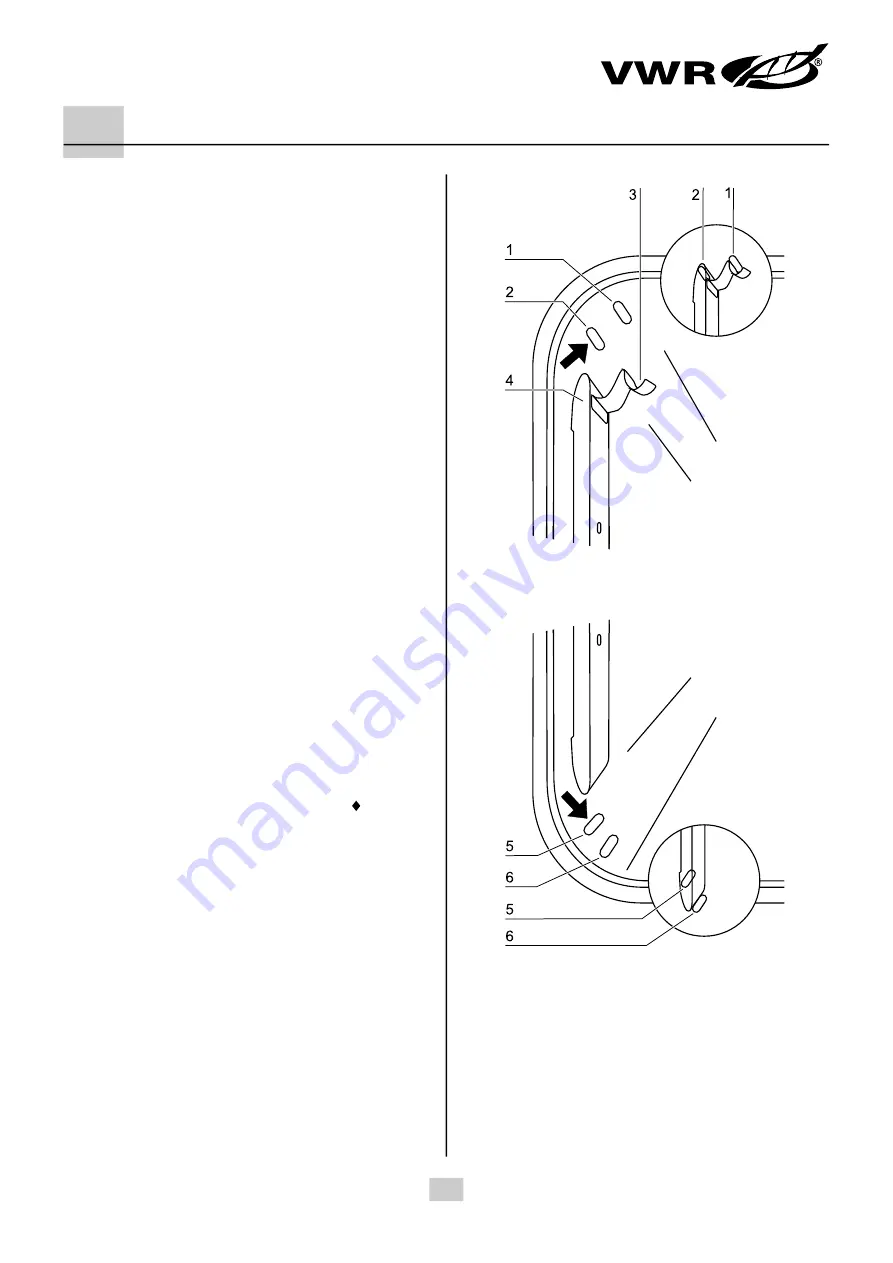
Operating Instructions | symphony 5.3 A – 06/2009
26
5
Start-up
5.1 Preparing the work space
The incubator is not delivered in a sterile state. Before
the initial start-up, the device must be decontamina-
ted.
Before the decontamination is performed, the follo-
wing work space components must be cleaned:
• Support rails,
• support hooks,
• shelves,
• work space surfaces,
• work space seals,
• glass door.
NOTE!
Decontamination:
For details about the cleaning and disinfec-
tion of the device, see Section 9!
5.2 Installing the shelf system
Tools are not required for the installation of the shelf
system. The support rails are secured using spring
pressure. After the support hooks have been inserted
into the rail, the shelves are pushed onto the support
hooks.
A
Support rail installation/removal:
Fig.10:
The support rails are held at the sides by
embossing [2] and [5] and secured by the embossing
[1] and [6]. The support rails marked with ( ) are inser-
ted at the rear panel of the device with the locksprings
[3] facing upward.
1. Position support rail [4] onto the lower embossing
[6] and tilt toward the work space side wall so that
the rail is positioned over the two embossings [5]
and [2].
2. Clamp lockspring [3] behind upper embossing [1].
3. To remove the support rails, pull lockspring tab
down and out of the embossing to remove rail.
Fig.10: Support rail installation/removal