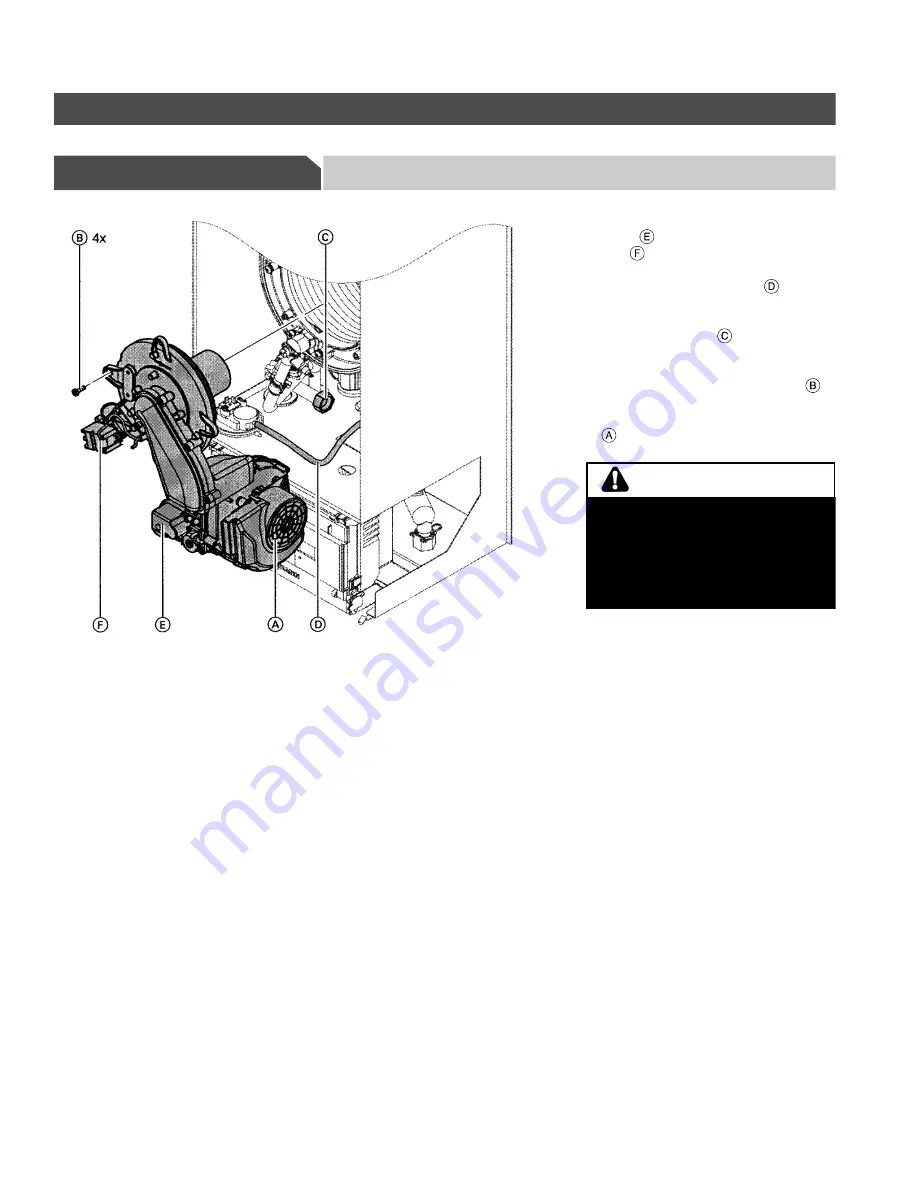
Initial Start-up, Inspection and Maintenance
54
Steps
(continued)
12. Remove burner (continued)
S
ervice
Maintenance
6.
Disconnect electrical cables from gas
valve
, and ignition transformer
unit
.
7.
Remove connection hose
from air
pressure switch.
8.
Loosen the fitting
on the gas
connection pipe.
9.
Loosen four Torx (T-30) screws
,
remove burner and disconnect all
electrical cables from blower motor
.
5
5
8
1
7
7
5
1
.3
To avoid damage to the burner, do
not lay burner on its cylindrical
burner tube.
Failure to heed this caution may
cause damage to the burner tube,
which may lead to improper
operation.
CAUTION