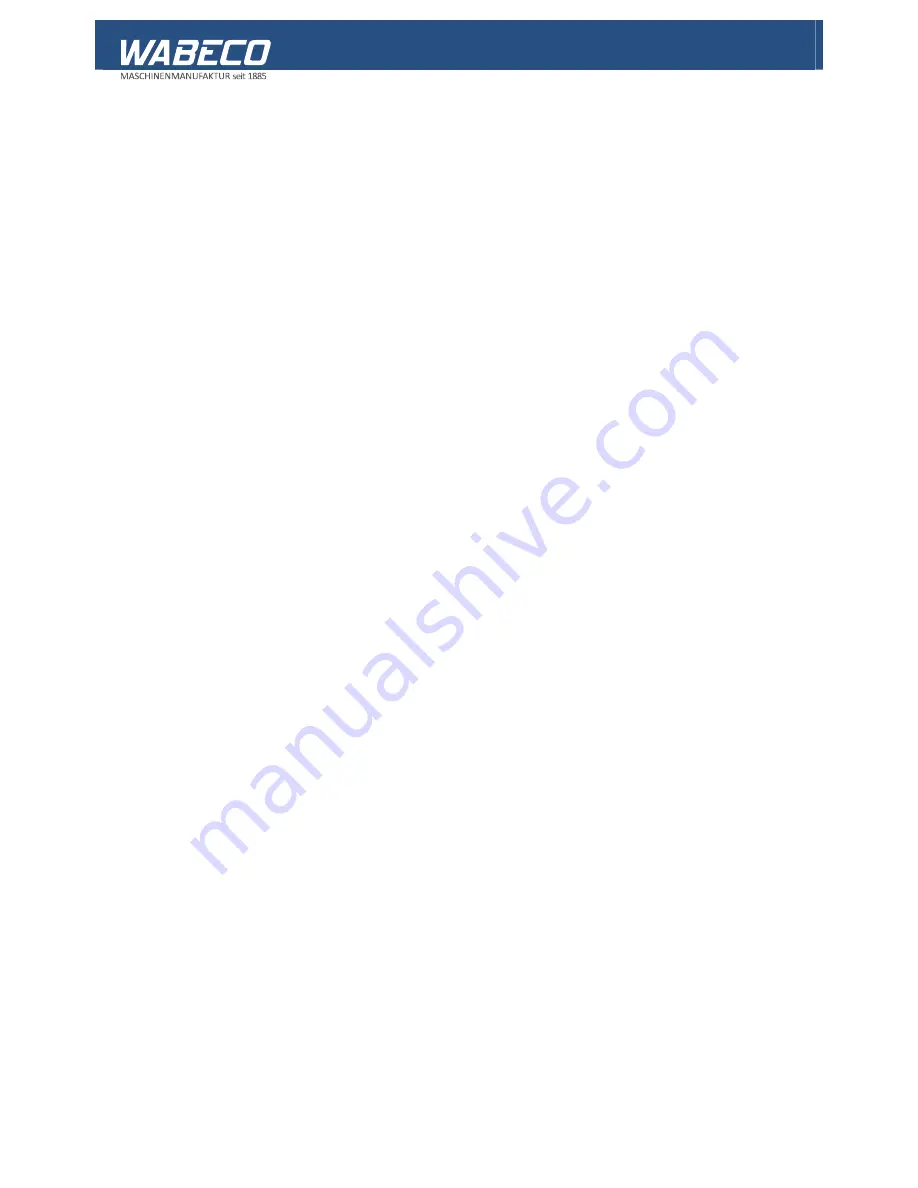
52
13. Maintenance
A long lifetime of the machine will depend on the appropriate care and maintenance.
All maintenance and repair tasks may only be carried out with the grounded plug pulled.
The machine must be cleaned after each use.
If the machine is set up in a wet room, all exposed parts must be oiled after each use to prevent
corrosion.
Always lubricate all moving parts well.
In the event of bearing or skid play, immediately adjust in order to prevent it from destroying the
bearing or skid guide.
Approximately every 100 operating hours
Clean the carbon brushes and collector of the drive motor (1.4 kW) with a piece of coarse
sandpaper.
Remove approximately 0.1 mm from the carbon brushes, then smooth out the contact surface with
fine sandpaper.
Check the tension of the gear belt and adjust if necessary
Check the play in the guides and feed spindles and set if necessary
14. Lubrication of the machine
The lubrication process:
■
Reduces wear and friction
■
Increases the lifetime
■
Protects metal surfaces from corrosion
We recommend
:
■
A class 2NLGI multi-purpose grease for lubrication
■
A lubrication oil with a viscosity of 100 mm
2
/s
for oiling
The machine is to be lubricated every 8 hours of operation in accordance with the lubrication plan.
The lubrication points.
■
Dovetail guide, base plate
■
Dovetail guide, upper skid
■
Dovetail guide, z-stand
■
Trapezoidal-threaded spindles
■
Sleeve and feed pinion (for sleeve stroke)
Are lubricated with the help of an oil can and an ordinary lubrication oil by moving the skid or sleeve
backwards and forwards.
All other lubrication points are lubricated with a grease press or a brush using multi-purpose grease.
Summary of Contents for CC-F1200 high speed
Page 42: ...42 6 Fitting and removing the tools 1 2 3 4 5...
Page 68: ...68 17 Drawings and legends 17 2 Electronic hood with 1 4 kW motor 17 2 2 CC F1200 CC F1210...
Page 70: ...70 17 Drawings and legends 17 3 Milling head with 1 4 kW motor...
Page 72: ...72 40 1 51004008 0002 Mounting pin 17 Drawings and legends 17 4 Milling head with 2 0 kW motor...
Page 74: ...74 17 Drawings and legends 17 4 Milling head with 2 0 kW motor...
Page 76: ...76 17 Drawings and legends 17 5 Z stand with vertical skid with trapezoidal threaded spindle...
Page 82: ...82 17 7 Lateral drive for z axis with trapezoidal threaded spindle 17 Drawings and legends...
Page 84: ...84 17 8 Cross slide support with trapezoidal threaded spindle 17 Drawings and legends...
Page 94: ...94 17 Drawings and legends 17 11 Z stand with vertical skid with ball screw spindle...
Page 100: ...100 17 Drawings and legends 17 13 Lateral drive for z axis with ball screw spindle...
Page 102: ...102 17 Drawings and legends 17 14 Cross slide support with ball screw spindle...
Page 114: ...114 17 Drawings and legends 17 20 Operating console for 1 4 kW motor...
Page 116: ...116 17 Drawings and legends 17 20 Operating console for 1 4 kW motor...
Page 118: ...118 17 Drawings and legends 17 21 Operating console for 2 0 kW motor...
Page 120: ...120 17 Drawings and legends 17 21 Operating console for 2 0 kW motor...
Page 122: ...122 17 Drawings and legends 17 22 Bracket arm for operating console...
Page 124: ...124 17 Drawings and legends 17 23 Industrial monitor and folio keyboard...