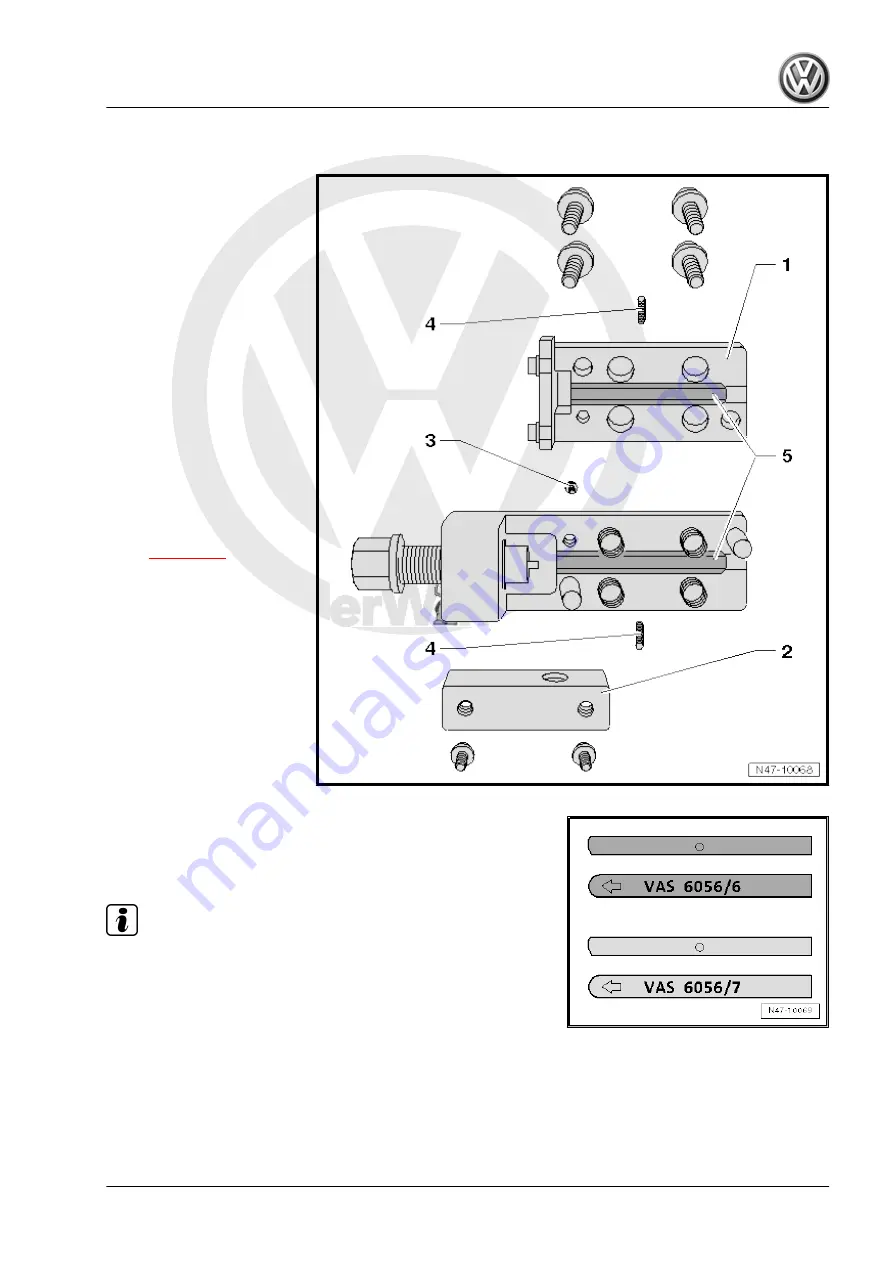
Pro
te
c
t
ed
b
y
co
p
y
rig
h
t.
C
o
p
y
in
g
fo
pr
iv
a
t
e
o
r
c
o
m
m
e
r
c
ia
l
p
u
rp
o
s
e
s
,
i
n
p
a
rt
o
r i
n
w
h
o
le
,
is
n
o
t
p
e
r
m
it
t
e
d
u
n
l
e
s
s
a
ut
ho
r
i
s
ed
b
y
V
olk
sw
a
ge
n AG
.
V
olk
s
w
a
g
en
AG do
es
n
ot g
uar
ante
e
or a
c
c
ep
t
a
ny
li
a
b
i
li
t
y
w
ith
r
e
s
p
e
c
t
t
o
th
e
c
o
rr
e
c
t
n
e
s
s
o
f
in
fo
r
m
a
tio
n
in
th
is
d
o
c
um
en
t.
C
o
py
rig
ht b
y
V
olk
sw
a
ge
n
A
G.
9.1
Assembly overview - flanging tool
1 - Flanging tool upper part
❑ Unbolt to change flang‐
ing jaws
2 - Fastening for handle
❑ Must be removed to ac‐
cess retaining screw for
upper part
3 - Retaining screw
❑ For flanging tool upper
part
4 - Grub screws for flanging
jaws
❑ For centring and holding
flanging jaws
❑ Hexagon socket head
bolt, 2 mm
5 - Flanging jaws
❑ Various
❑ Assembly instructions
Flanging jaw assembly instructions:
♦ VAS 6056/6 (dark) for black brake lines
♦ VAS 6056/7 (light) for green brake lines
Note
The arrow on the rounded side of the flanging jaws must point to
the edge of the housing, and the straight side of the flanging jaws
must be installed towards the spindle, or the flange will not be
formed correctly.
9.2
Work instructions
– Unbolt relevant brake line at brake caliper or wheel brake cyl‐
inder; catch escaping brake fluid and dispose of this as per
regulations.
Touareg 2010 ➤
Brake systems - Edition 05.2011
9. Repairing brake lines
103