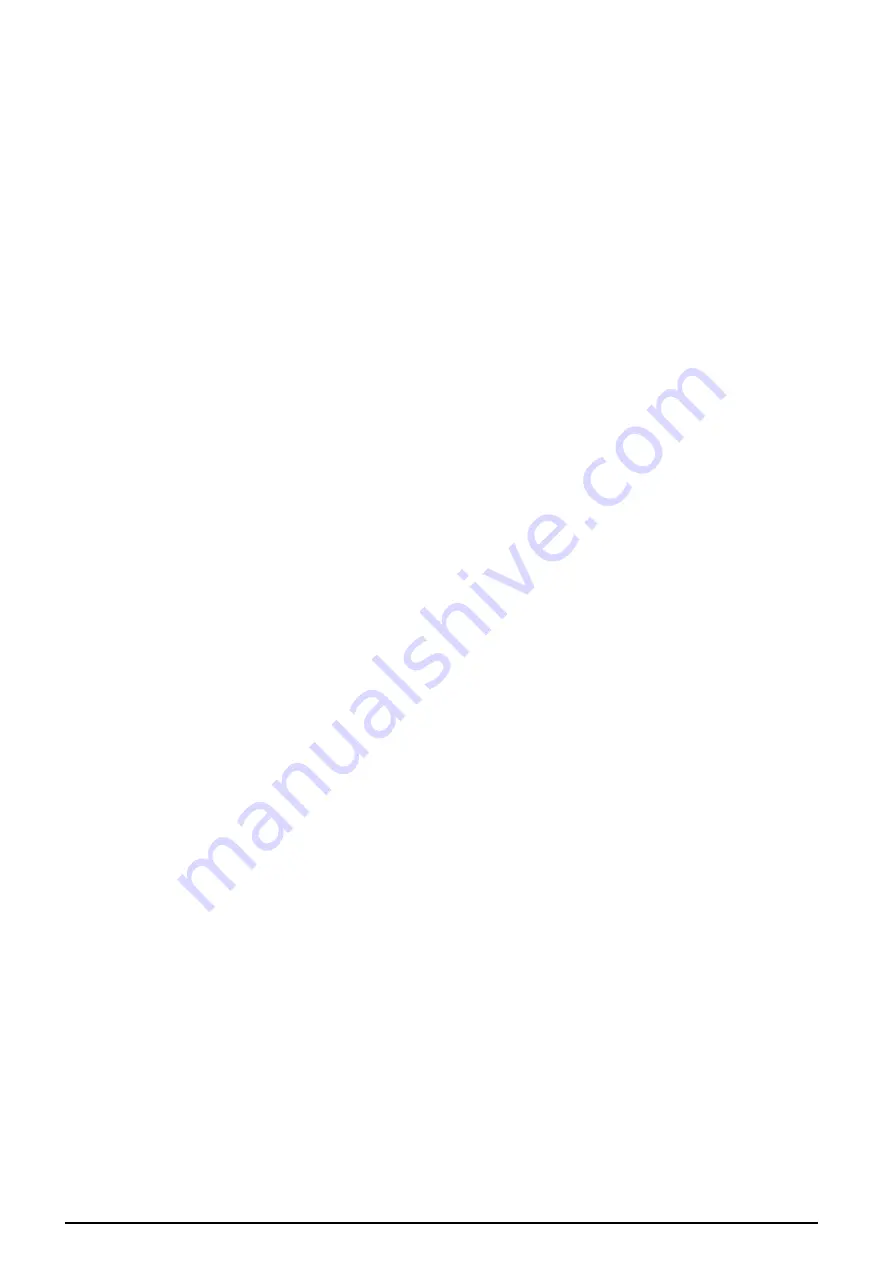
7
Mynute
the provision of a safe and satisfactory flue and
termination. The location must also permit an
adequate air supply for combustion purposes
and an adequate space for servicing and air
circulation around the appliance. Where the
installation of the appliance will be in an unusual
location special procedures may be necessary,
refer to I.S. 813 for detailed guidance on this
aspect.
A compartment used to enclose the appliance
must be designed and constructed specifically
for this purpose. An existing compartment/
cupboard may be utilised provided that it is
modified to suit.
This appliance is not suitable for external
installation.
3A.3
GAS SUPPLY
The gas meter – as supplied by the gas supplier
– must be checked to ensure that it is of adequate
size to deal with the maximum rated input of all
the appliances that it serves. Installation pipes
must be fitted in accordance with I.S. 813.
Pipe work from the meter to the appliance must
be of adequate size. Pipes of a smaller size than
the appliance gas inlet connection must not be
used. The installation must be tested for
soundness in accordance with I.S. 813.
If the gas supply serves more than one appliance,
it must be ensured that an adequate supply is
maintained to each appliance when they are in
use at the same time.
3A.4
FLUE SYSTEM
The terminal should be located where the dispersal
of combustion products is not impeded and with
due regard for the damage and discoloration that
may occur to building products located nearby.
The terminal must not be located in a place where
it is likely to cause a nuisance (see I.S. 813).
In cold and/or humid weather, water vapour may
condense on leaving the terminal; the effect of
such pluming must be considered.
If installed less than 2m above a pavement or
platform to which people have access (including
balconies or flat roofs) the terminal must be
protected by a guard of durable material. The
guard must be fitted centrally over the terminal.
Refer to I.S. 813, when the terminal is 0.5 metres
(or less) below plastic guttering or 1 metre (or
less) below painted eaves.
3A.5
AIR SUPPLY
The following notes are intended for general
guidance only.
This appliance is a room-sealed, fan-flued boiler,
consequently it does not require a permanent air
vent for combustion air supply.
When installed in a cupboard or compartment,
ventilation for cooling purposes is also not
required.
3A.6
WATER CIRCULATION
Specific recommendations are given in I.S. 813.
The following notes are for general guidance
only.
3A.6.1 PIPEWORK
It is recommended that copper tubing be used in
conjunction with soldered capillary joints.
Where possible pipes should have a gradient to
ensure air is carried naturally to air release points
and that water flows naturally to drain cocks.
Except where providing useful heat, pipes should
be insulated to avoid heat loss and in particular to
avoid the possibility of freezing. Particular attention
should be paid to pipes passing through ventilated
areas such as under floors, loft space, and void
areas.
3A.6.2 AUTOMATIC BY-PASS
The appliance has a built-in automatic by-pass,
consequently there is no requirement for an
external by-pass, however the design of the
system should be such that it prevents boiler
‘cycling.
3A.6.3 DRAIN COCKS
These must be located in accessible positions to
facilitate draining of the appliance and all water
pipes connected to the appliance.
3A.6.4 AIR RELEASE POINTS
These must be positioned at the highest points in
the system where air is likely to be trapped. They
should be used to expel trapped air and allow
complete filling of the system.
3A.6.5 EXPANSION VESSEL
The appliance has an integral expansion vessel
to accommodate the increased volume of water
when the system is heated. It can accept up to 10
litres of expansion from within the system,
generally this is sufficient, however if the system
has an unusually high water content, it may be
necessary to provide additional expansion
capacity.
3A.6.6 FILLING POINT
A method for initial filling of the system and
replacing water lost during servicing etc. must be
provided. A typical arrangement is shown in
figure 5. You should ensure this method of filling
complies with the local water authority regulations.
3A.6.7 LOW PRESSURE SEALED SYSTEM
An alternative method of filling the system would
be from an independent make-up vessel or tank
mounted in a position at least 1 metre above the
highest point in the system and at least 5 metres
above the boiler (fig. 5).
The cold feed from the make-up vessel or tank
must be fitted with an approved non-return valve
and stopcock for isolation purposes. The feed
pipe should be connected to the return pipe as
close to the boiler as possible.
3A.6.8 FREQUENT FILLING
Frequent filling or venting of the system may be
indicative of a leak. Care should be taken during