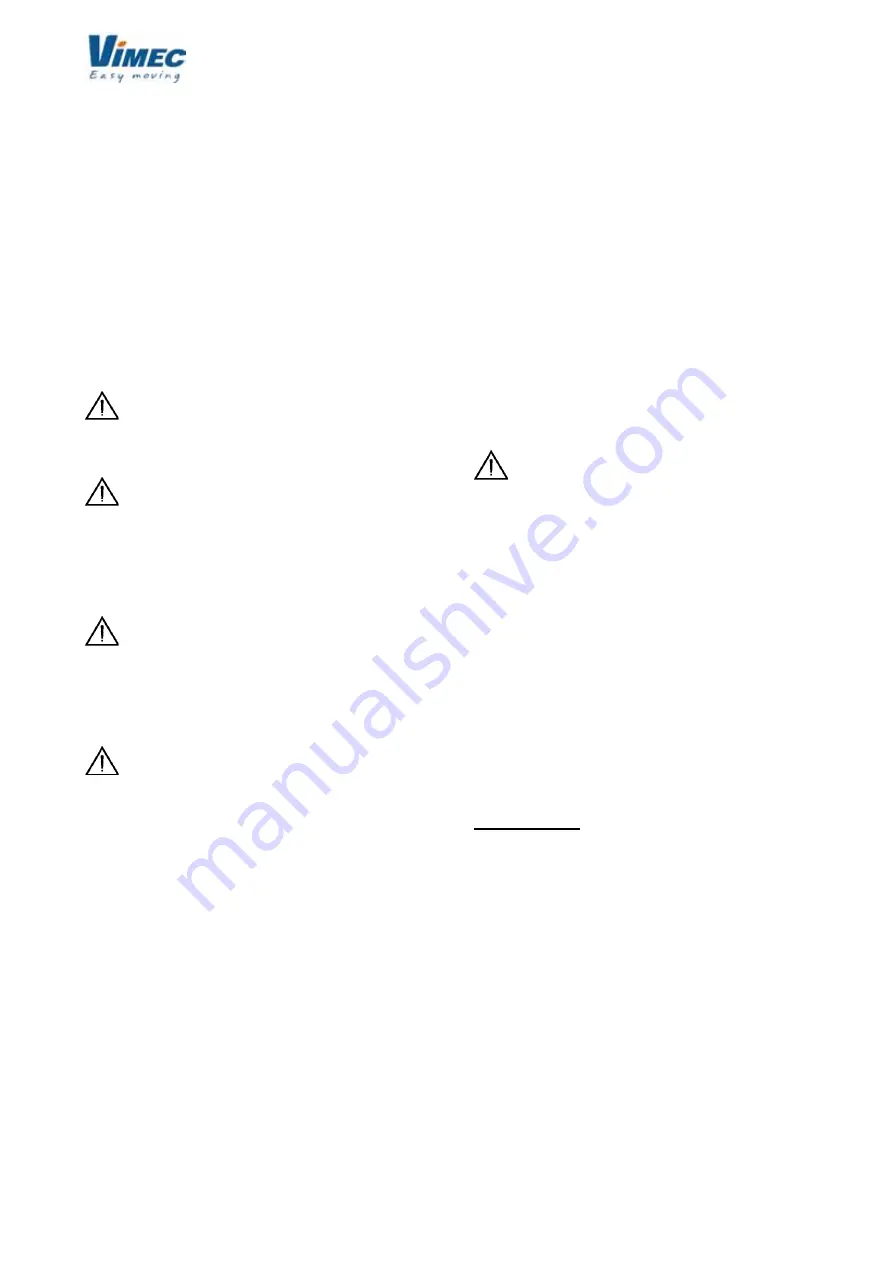
15
7502040
9) MAINTENANCE
VIMEC products are built in compliance with the current
Machinery Directive, that emphasizes the importance of
safety both in designing and building the machines, as
well as of proper installation and maintenance over time.
Therefore the product warranty is subject to an ordinary
and accurate maintenance of all safety devices and
guards. The maintenance service shall be carried out
by skilled technicians specially trained for this task, in
charge of performing the operations described below.
9.1) Precautions for long periods of disuse:
If the stairlift is to be left unused for a long time, switch
on the power supply to charge the batteries at least
every month.
WARNING: In all circumstances, only call in
authorised VIMEC after-sales staff for service and
repairs; use only genuine spare parts.
WARNING: Maintenance frequencies must be
complied with.
9.2) Parts requiring regular inspection
Skill level required: SO: Skilled operative authorised
by VIMEC.
WARNING: Before starting servicing work on
the rail or lift, disconnect the electricity by pulling
the power supply plug (Fig. 19/a) and taking care to
disconnect the battery on the lift. (Fig. 20/a).
Monthly checks:
WARNING: If the lift is used for more than 30
trips per day, check the mechanical drive compo-
nents, safety devices and parts subject to wear
and tear.
Six-monthly checks:
a) Safety devices
Make sure that on contact with an obstacle the anti-col-
lision and anti-shearing sensors stop the lift and allow
it to be restarted in the opposite direction.
Check that the lift stops in the required positions at
the floors.
b) Checking the interlocking of the platform
with independent or retractable arms (manual
platform)
Check that as long as the descent side arm is in the
rest position the platform remains locked, whether in
the working or the rest position.
c) Electromagnetic brake
The electromagnetic brake on the engine must stop
the lift, carrying the maximum working load, before the
final limit switch is tripped. If necessary, replace the
whole brake unit.
d) Drive mechanics
Check that the drive sprocket teeth and the lift’s nylon
wheels are not worn or damaged. There must be no
scoring or flattening of the wheels. Check the chain
for wear.
e) Safety gear
Check that the hook operates freely without friction or
excessive play, and trips the safety microswitch cor-
rectly.
To check that the safety gear is operating correctly,
proceed as follows
- Move the stairlift away from the floor (1-2 metres).
- Cut off the electricity by turning the master switch to
OFF.
- Remove the protective panel (Fig. 1/b).
- Press the safety gear hook with a plastic/wooden
rod.
WARNING: Keep well away from all unpro-
tected moving parts.
- Restore the power supply and press the down button
until the hook engages. The stairlift will stop when the
hook depresses the safety microswitch.
- Reset the safety gear by moving the stairlift upward
by hand (see point 7.6 ).
f) Stability of the rail
Check all the fixing screws which connect the rail to its
mounts and any expansion plugs used.
g) General checks
Check all moving parts, the guards, labels and signs.
Check the batteries and the warning lights of the power
supply unit.
h) Cleaning the rail
Clean the rail thoroughly.
Annual checks:
a) Controls
Check their operation by testing all the lift’s functions
using the control panel on the lift (and the control panels
at the floors, if installed).
Make sure that the system has not been tampered with
or modified.
b) Floor control panels
Check that these devices are operating correctly.
c) Electrical system
Check that all electrical components, contactors and
microswitches are operating correctly.
Check the continuity of the earth conductors.
Check that the lift does not tilt by more than 2°.Check
Check that the earth conductors are properly connected
to earth.
Summary of Contents for V65 B.I.
Page 47: ...47 7801186 servoscale CARRELLO INFERIORE ...
Page 66: ...66 7801189 servoscale BARRE DI SICUREZZA ...
Page 69: ...69 servoscale 7801190 BARRE DI SICUREZZA RETRATTILI ...
Page 75: ...75 servoscale 7801214 1 2 3 4 5 6 8 9 13 7 11 10 12 15 14 16 CONNETTORI ...
Page 77: ...77 7801192 servoscale GUIDA ...
Page 80: ...80 servoscale 7801193 1 3 3 2 4 SCHEDA DI CONTROLLO ...
Page 84: ...84 servoscale 7801222 4 2 3 1 5 6 8 7 14 12 11 11 13 9 10 GIUNZIONI GUIDE V65 ...