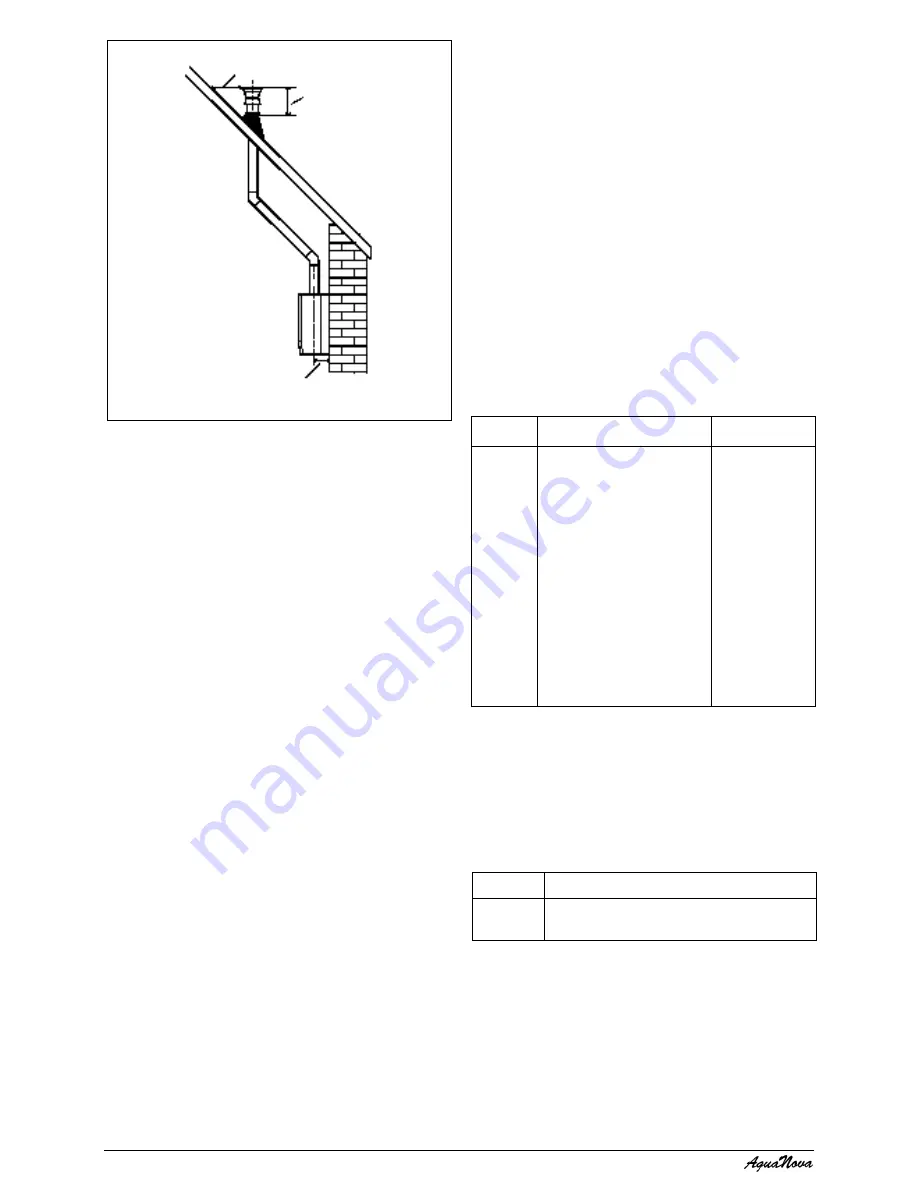
8
Fig. 9
Twin flue accessories
Part No.
Description
Length
0225805
0225810
300
0225770
0225765
0225815
0225820
0225825
0225830
0225835
0225840
0225845
0225850
0225855
Horizontal flue terminal
Vertical flue terminal
Concentric to twin, adapter
Pitched roof flashing plate
Flat roof flashing plate
Condensate drain kit
0,25m extension (pair)
0,5m extension (pair)
1,0m extension (pair)
2,0m extension (pair)
45
°
bend (pair)
90
°
bend (pair)
Twin bracket (5)
Single bracket (5)
1000 mm
1000 mm
N/A
N/A
N/A
N/A
250mm
500mm
1000mm
2000mm
N/A
N/A
N/A
N/A
166mm
465mm
300mm minimum
The vertical flue terminal is 1.0 metre in length
and cannot be cut; therefore it may be necessary
to adjust the height of the appliance to suit or use
a suitable extension.
Remove or discard the flue restrictor ring from the
appliance flue outlet (see fig. 1), if the total flue
length - including the allowance for any additional
bends - exceeds 1.0 metre.
Connect the vertical flue assembly to the water
heater flue spigot using the 60mm & 100mm clips,
gaskets & screws (supplied), ensuring the correct
seal is made. The flue support bracket (supplied
with the vertical flue kit) can now be fitted.
If the vertical flue requires extension/s or additional
bend/s, connect the required number of flue
extensions or bends (up to the maximum
equivalent flue length) between the water heater
and vertical flue assembly (see fig. 8).
NOTE
When cutting an extension to the required length,
you must ensure that the excess is cut from the
plain end of the extension and that the inner
(60mm) pipe is 7,5mm longer than outer (100mm)
pipe (see fig. 8). Remove any burrs, and check
that any seals are located properly.
You must ensure that the entire flue system is
properly supported and connected.
4.5.3
TWIN FLUE SYSTEM
The Vokera twin flue system enables greater flue
distances to be achieved (see 4.4.2) than that of
the standard concentric flue system.
It can be used for horizontal or vertical
applications, however the twin flue system must
be converted to the dedicated concentric flue kit
for termination.
It is essential that the installation of the twin flue
system be carried out in strict accordance with
these instructions.
GUIDANCE NOTES ON TWIN FLUE
INSTALLATION
●
The flue must have a fall back of 1
°
back to the
appliance to allow any condensate that may form
in the flue system to drain via the condensate
drain. Consideration must also be given to the
fact that there is the possibility of a small amount
of condensate dripping from the terminal.
●
Ensure that the entire flue system is adequately
supported, use at least one bracket for each
extension.
●
The entire flue system must be adequately
insulated to maintain heat within the flue system
thereby reducing the possibility of condensate
production.
●
As the exhaust outlet pipe can reach very high
temperatures it must be protected to prevent
persons touching the hot surface.
●
The condensate drain pipe must be connected
in accordance with building regulations.
MOUNTING THE WATER HEATER
The fixing holes for the wall-mounting bracket
should now be drilled and plugged, an
appropriate type and quantity of fixing should be
used to ensure that the bracket is mounted
securely. Once the bracket has been secured to
the wall, mount the appliance onto the bracket.
4.5.3.1 INSTALLATION OF CONCENTRIC TO TWIN
ADAPTOR KIT (see fig. 10)
●
Remove the flue restrictor ring from the
appliance flue outlet (if fitted).
●
Using the two holes in the concentric section
of the adaptor as a guide, drill two - 3mm -
corresponding holes on the appliance flue
outlet.
●
Fit the adaptor to the appliance flue outlet and
secure it using the screws provided.
Reduction in maximum flue length for each bend
Reduction for bends
Bend
45
°
bend
90
°
bend
1,0 metre
1,0 metre