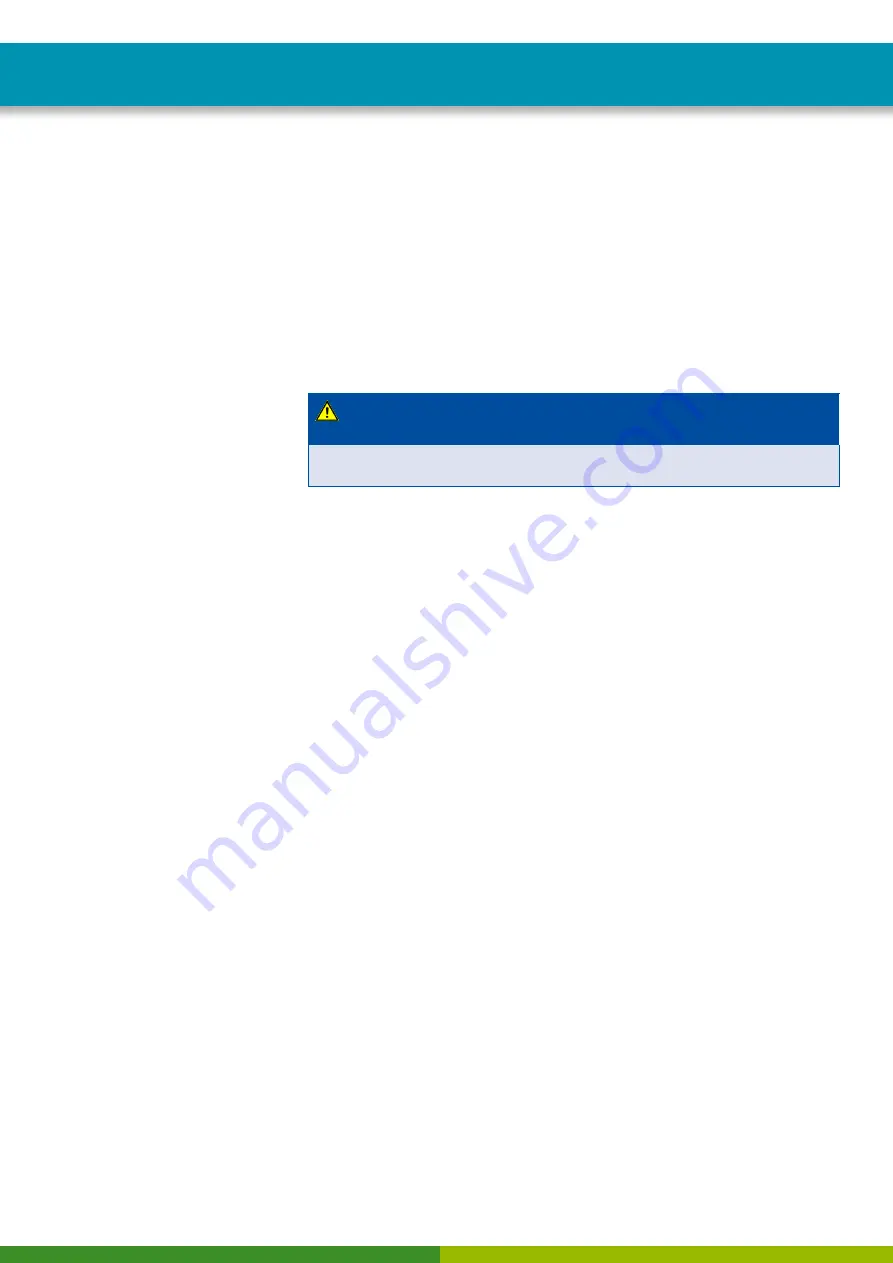
19
To enable ancillary autonomous braking actions, the additional valves familiar from the ABS braking system are
installed. There are only two main differences:
Here, the outputted braking pressure is not forwarded to an LSV regulator because its task is taken over by the axis
modulator. Instead, the braking pressure is fed to the control input of an additionally installed relay valve. The task
of this valve is to shorten the response time of the autonomous brake.
The output pressure of the relay valve then reaches the Tristop cylinders of the rear axle via the two likewise
additionally installed two-way valves (7).
5.3
Variant: Autonomous braking via a prepared interface for
TailGUARD™
To avoid any accidents, observe the following safety instructions for
vehicles with braking intervention through TailGUARD:
Vehicles with a prepared interface for TailGUARD:
TailGUARD may not
brake if the vehicle’s EBS system has a fault.
With this variant, separate valves do not have to be installed because the autonomous braking actions are effected
using the existing EBS service brake system of the towing vehicle.
Depending on the interface to the towing vehicle, the optical indications can be shown on the display on the vehicle's
instrument panel. Hardware can also be installed in the driver's cab by the vehicle manufacturer for the acoustic
signalling. Otherwise, a Trailer Remote Control can be used here as well for optical and acoustic indication purposes.
With this variant, the ECU is connected to the TailGUARD™ interface fitted the vehicle manufacturer by four multi-core
connecting cables. These are used, among other things,
to supply power to the ECU,
to transmit the request signal for the autonomous braking action,
to report error states,
and for connecting the ECU to the corresponding on-board CAN bus.
On the first available vehicle series with an optionally prepared TailGUARD™ interface, the Mercedes-Benz Econic
Euro 6, the vehicle interface comprises three multi-pin sockets X1, X2 and X3. The corresponding three connector
housings need to be obtained from the vehicle manufacturer, and are then fitted with the four connecting cables
supplied by WABCO.
Otherwise, the ECU is connected to a dedicated diagnostic socket as with the other two variants.
Required components: Overview
Summary of Contents for TAILGUARD
Page 1: ...TAILGUARD FOR REFUSE COLLECTION VEHICLES...
Page 2: ...2...
Page 40: ...40 Notes...
Page 41: ...41 Notes...
Page 42: ...42 Notes...
Page 43: ......