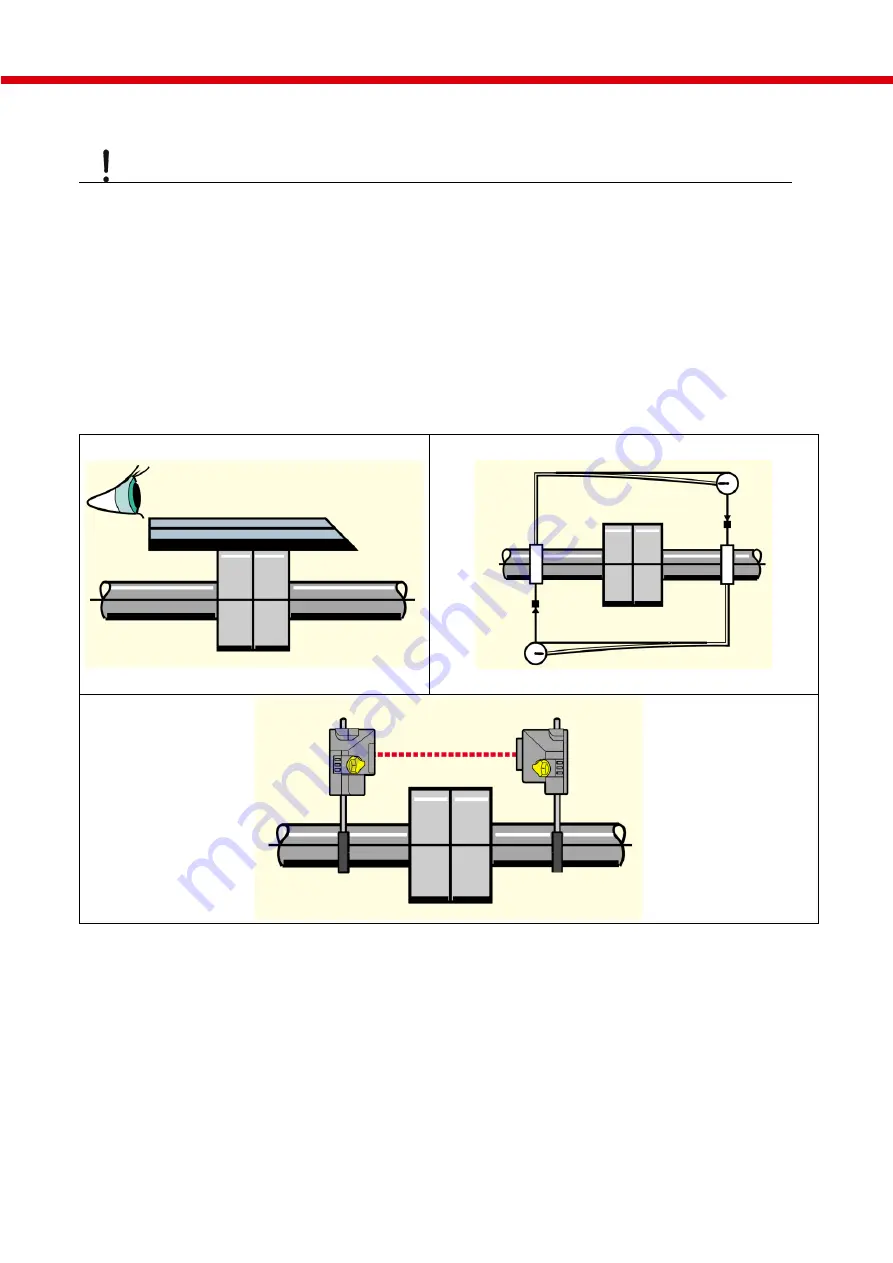
Asse mbl y
WBV.PU.003.EN FX116 V1.0
25
6.5.3
Coupling orientation
ATTENTION
Vibration and wear due to incorrectly oriented coupling!
If completely assembled at the Vogelsang plant, the alignment between the machine and the motor has been
optimally adjusted.
In the case of a drive provided by the operator, the tolerance specifications of the manufacturer of the
coupling must be complied with.
•
To protect the machine against damage caused by vibrations, check the orientation of the coupling
before start-up and then every 2000 operating hours (at least once a year) and correct it, as necessary
Fig.
"Orientation procedure".
•
If alignment errors are determined or after any blockage e.g. by foreign matter, check the function of
all parts of the drive line and readjust it, if necessary.
•
In the event of any unusual running noises or vibrations, check the coupling immediately, regardless of
the maintenance intervals.
Fig. 9: Orientation procedure