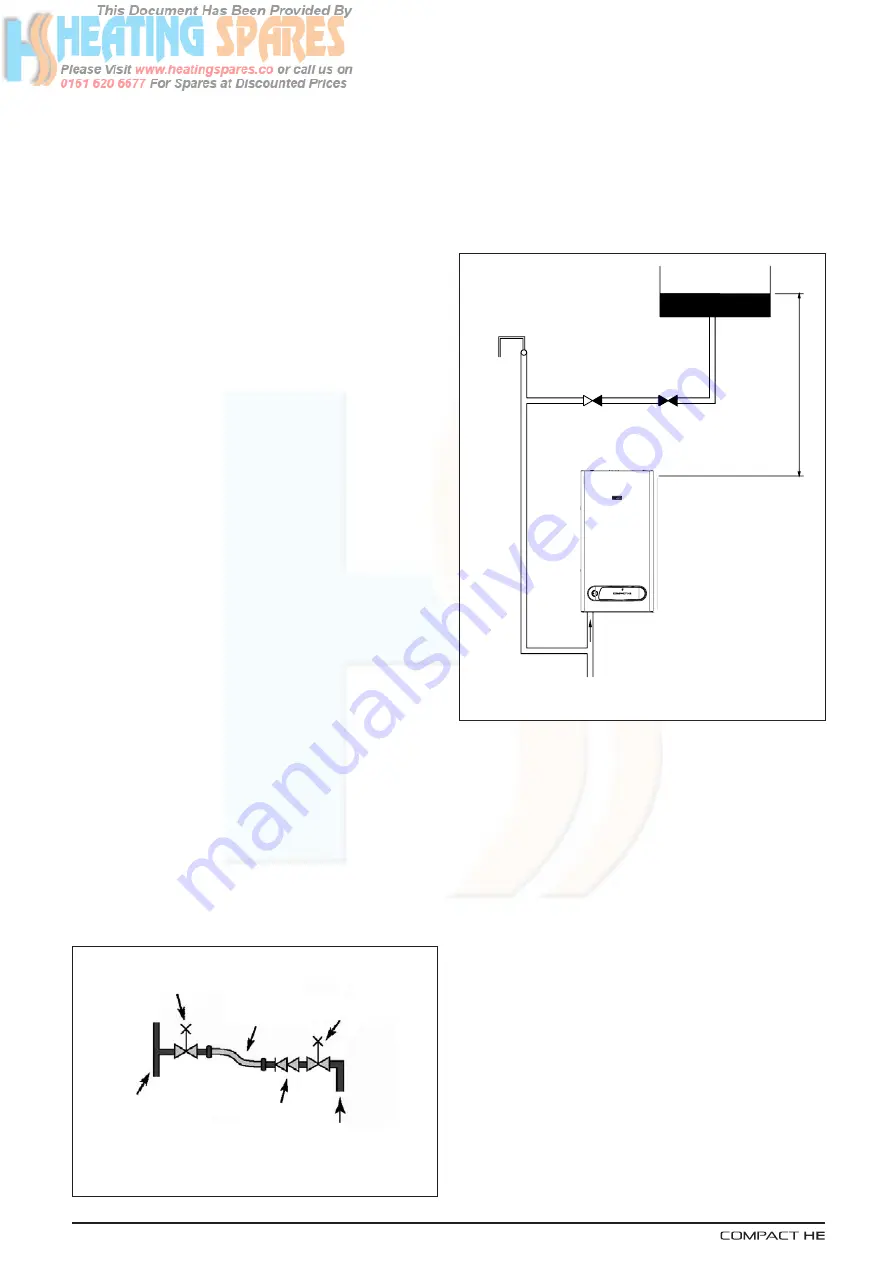
Supplied By www.heating spares.co Tel. 0161 620 6677
6
Fig. 5a
3.6.7
LOW PRESSURE SEALED SYSTEM
An alternative method of filling the system would
be from an independent make-up vessel or tank
mounted in a position at least 1 metre above the
highest point in the system and at least 5 metres
above the boiler (see fig. 5a).
The cold feed from the make-up vessel or tank
must be fitted with an approved non-return valve
and stopcock for isolation purposes. The feed
pipe should be connected to the return pipe as
close to the boiler as possible.
3.6.8
FREQUENT FILLING
Frequent filling or venting of the system may be
indicative of a leak. Care should be taken during
the installation of the appliance to ensure all
aspects of the system are capable of withstand-
ing pressures up to at least 3 bar.
3.7
ELECTRICAL SUPPLY
The appliance is supplied for operation on 230V
@ 50Hz electrical supply; it must be protected
with a 3-amp fuse. The method of connection to
the mains electricity supply must allow for com-
plete isolation from the supply. The preferred
method is by using a double-pole switch with a
contact separation of at least 3mm. The switch
must only supply the appliance and its corre-
sponding controls, i.e. time clock, room thermo-
stat, etc. Alternatively an un-switched shuttered
socket with a fused 3-pin plug both complying
with BS 1363 is acceptable.
3.8
SHOWERS
If the appliance is intended for use with a shower,
the shower must be thermostatically controlled
and be suitable for use with a combination boiler.
3.6.1
PIPEWORK
It is recommended that copper tubing to BS 2871
Part 1 is used in conjunction with soldered capil-
lary joints.
Where possible pipes should have a gradient to
ensure air is carried naturally to air release points
and that water flows naturally to drain cocks.
Except where providing useful heat, pipes should
be insulated to avoid heat loss and in particular to
avoid the possibility of freezing. Particular atten-
tion should be paid to pipes passing through
ventilated areas such as under floors, loft space,
and void areas.
3.6.2
AUTOMATIC BY-PASS
The appliance has a built-in automatic by-pass.
However it may be necessary to fit an external
bypass should the design of the heating system
require such. In any case, the design of the
system should be such that it prevents boiler
‘cycling’.
3.6.3
DRAIN COCKS
These must be located in accessible positions to
facilitate draining of the appliance and all water
pipes connected to the appliance. The drain
cocks must be manufactured in accordance with
BS 2879.
3.6.4
AIR RELEASE POINTS
These must be positioned at the highest points in
the system where air is likely to be trapped. They
should be used to expel trapped air and allow
complete filling of the system.
3.6.5
EXPANSION VESSEL
The appliance has an integral expansion vessel
to accommodate the increased volume of water
when the system is heated. It can accept up to 8
litres (25kW) or 10 litres (29 & 35kW) of expan-
sion from within the system, generally this is
sufficient, however if the system has an unusu-
ally high water content, it may be necessary to
provide additional expansion capacity (see 6.19).
3.6.6
FILLING POINT
An approved method for initial filling of the system
and replacing water lost during servicing etc. is
required (see fig. 5). This method of filling must
comply with the current Water Supply (Water
Fittings) Regulations 1999 and Water Bylaws
2000 (Scotland).
Fig. 5
control valve
temporary
connection
control valve
supply pipe
double check
valve
flow/return
pipe
Make-up vessel
or tank
Automatic
air-vent
Non-return
valve
Stopcock
5.0 metres minimum
Heating
return