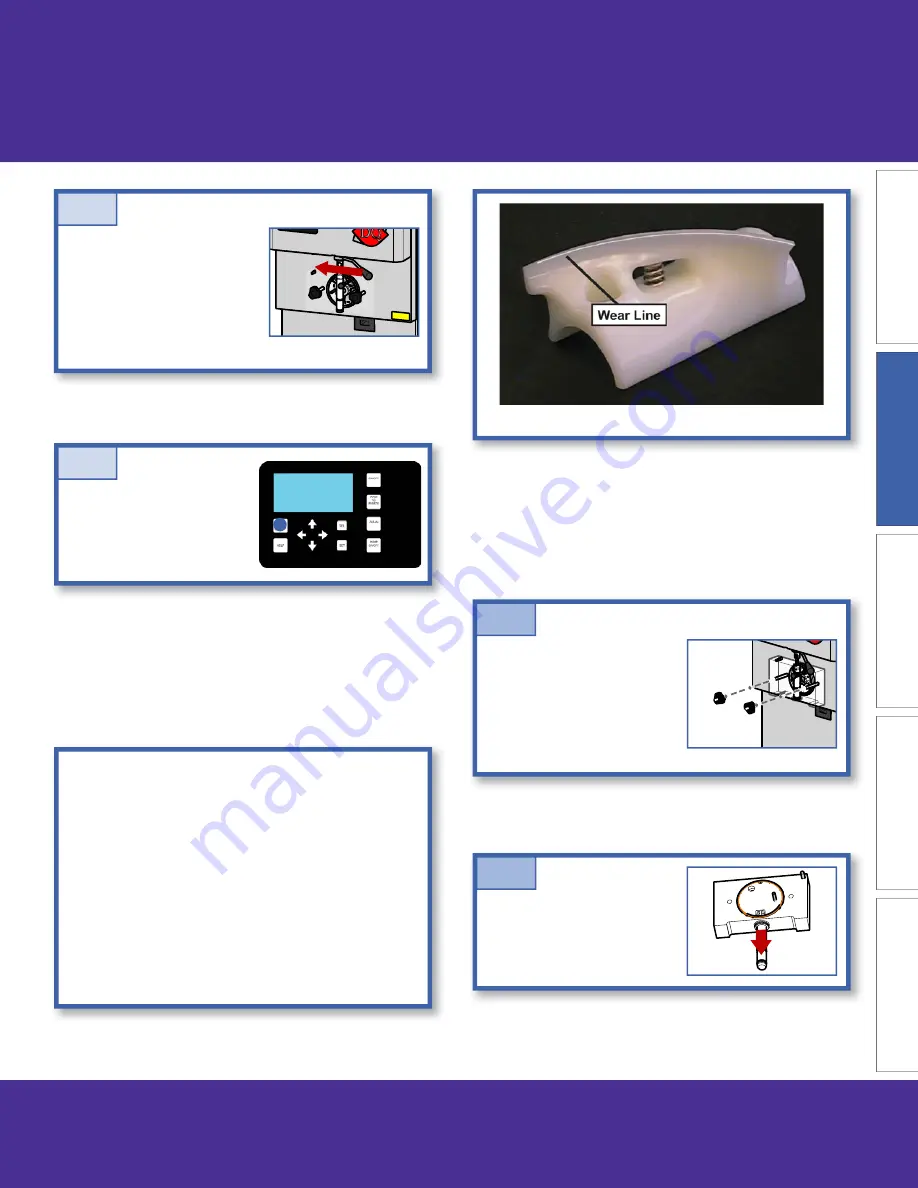
513687 REV.2
DQU411-I2 OPERATOR’S MANUAL
7
Section 2: Operation
MAINTENANCE
P
A
R
T
S
TROUBLESHOO
TING
OPERA
TION
INTRODUCTION
Before using the machine for the fi rst time, complete
machine disassembly, cleaning and sanitizing
procedures need to be followed. Routine cleaning
intervals and procedures must comply with the local
and state health regulations. Inspection for worn or
broken parts should be made at every disassembly
of the machine. All worn or broken parts should be
replaced to ensure safety to both the operator and the
customer and to maintain good machine performance
and a quality product. Check the wear line on the auger
fl ights on a regular basis and replace as needed.
B. Disassemble Parts
Auger Flight Wear
Press and hold the Main
Freezer Power button for
three seconds to turn off
the power.
A.8
1. Front Door Disassembly
Remove the spigot extension
or rosette cap if installed.
Unscrew the knobs on the
front door and remove the
door.
B.1
Remove the front door o-ring
and remove the spigot from
the front door.
B.2
Remove the bucket in the
cab and turn on the pump to
clear any remaining liquid in
the hoses.
Open the spigot to drain the
freezing cylinder.
A.7