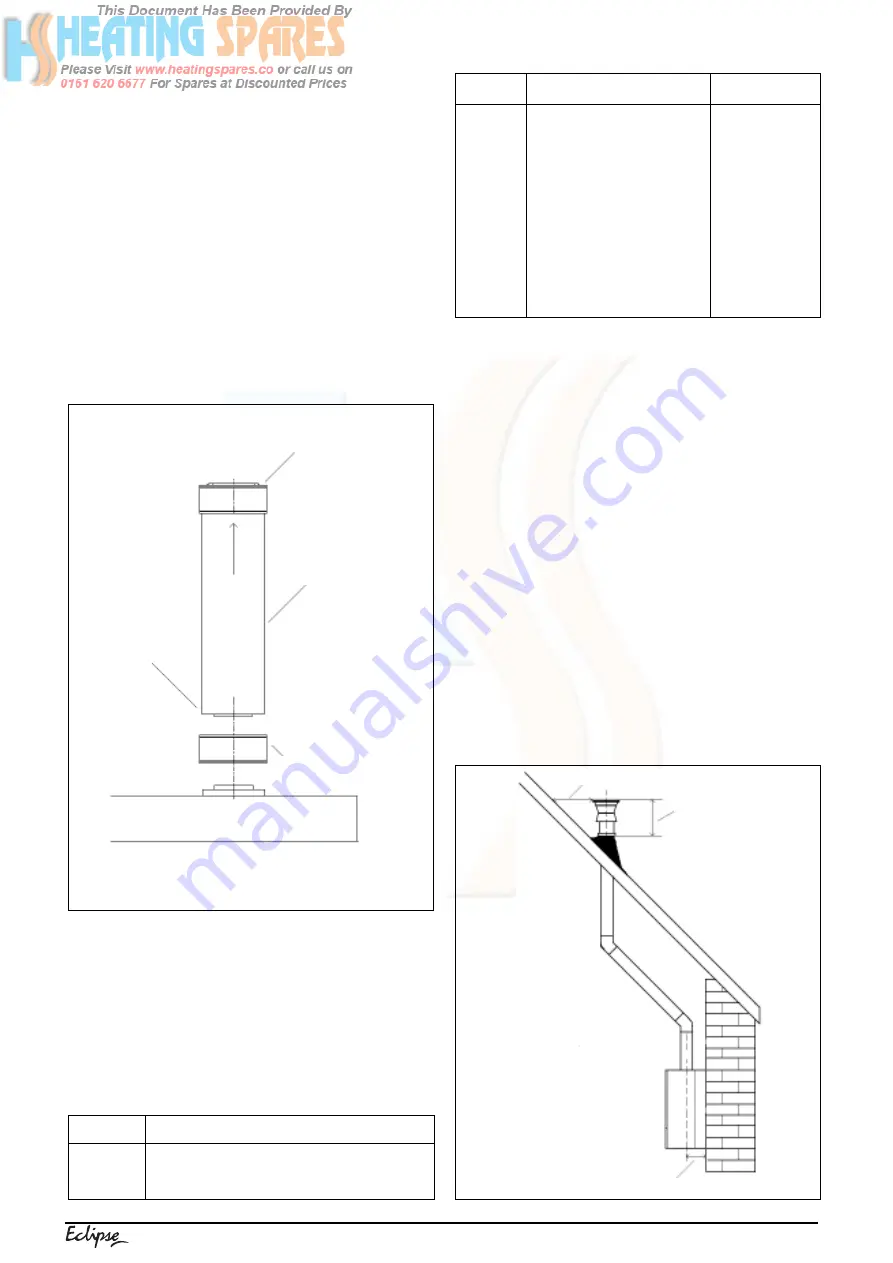
Supplied By www.heating spares.co Tel. 0161 620 6677
9
4.5.2
CONCENTRIC VERTICAL FLUE
The vertical flue terminal can be connected directly
to the appliance flue outlet. Alternatively, an
extension or bend can be connected to the
appliance flue outlet if desired (see 2.9), however
if additional bends are fitted, a reduction must be
made to the maximum flue length (see table
below).
Vertical flue terminal and accessories
Part No.
Description
Min-Max length
0225725
0225770
0225765
0225755
0225740
0225745
0225750
0225730
0225735
0225760
Vertical flue terminal
Pitched roof flashing plate
Flat roof flashing plate
350-500 telescopic extension
0,5m extension
1,0m extension
2,0m extension
45
°
bend (pair)
90
°
bend
Wall bracket (4)
1000 mm
N/A
N/A
350mm-500mm
500mm
1000mm
2000mm
N/A
N/A
N/A
4.5.1.1 EXTENDING THE FLUE
Connect the bend – supplied with the terminal kit
– to the top of the boiler using the boiler top
adapter (supplied, see fig. 7). The additional
bends & extensions have push-fit connections,
care should be taken to ensure that the correct
seal is made when assembling the flue system.
Connect the required number of flue extensions
or bends (up to the maximum equivalent flue
length) to the flue terminal (see fig. 7B & 7C).
NOTE
When cutting an extension to the required length,
you must ensure that the excess is cut from the
plain end of the extension (see fig. 7B & 7C).
Remove any burrs, and check that any seals are
located properly.
You must ensure that the entire flue system is
properly supported and connected.
Fig. 7C
Reduction in maximum flue length for each bend
Reduction for bends
Bend
45
°
bend
90
°
bend
0,5 metre
1,0 metre
Using the dimensions given in fig. 8 as a reference,
mark and cut a 105mm hole in the ceiling and/or roof.
IMPORTANT
You must ensure that the terminal is at least
300mm from any structure or surface (see fig. 8).
The vertical flue terminal is 1,0 metre in length
and cannot be cut; therefore it may be necessary
to adjust the height of the appliance to suit or use
a suitable extension.
Encure that any horizontal sections of the flue
system have a 1
°
fall back to the boiler (17mm per
1000mm).
Fit the appropriate flashing plate to the roof and
insert the vertical flue terminal through the flashing
plate from the outside, ensuring that the collar on
the flue terminal fits over the flashing.
The fixing holes for the wall-mounting bracket
should now be drilled and plugged, an appropriate
type and quantity of fixing should be used to
ensure that the bracket is mounted securely.
Once the bracket has been secured to the wall,
mount the appliance onto the bracket.
Fig. 8
Push-fit connection
Boiler
Extension pipe
Boiler top adaptor
Plain end
520mm
300mm minimum
139mm