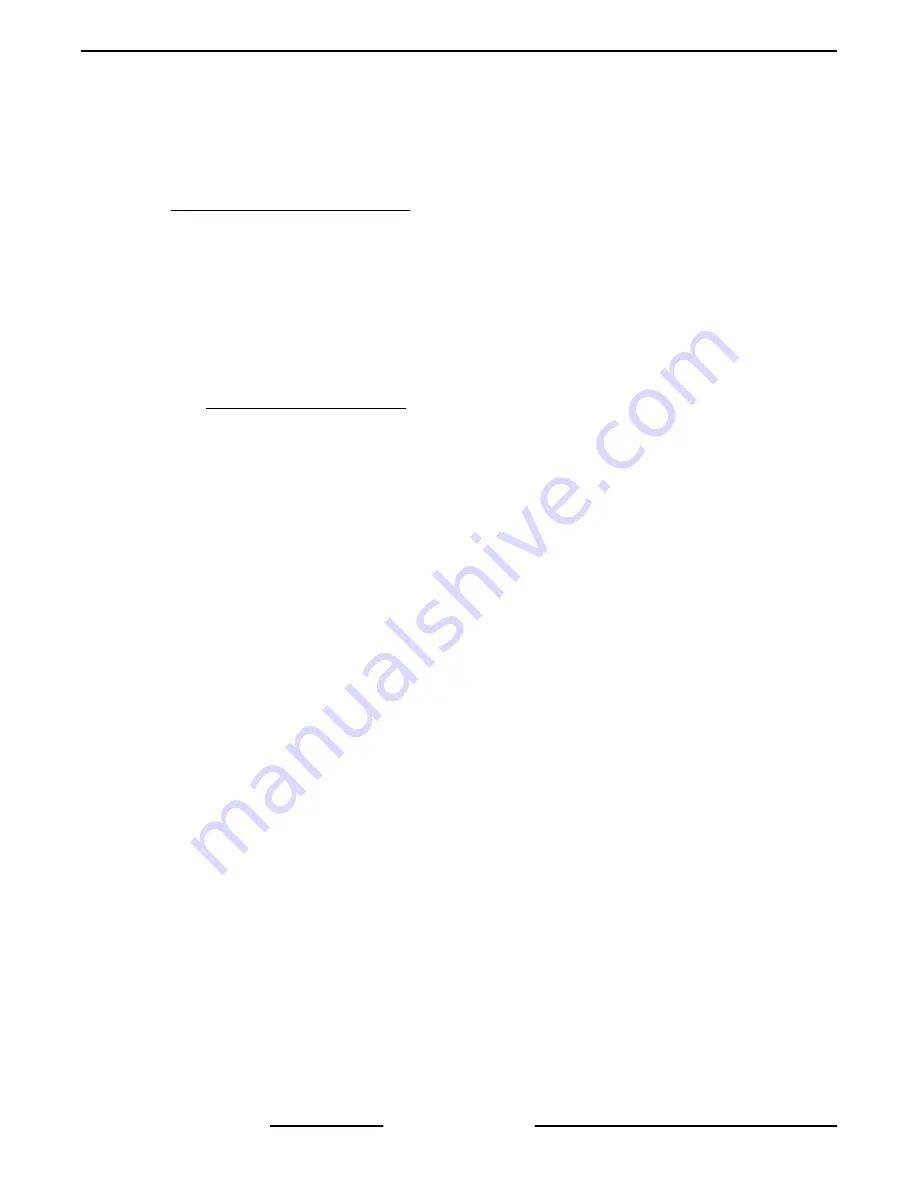
1.
Unbolt and remove the hand hole cover plate and
gasket assembly.
2.
Examine interior of boiler and if scalants and/or
lime build up is apparent, perform a boiler clean-
out and deliming procedure.
Refer to BOILER INSPECTION / CLEANING for
detailed instructions.
3.
If considerable scalants are evident, then both
the boiler blowdown solenoid valve and the water
level control must also be examined.
Gas Models
NOTE:
Low incoming gas pressure causes reduced
BTU output.
1.
Check incoming line and manifold gas pressures
as outlined in Manifold Pressure Adjustment.
2.
If the pressures are acceptable, check for:
•
Gas combination control valve malfunction.
If pressure adjustments are made and
manifold pressure remains low, replace the
combination valve and test unit for proper
operation.
NOTE:
After a period of time, gas burners can
accumulate carbon in their ports or become clogged
by food and grease debris from kitchen cleaning,
restricting performance.
•
Gas burner ports clogged or obstruction
around air shutter. To clean burners,
remove them from burner box and boil in
water for 10 -15 minutes to dislodge clog.
Clean-out any remaining debris from the
gas ports using a wire brush, scribe or pick
type metal instrument. Remove any other
foreign objects that appear to be obstructing
the gas ports or air shutters.
NOTE:
It is possible for debris to become lodged in
the small gas orifice opening over time.
•
Gas orifice clogged or obstructed around air
shutter. Clean-out the gas orifice using a
round metal instrument of the same hole
diameter or slightly smaller. Clean as
needed. If clogging reappears, the orifice
should be removed, cleaned and
reinstalled. Remove any other foreign
objects that appear to be obstructing the gas
orifice or air shutters.
Electric Models
Check for the following:
•
Heavy scale build up on heating element.
•
One or more electric heating elements
malfunctioning.
•
One or more magnetic contactors not activating
to power heating elements.
•
If unit operates under three phase power, then
one of the phases might be lost.
Direct Steam Models
Check for the following:
•
Low steam supply pressure.
•
Cooking compartment steam solenoid valve
malfunction.
•
Steam pressure regulator adjusted too low.
•
Clogging in the steam line.
Regenerated Steam Models
Check for the following:
•
Low steam supply pressure.
•
Cooking compartment steam solenoid valve
malfunction.
•
Heavy scale build up inside copper steam coil.
STRAINERS
Inlet Water Strainer
NOTE:
The in-line Y strainer should be located
upstream of the fill valve solenoid.
1.
Unscrew the cap from the Y-strainer leg pointing
toward the floor.
2.
Remove the screen and any foreign particles
trapped in the opening.
3.
Rinse the screen thoroughly to remove
accumulated debris and replace the screen in the
valve body.
4.
If screen can not be thoroughly cleaned, replace
it with a new one.
5.
Reinstall the cap. Ensure that the Y-strainer is
positioned so the cap is pointing downward to
catch debris.
Pressure Regulating Strainer
NOTE:
The pressure regulating valve strainer will
become clogged if dirty steam lines are connected to
direct steam models.
1.
Remove the hex nut on the bottom of the
pressure regulating valve.
2.
Remove the strainer.
3.
Clean the strainer and valve seat.
VSX BOILER BASE SERIES CONVECTION STEAMERS - SERVICE PROCEDURES
F24627 (0916)
Page 20 of 82