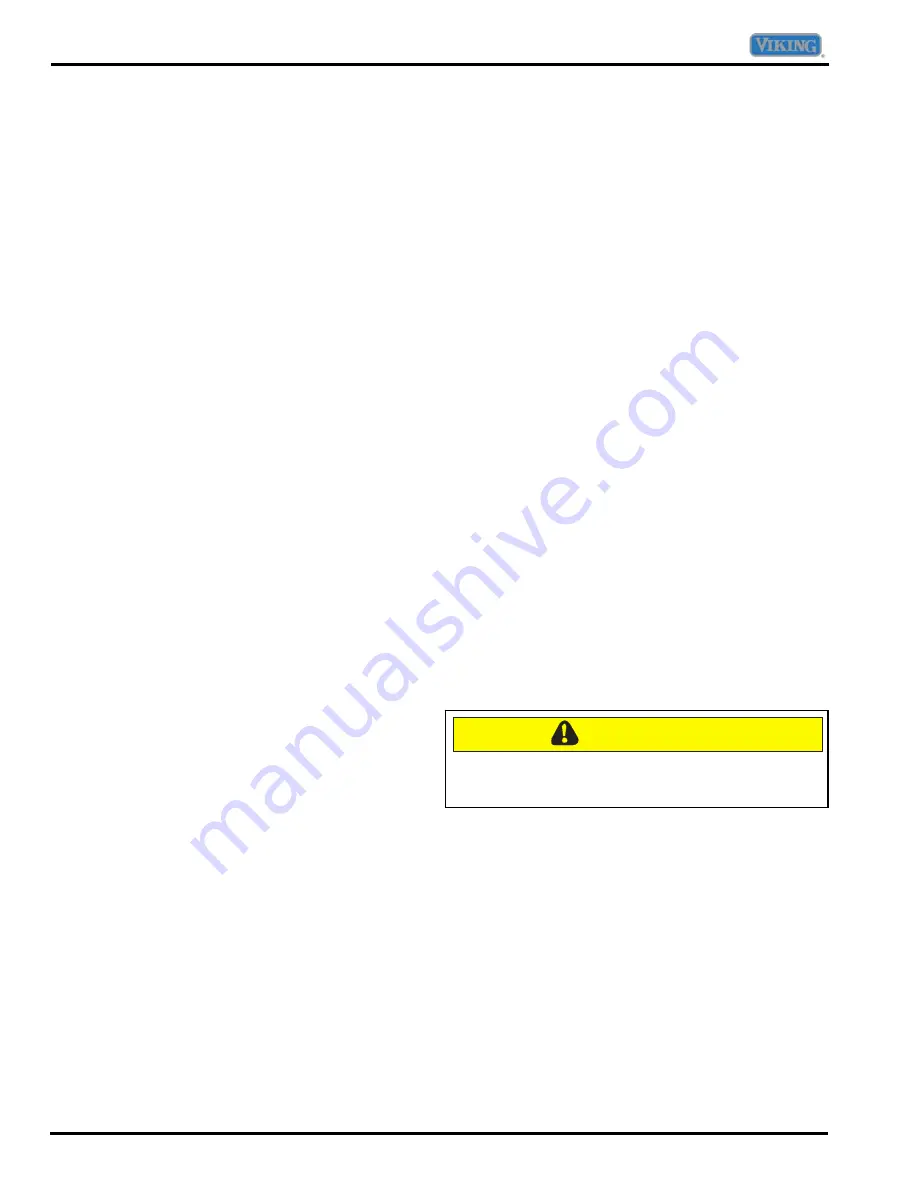
Service Procedure
32
©2007 Viking Preferred Service
Dehydrating Sealed Refrigeration System
Moisture in a refrigerator sealed system exposed to heat
generated by the compressor and motor reacts
chemically with refrigerant and oil in the system and
forms corrosive hydrochloric and hydrofluoric acids.
These acids contribute to breakdown of motor winding
insulation and corrosion of compressor working parts,
causing compressor failure.
In addition, sludge, a residue of the chemical reaction,
coats all surfaces of sealed system, and will eventually
restrict refrigerant flow through capillary tube.
To dehydrate sealed system, evacuate system (see
Evacuation).
Restrictions
Symptoms
Restrictions in sealed system most often occur at
capillary tube or filter drier, but can exist anywhere on
liquid side of system.
Restrictions reduce refrigerant flow rate and heat
removal rate. Wattage drops because compressor is not
circulating normal amount of refrigerants.
Common causes of total restrictions are moisture, poorly
soldered joints, or solid contaminants. Moisture freezes
at evaporator inlet end of capillary tube. Solid
contaminants collect in filter drier.
If restriction is on low side, suction pressure will be in a
vacuum and head pressure will be near normal.
If restriction is on high side, suction pressure will be in a
vacuum and head pressure will be higher than normal
during pump out cycle.
Refrigeration occurs on low pressure side of partial
restriction. There will be a temperature difference at the
point of restriction. Frost and/or condensation will be
present in most case at the point of restriction. Also,
system requires longer to equalize.
Slight or partial restriction can give the same symptoms
as refrigerant shortage including lower than normal back
pressure, head pressure, wattage, and warmer
temperatures.
Total restriction on the discharge side of compressor,
when restriction is between compressor and first half of
condenser, results in higher than normal head pressure
and wattage while low side is being pumped out.
Testing for Restrictions
To determine if a restriction exists:
1. Attach gauge and manifold between suction and
discharge sides of sealed system.
2. Turn unit on and allow pressure on each side to
stabilize. Inspect condenser side of system. Tubing
on condenser should be warm and temperature
should be equal throughout (no sudden drops at any
point along tubing).
•
If temperature of condenser tubing is consistent
throughout, go to step 4.
•
If temperature of condenser tubing drops suddenly
at any point, tubing is restricted at point of
temperature drop (if restriction is severe, frost may
form at point of restriction and extend down in
direction of refrigerant flow in system). Go to step 5.
3. Visually check system for kinks in refrigeration line
which is causing restriction. Correct kink and repeat
step 2.
4. Turn unit off and time how long it takes high and low
pressure gauges to equalize:
•
If pressure equalization takes longer than 10
minutes, a restriction exists in the capillary tube or
drier filter. Go to step 5.
•
If pressure equalization takes less than 10 minutes,
system is not restricted. Check for other possible
causes of malfunction.
5. Recover refrigerant in sealed system.
NOTE:
Before opening any refrigeration system,
capture refrigerant in system for safe disposal.
6. Remove power from unit.
CAUTION
To avoid risk of personal injury or property damage,
take necessary precautions against high
temperatures required for brazing.
7. Remove and replace restricted device.
8. Evacuate sealed system.
9. Charge system to specification.
NOTE:
Do not use captured or recycled refrigerant in
units. Captured or recycled refrigerant voids any
compressor manufacturer's warranty.
NOTE:
Charge system with exact amount of refrigerant.
Refer to unit nameplate for correct refrigerant
charge. Inaccurately charged system will cause
future problems.
Summary of Contents for DDBF036LSS
Page 18: ......
Page 50: ...Appendix A 50 2007 Viking Preferred Service NOTES ...