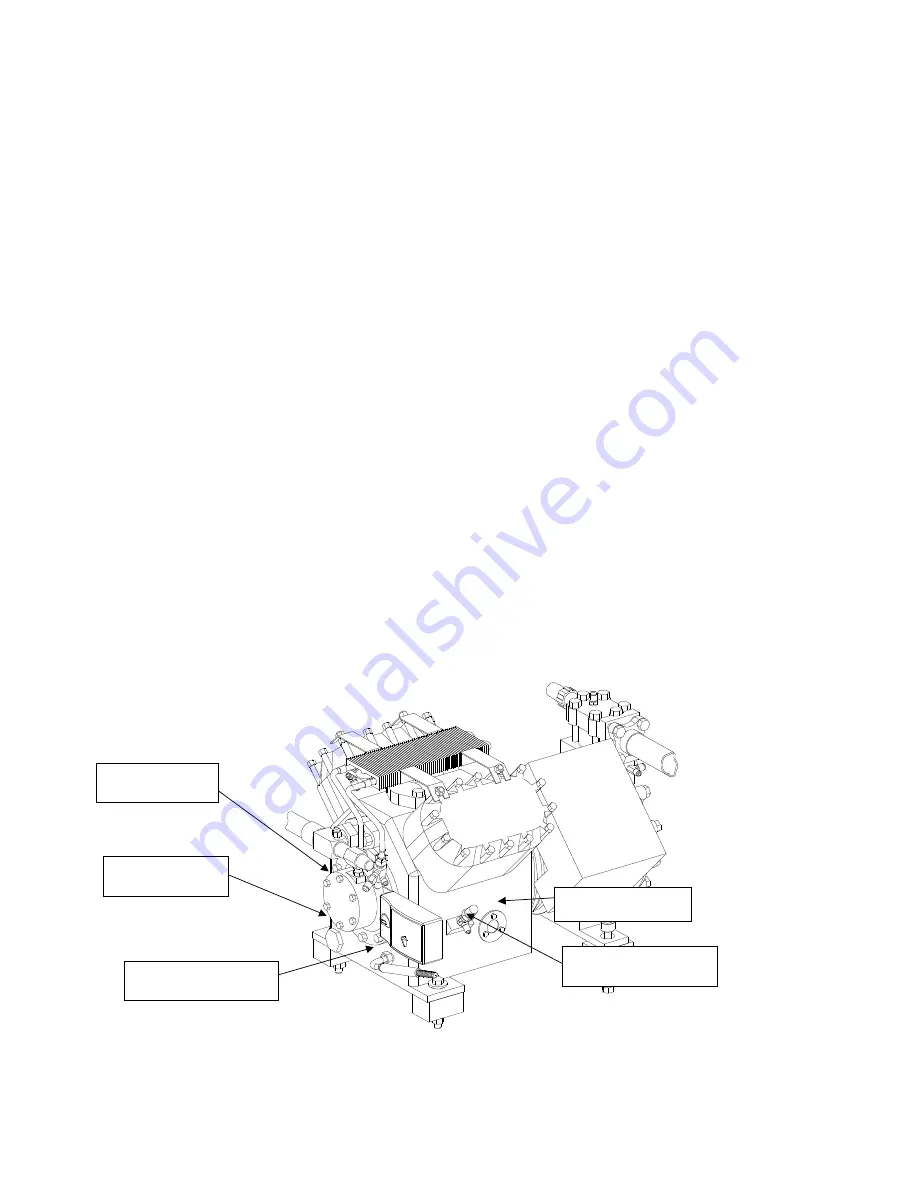
Vogt
®
VT Service Manual
6-3
Maintenance
Air-Cooled Condenser Cleaning.
Visual inspection will indicate if dirt is accumulating and clogging
the fin face of the condenser. A vacuum cleaner, compressed air, or a brush may be used to remove any
accumulation of loose dirt from the fin section of the condenser.
For the removal of more severe accumulations of dirt or foreign materials, a detergent-type cleaner can be
used. This cleaning agent can be supplied by your local refrigeration supply house. Follow the
manufacturer’s instructions when using a liquid cleaner.
If fins have been damaged, they should be straightened with the proper fin comb.
Compressor Oil.
In starting and charging the unit, the oil sight glass in the crankcase of the compressor
should be watched carefully for the first hour to make certain the proper lubrication is being maintained. The
oil may become low in the crankcase on an initial start-up if the electrical current has been interrupted to the
machine, thus de-energizing the compressor crankcase heater.
Before starting the machine again, the heater should be energized for a time period of at least two hours to
evaporate refrigerant that may have condensed in the crankcase during the shutdown period. If the oil level
is low after start-up, it should begin to return after a short period of operation.
The oil level should be checked frequently, particularly during the start-up operation, to see that a sufficient
amount of oil remains in the crankcase. While it is important to observe the oil splash during operation, the
true level can be obtained only when the compressor is stopped. With the compressor idle, the oil level
should be between 1/2 to 3/4 of the sight glass, but not above the top of the sightglass.
Although the machine was shipped with the oil charge, which was originally added for the test operation, it
may be necessary to add some oil when or if new refrigerant is added to the system.
An oil pump should be used to force any oil that may be required into the system. Oil may be added to the
compressor of all units through the compressor oil charging port. Air should be purged from the oil pump
discharge line by forcing some oil through the line before tightening the charging port.
R22 - Dual Inhibited Suniso 3GS (Viscosity 150) or equal.
R404A - Ultra 32 – 3MAF, Mobil EAL Arctic 22 CC or equal.
See page 3-1 for amount.
FIGURE 6-1
Copeland Discus Compressor (VT80)
Oil Sight Glass
Oil Charging valve
Oil Pump
Suction Screen
Crankcase Heater
Oil Pump
Summary of Contents for VT100
Page 1: ...VT Series Ice Maker Model VT40 VT60 VT80 VT100 Revision Date 1 04 12 ...
Page 21: ...2 14 Vogt VT Service Manual Installation Instructions Blank ...
Page 29: ...4 6 Vogt VT Service Manual Initial Startup Blank ...
Page 51: ...7 6 Vogt VT Service Manual Troubleshooting Blank ...
Page 71: ...8 20 Vogt VT Service Manual Service Operations Blank ...