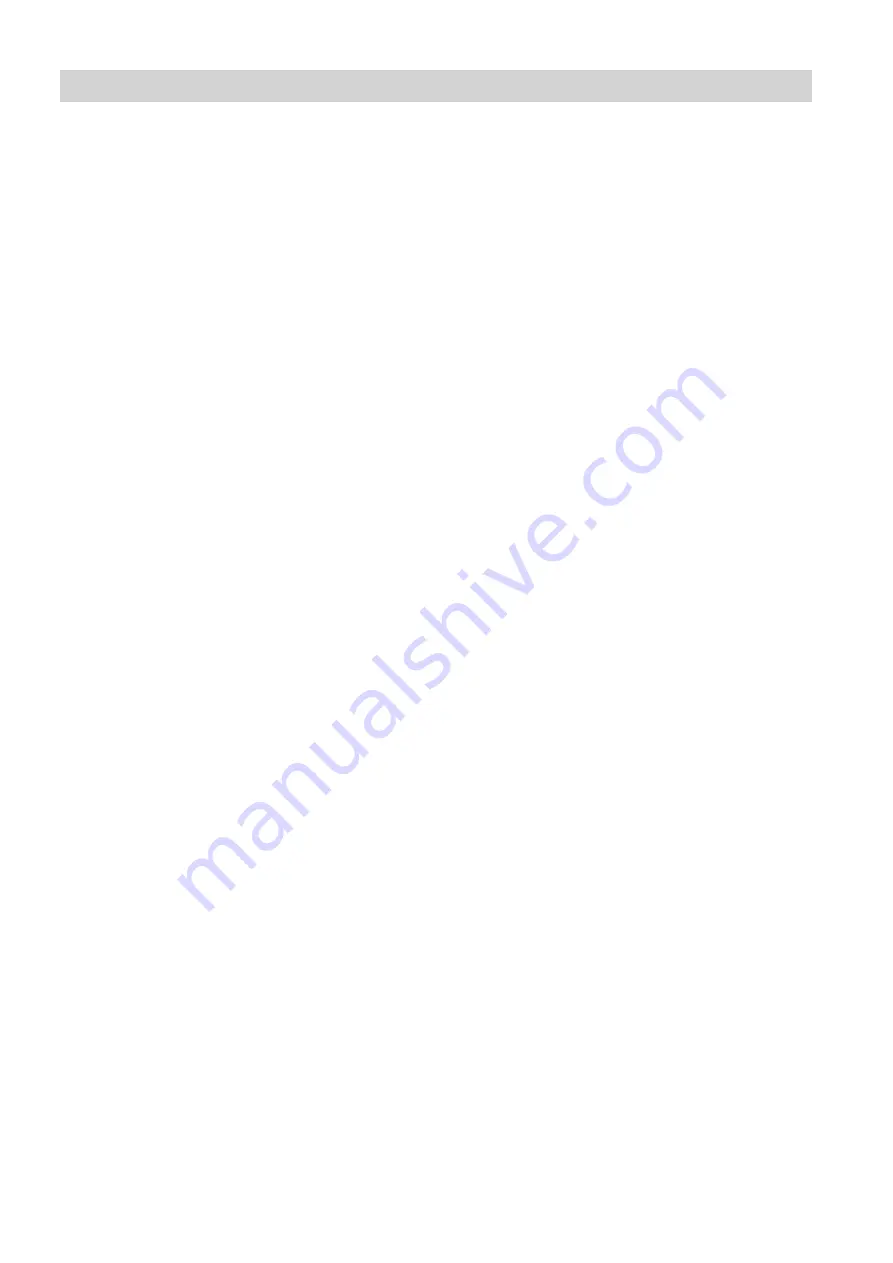
4
Only authorised personnel are permitted to enter the
boiler house.
Keep the boiler house clean at all times.
Do not store anything in the boiler house.
Keep exits clear.
Never use the boiler house or system components as
a drying area.
The operating personnel must log the following:
■
Settings
■
Readings
■
Faults
■
Replacement of spare parts
■
Repairs
Any defects must be dealt with immediately by trained
personnel, e.g.:
■
Abnormalities on weld seams
■
Leaks
■
Heavy corrosion
■
Faulty instrument displays
■
Noise in the boiler
Faults and defects that cannot be remedied locally
must be reported to the manufacturer. Protect all boiler
parts and control equipment from rain, water leaks and
expelled steam.
Safety instructions
Safety instructions
(cont.)
5673144
Summary of Contents for Vitomax LW M148 Series
Page 35: ...35 5673144...