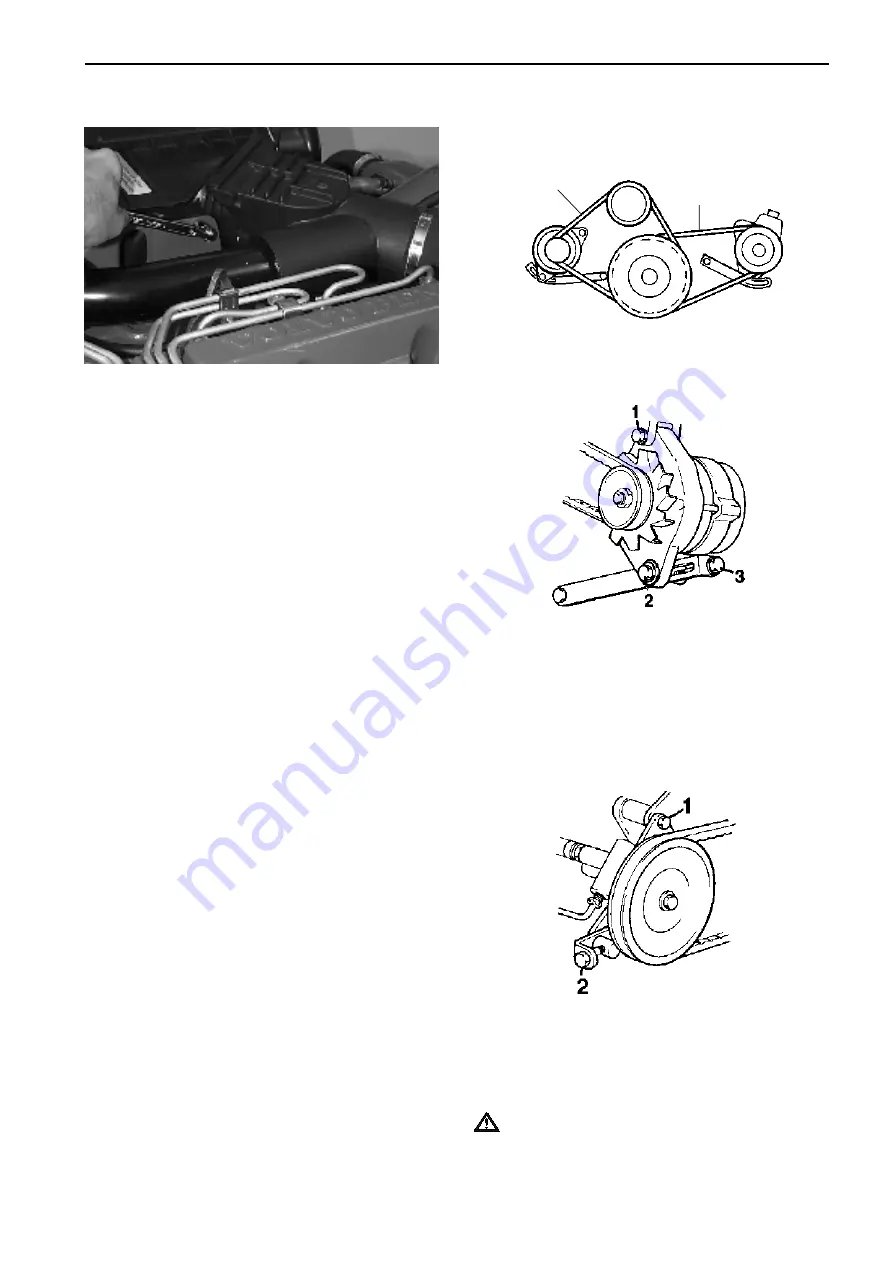
87
60
Install the air pipe compressor – air cleaner. Use new
O-rings and dip them in soap solution to facilitate in-
stalling the air pipe . Install air cleaner. Wrench 10,
11 mm. Install the pipe between the turbo – the air
cleaner – the compressor. The compressor terminals,
both intake and output sides are sealed with a silicon
sealing agent, such as Permatex ® No. 6 or Loctite ®
Silicon sealing.
61
Install the electrical box and connect all components.
Wrench 8, 10, 12, 13 mm.
Repair Instructions
Drive belts, tensioning, 31/41 series
62
Alternator belt
Undo alternator fixing screws (1) and (2). Tension the
belt with adjustment screw (4), so that the belt can be
pressed down about 10 mm between the pulleys at
(A). Tighten screws (1) and (2).
63
Servo pump belt
Undo retaining screw (1). Tension the belt with adjust-
ment screw (2), so that the belt can be pressed down
about 10 mm under normal thumb pressure between
the pulleys at (B). Tighten screw (1).
IMPORTANT! Re-check belt tension on all belts
after the engine has warmed up. Do this check
while the belts are still warm.
A
B
Drive belts, inspection points