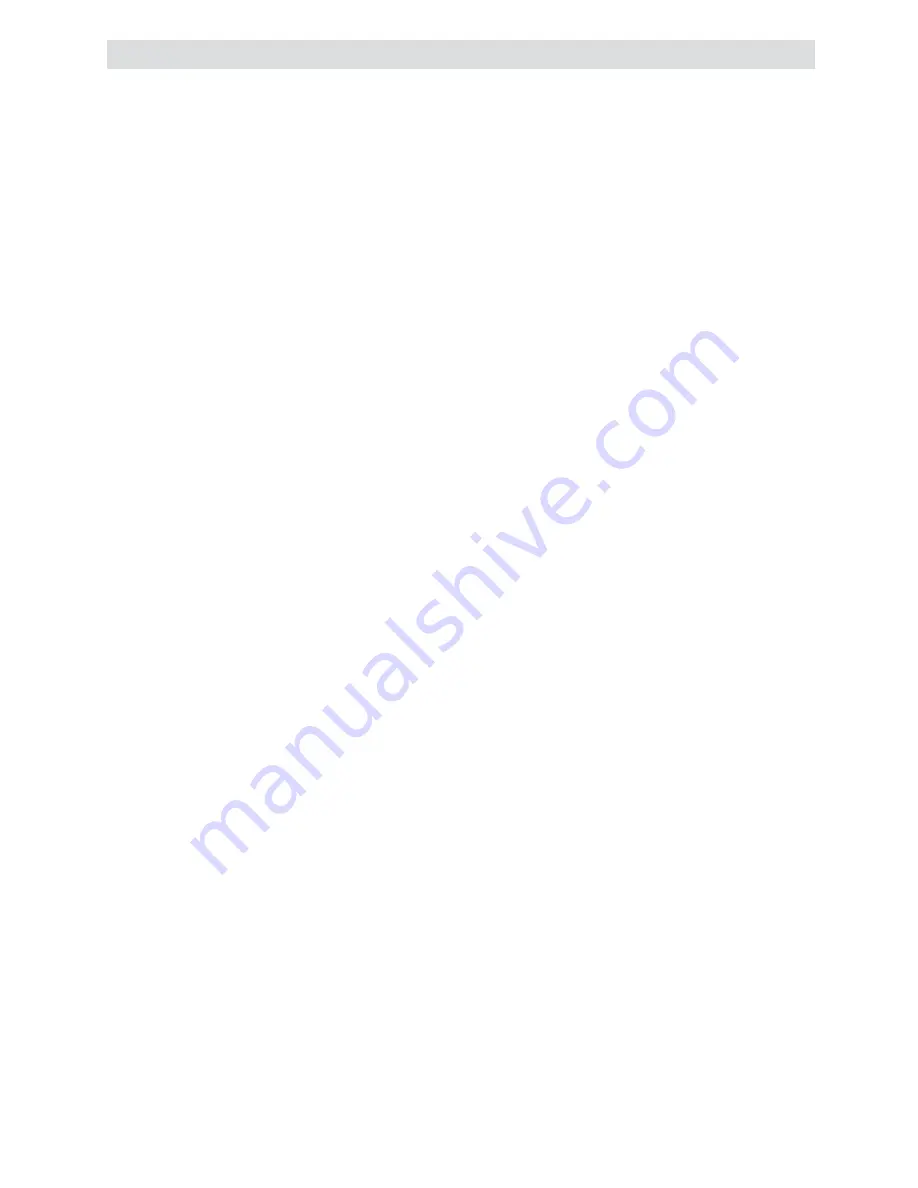
19
5.1 GAS SUPPLY INSTALLATION
Inspect the entire installation including the gas meter, test for
tightness and purge. Refer to BS 6891 (I.S. 813 in ROI) for
speci
fi
c instruction.
5.2 THE HEATING SYSTEM
The appliance contains components that may become damaged
or rendered inoperable by oils and/or debris that are residual
from the installation of the system, consequently it is essential
that the system be
fl
ushed in accordance with the following
instructions.
5.3 INITIAL FILLING OF THE SYSTEM
Ensure both
fl
ow and return service valves are open, remove
appliance casing as described in 4.7.1, identify the automatic air
release valves (AAV) and loosen the dust cap/s by turning the
cap anti-clockwise one full turn. Ensure all manual air release
valves located on the heating system are closed. Connect the
fi
lling loop as shown in
fi
g. 8, slowly proceed to
fi
ll the system
by
fi
rstly opening the inlet valve connected to the
fl
ow pipe, and
then turning the lever on the
fi
ll valve, to the open position. As
water enters the system the pressure gauge will begin to rise.
Once the gauge has reached 1 BAR close both valves and begin
venting all manual air release valves, starting at the lowest
fi
rst.
It may be necessary to go back and top-up the pressure until
the entire system has been
fi
lled. Inspect the system for water
tightness, rectifying any leaks.
5.4 INITIAL FLUSHING OF THE SYSTEM
The whole of the heating system must be
fl
ushed both cold
and hot as detailed in 5.8. Open all radiator or heating valves
and the appliance
fl
ow & return service valve. Drain the boiler
and system from the lowest points. Open the drain valve full
bore to remove any installation debris from the boiler prior to
lighting. Re
fi
ll the boiler and heating system as described in 5.3.
5.5 PRE-OPERATION CHECKS
Before attempting the initial lighting of the appliance, the fol-
lowing checks must be carried out:
• ensure all gas service valves from the meter to the applian-
ce are open and the supply pipe has been properly purged;
• ensure the proper electrical checks have been carried out,
(see 7.8) particularly continuity, polarity and resistance to
earth;
• ensure the 3 AMP fuse – supplied with the appliance – has
been
fi
tted;
• ensure the system has been
fi
lled, vented and the pressure
set to 1 BAR;
• ensure the
fl
ue system has been
fi
tted properly and in ac-
cordance with the instructions;
• ensure all appliance service valves are open.
5.6 INITIAL LIGHTING
Ensure the electrical supply to the appliance is switched on.
Ensure any external controls are switched to an ‘ON’ position
and are calling for heat. Move the selector switch to the ON
position, the appliance will now operate as described in 1.2.
Should the appliance fail to ignite, refer to 5.6 and/or section 7
(mode of operation & fault
fi
nding).
5.7 CHECKING GAS PRESSURE AND COMBUS-
TION ANALYSIS
The appliance is factory set so should require no additional
adjustment once installed. However to satisfy the require-
ments of GSIUR 26/9 (I.S. 813 ROI), it will be necessary to
gas rate the appliance using the gas meter that serves the
appliance and carry out a combustion analysis check in accor-
dance with BS 7967 (UK) to ensure that correct combustion is
occurring, see
fl
ow chart on page 38.
Additionally, if the gas valve has been adjusted, replaced, or
the appliance has been converted for use with another gas
type, then it becomes necessary to carry out a combustion
analysis check to ensure that correct combustion is occurring.
If there are no means to carry out a combustion analysis
check, then it will not be possible to complete the commissio-
ning procedure.
Details on how to carry out the combustion analysis can be
found in section 7.
IMPORTANT
It’s imperative that a suf
fi
cient dynamic – gas – pressure is
maintained at all times. Should the dynamic gas pressure fall
below an acceptable level, the appliance may malfunction or
sustain damage.
5.8 FINAL FLUSHING OF THE HEATING SYSTEM
The system shall be
fl
ushed in accordance with BS 7593 (I.S.
813 ROI). Should a cleanser be used, it must be suitable for
Aluminium heat exchangers. It shall be from a reputable manu-
facturer and shall be administered in strict accordance with the
manufacturers’ instructions and the DWTA code of practice.
NOTE
Chemicals used to cleanse the system and/or inhibit corrosion
must be pH neutral, i.e. they should ensure that the level of the
pH in the system water remains neutral. Premature failure of
certain components can occur if the level of pH in the system
water is out-with normal levels.
5.8.1 INHIBITORS
See Section 3 “General Requirements”.
5.9 SETTING THE FLOW OUTLET TEMPERA-
TURE
The
fl
ow outlet temperature can be adjusted between 40 °C -
80 °C for standard CH system by using the Heating thermostat
knob (see
fi
g.1).
5.9.1 SETTING THE DHW OUTLET TEMPERATURE
The DHW outlet temperature can be adjusted between 37 °C
- 60 °C via the DHW thermostat knob (see
fi
g.1).
5.10 SETTING THE SYSTEM DESIGN PRESSURE
The design pressure should be a minimum of 0.5 BAR and a
maximum of 1.5 BAR. The actual reading should ideally be 1
BAR plus the equivalent height in metres (0.1 BAR = 1 metre) to
the highest point in the system above the base of the appliance
(up to the maximum of 1.5 BAR total).
N.B.
The safety valve
is set to lift at 3 BAR/30 metres/45 psig. To lower the system
pressure to the required value, drain off some water from the
appliance drain valve until the required
fi
gure registers on the
pressure gauge (see
fi
g. 1).
5.11 REGULATING THE CENTRAL HEATING
SYSTEM
Fully open all radiator and circuit valves and run the appliance
for both heating and hot water until heated water is circulating.
If conditions are warm remove any thermostatic heads. Adjust
radiator return valves and any branch circuit return valves
until the individual return temperatures are correct and are
approximately equal.
5.11.1 REGULATING THE DHW FLOW-RATE
The appliance is
fi
tted with a
fl
ow rate restrictor that limits the
maximum
fl
ow rate that can be drawn through the appliance.
The restrictor eliminates the need to manually adjust the DHW
fl
ow rate. However if it is felt necessary to further increase or
decrease the available
fl
ow rate, spare restrictors are available
from Vokèra spare parts.
The spare
fl
ow rate restrictors can be
fi
tted to either increase
or decrease the maximum
fl
ow rate.
SECTION 5 - COMMISSIONING