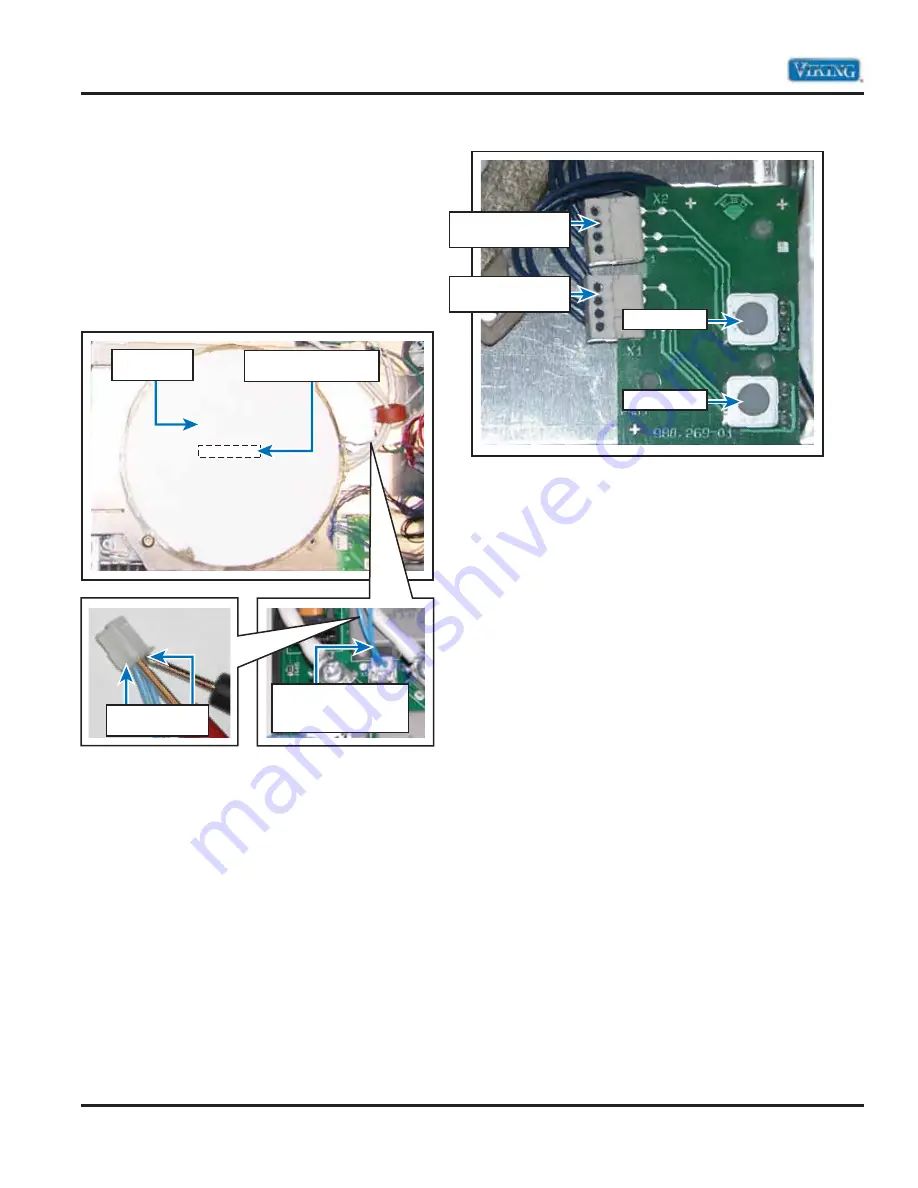
© 2009 Viking Preferred Service
27
Inductor
The inductor is similar to the surface element in a
normal cooking system. When the end user makes
a selection, the signal is sent to the filter board via
the interface. The filter board sends power to the
power board and in turn energizes the inductor.
This creates an electromagnetic field and allows an
electromagnetic transfer of energy from the inductor
to the cooking vessel which generates heat in the
vessel causing it to heat up rapidly.
The inductor has two blue wires that plug into the
power board. These wires go to the thermal sensor
which monitor glass temperature to prevent an
overheat situation. If an overheat situation occurs,
an E2 failure code will be displayed. If a failure of
the thermal sensor occurs, an E9 will be displayed.
Resistance should be approximately 990
Ω
when
unplugged from the power board. If resistance is
within range, verify voltage from the power board
position X5 or X4. If no power verify the inductor
leads are properly secured to the power board X6,
X8, X7, X9. If the inductor leads are secured and no
power out, replace the power board. If power out
and no heat, verify the cooking vessel is proper (a
common refrigerator magnetic will stick to it). If the
cooking vessel is proper, replace the inductor.
Indicator
The indicator serves as a means to ensure a pot is on
the cooking surface. The indicator will flash if no pot
is recognized or if an error is present.
LED flashes with pan detection and residual heat.
When cook top is off and residual heat is present,
the zone indicator flashes. In case of overheat
powerboard LED’s flash rapidly.
The indicator receives a signal at position X2 via a
four wire cable from the interface position X1. Verify
the cable is connected and ohm the wires end to
end. If continuity is present, check the switch and
interface. If both are OK, replace the indicator.
Service Diagnostics and Procedures
Inductor
Test Points
Thermal Sensor
Connection
Thermal Sensor
Input from Interface/
Induction Adapter
Input from Interface/
Induction Adapter
LED indicator
LED indicator