, 3/4-16 x 3-1/2" LG. (18-8 STAINLESS STEEL)
1
HHCS, 1-8 x 2" LNG. (18-8 STAINLESS STEEL)
4
HHCS, 1-8 x 2-1/2" LNG. (BUMAX 109 MATERIAL)
2
HHCS-SS, 1"-8 x 3-1/2" LG. (18-8 STAINLESS STEEL)
4
HHCS, 1/2-13 x 1-3/4" LNG. (18-8 STAINLESS STEEL)
4
BHCS, 10-24 x 3/8 (18-8 STAINLESS STEEL)
4
WASHER, 1" (18-8 STAINLESS STEEL)
24
WASHER, 1/2" (18-8 STAINLESS STEEL)
8
LOCKWASHER, SPLIT RING 1/2" (18-8 STAINLESS STEEL)
8
NUT, HEX 1/2-13 (18-8 STAINLESS STEEL)
1
NUT, HEX JAM 3/4-16 (316 SS)
MECHANICAL AUTOFEED (DEFAULT)
Qty.
Part No.
Description
1
98-037-035
LEVER, FEED CONTROL
1
98-037-036
PIN, FEED LOCK-OUT
1
98-037-037
CAM, FEED OVERLOAD
Summary of Contents for Goliath Guillotine
Page 2: ...Goliath Guillotine Pipe Saw Part No 06 150 520 MAN Rev 0 0607 E H Wachs Company...
Page 8: ...Goliath Guillotine Pipe Saw 4 Part No 06 150 520 MAN Rev 0 0607 E H Wachs Company...
Page 20: ...Goliath Guillotine Pipe Saw 16 Part No 06 150 520 MAN Rev 0 0607 E H Wachs Company...
Page 22: ...Goliath Guillotine Pipe Saw 18 Part No 06 150 520 MAN Rev 0 0607 E H Wachs Company...
Page 58: ...Goliath Guillotine Pipe Saw 54 Part No 06 150 520 MAN Rev 0 0607 E H Wachs Company...
Page 64: ...Goliath Guillotine Pipe Saw 60 Part No 06 150 520 MAN Rev 0 0607 E H Wachs Company...
Page 74: ...Goliath Guillotine Pipe Saw 70 Part No 06 150 520 MAN Rev 0 0607 E H Wachs Company...
Page 76: ...Goliath Guillotine Pipe Saw 72 Part No 06 150 520 MAN Rev 0 0607 E H Wachs Company...
Page 77: ......
Page 78: ...E H Wachs Company 600 Knightsbridge Parkway Lincolnshire IL 60069 847 537 8800 www wachsco com...